Moteurs modernes combustion interne sont constitués de plusieurs parties. Parmi eux, vous pouvez trouver des éléments complètement différents qui ont un objectif complètement différent, mais très utile pour le moteur. Un si petit détail qu'une pompe-buse ne fait pas exception. Dans cet article, nous analyserons l'appareil, le principe de fonctionnement et la réparation de la pompe - injecteur.
Le dispositif et le principe de fonctionnement de la pompe - buse
La buse est un tube métallique avec une section spéciale conçue pour la pulvérisation mélange de carburant. Pour la première fois à ce jour, un tel dispositif est utilisé sur des moteurs diesel, où des paramètres importants tels que l'efficacité du moteur, niveau faible son bruit et sa faible toxicité les gaz d'échappement.
La pompe d'injection est installée au-dessus de chaque cylindre et a la même structure. Il se compose généralement de : un piston d'arrêt, un piston spécial, une aiguille de dispositif de pulvérisation, une soupape de contrôle et de contrôle et un ressort de dispositif de pulvérisation.
Le piston est une pièce qui crée une certaine pression à l'intérieur de la buse. Le pompage se produit pendant le mouvement vers l'avant du piston. Pour ce faire, il y a des cames spéciales sur l'arbre à cames qui, à certains moments, agissent sur le piston et l'actionnent.
La soupape de commande s'ouvre avec le mouvement du piston et fait passer le carburant dans la chambre de combustion. La conception de la soupape est choisie de manière à ce que le carburant diesel soit nécessairement fourni sous forme atomisée. Ainsi, il brûle plus efficacement et économiquement. Selon le principe de fonctionnement, les vannes de régulation peuvent être divisées en électromagnétique et piézoélectrique. Vannes piézo sont les plus efficaces, car ils fonctionnent rapidement et ne permettent pas la formation d'un excès de carburant, ainsi que sa famine dans certaines zones du système d'injection. L'élément principal de toute vanne de régulation est son aiguille, qui est précisément responsable de la vitesse du système.
Le ressort de l'atomiseur est installé pour assurer un ajustement serré de l'aiguille. La force du ressort est généralement complétée par la pression de carburant créée dans la pompe à carburant. haute pression. Pour ce faire, un piston d'arrêt spécial est installé du côté opposé du ressort, qui appuie dessus sous l'influence du carburant.
Le contrôle de tout injecteur-pompe est assuré à l'aide de . L'ECU reçoit diverses lectures de tous les capteurs, les analyse et, en fonction des données reçues, ouvre ou ferme les injecteurs à certains moments.
Principe d'opération:
- Pré-injection. À ce stade, une came de synchronisation spéciale agit sur le piston, le faisant descendre. Le mélange de carburant et d'air passe dans les canaux de la buse et le clapet anti-retour se ferme. Le piston crée une pression de 13 MPa et, à ce moment, la soupape de commande de la buse est activée, ce qui fait passer le mélange sous pression dans la chambre de combustion. Au dernier moment, la soupape d'admission s'ouvre et une nouvelle portion de carburant pénètre dans les canaux de la buse. Dans le même temps, la pression du carburant à l'intérieur de l'élément diminue.
- Injection principale. A ce stade, le piston redescend, la vanne de régulation se ferme, mais une pression de 30 MPa est déjà créée dans la buse. Cette fois, le carburant est alimenté sous haute pression, ce qui assure sa compression et sa combustion efficaces dans la chambre de travail. Chaque processus de compression ultérieur s'accompagne d'une augmentation de la pression à l'intérieur de la buse. La valeur maximale est de 220 MPa. La fin de cette étape se déroule exactement de la même manière que pour l'injection préliminaire de carburant.
- Injection supplémentaire. Il consiste à nettoyer tous les éléments de la buse des traces de suie et de suie. Une injection supplémentaire est effectuée immédiatement après la principale. Toutes les actions d'injection sont effectuées de la même manière que dans l'étape principale. D'une autre manière, ce phénomène est également appelé double injection de carburant.
Vidéo - Comment déterminer quel injecteur de pompe ne fonctionne pas ou cogne
Comment réparer la pompe - injecteurs de vos propres mains
Bien entendu, le remplacement d'un injecteur défaillant sera beaucoup plus correct. Cependant, étant donné les prix actuels des pièces automobiles, la pensée supplie involontairement pourquoi ne pas réparer l'ancienne, car elle est moins chère. En réalité, un kit de réparation de buse coûte beaucoup moins cher qu'un nouvel article, et sera donc beaucoup plus rentable.
La défaillance de l'injecteur est généralement due à un colmatage ou à une détérioration des propriétés d'étanchéité des joints en caoutchouc internes. Le moteur, en même temps, commence à fonctionner de manière instable et ne développe pas sa puissance nominale, et la consommation de carburant augmente considérablement.
Lors du choix d'un kit de réparation, il est important de respecter la marque et le modèle. Afin de ne pas se tromper nous vous conseillons de retirer l'ancien et de l'emmener avec vous dans un magasin de pièces auto. Des consultants sélectionneront pour vous l'ensemble dont vous avez besoin lors de la réparation. Si vous installez des joints conçus pour une buse d'un modèle différent, il est certain que la buse ne fonctionnera pas du tout correctement. Bien que, dans la plupart des cas, ils aient des tailles de joints complètement différentes, ce qui rendra la réparation elle-même problématique, plutôt que le fonctionnement ultérieur d'un tel élément.
Pour réparer l'ancienne buse, il faut la démonter. Pour ce faire, tout d'abord, relâchez la pression dans le système de carburant. Cela est nécessaire pour ne pas se salir avec du carburant et ne pas recevoir un jet puissant en plein visage.
Après cela, la fixation métallique du tube à la buse est dévissée et il s'avère. Démontez l'élément et notez soigneusement l'emplacement et l'ordre de montage des pièces. Cela est nécessaire pour l'assemblage ultérieur, de sorte qu'il n'y ait pas de phénomène tel que l'apparition de pièces "supplémentaires". Nettoyez maintenant les pièces métalliques si elles sont obstruées, remplacez les joints en caoutchouc et les autres pièces qui sont en trousse de réparation buses. Après cela, assemblez la pièce dans l'ordre inverse du démontage.
Enveloppez la buse et connectez-la au système de carburant. La pression ayant été réduite, il est nécessaire de dévisser le bouton d'amorçage manuel et de remettre le système sous pression. La balançoire doit être jusqu'au moment où la poignée ne se serre pas. Après cela, enveloppez-le à nouveau et vous pouvez démarrer le moteur.
Vidéo - Réparation des injecteurs BOSCH
Ceci termine la réparation de l'injecteur-pompe. Il convient de rappeler à nouveau que cette procédure pas du tout compliqué, et surtout - cela vous coûtera le moins cher. Après tout, prolonger la durée de vie d'une ancienne buse est beaucoup moins cher que d'en installer une nouvelle.
L'utilisation d'un tel système permet d'augmenter la puissance du moteur, de réduire les coûts de carburant et la toxicité, le niveau sonore.
Dans le système d'injection de ce type un seul dispositif central, la pompe-injecteur, est responsable de l'alimentation en carburant et de sa distribution. De plus, chaque cylindre est équipé de sa propre buse.
Le système est entraîné par un arbre à cames, équipé de cames spéciales, qui agissent sur l'injecteur-pompe à travers le culbuteur, assurant son fonctionnement.
Comment fonctionne le système pompe-injecteur
Le système pompe-injecteur comprend des éléments tels que: plongeur, piston d'arrêt, vannes de contrôle et de contrôle, aiguille de pulvérisation.
Le piston est conçu pour créer une pression de travail à l'intérieur de la buse. Dans ce cas, le mouvement du plongeur à caractère progressif est assuré par les cames de l'arbre à cames, et le mouvement de retour est assuré par un ressort.
La fonction principale de la soupape de commande est l'injection de carburant, ou plutôt le contrôle de l'injection. Dans de tels systèmes, deux types de vannes peuvent être utilisées - électromagnétiques et piézoélectriques.
Une vanne basée sur un élément piézoélectrique est plus avancée en raison de sa vitesse élevée. L'élément de conception principal de la vanne de régulation est son aiguille.
Le ressort de l'atomiseur est nécessaire pour assurer un ajustement sûr de l'aiguille de l'atomiseur dans le siège. La force du ressort est complétée par la force de la pression de carburant, et tout cela est fait à l'aide d'un piston d'arrêt installé sur un côté du ressort et clapet anti-retour situé à l'opposé de la source.
L'aiguille de l'atomiseur fournit une injection directe Gas-oil dans la chambre de combustion du moteur.
Les injecteurs unitaires sont contrôlés par l'unité de commande du moteur qui, sur la base des données reçues des capteurs, contrôle le fonctionnement de la soupape de l'injecteur unitaire.
Comment fonctionne le système pompe-injecteur
La réception et la distribution efficaces des assemblages combustibles dans le système pompe-injecteur se produisent en trois étapes - injection de carburant préliminaire, principale et supplémentaire.
Pré-injection
L'étage de pré-injection est conçu pour assurer une combustion douce des assemblages combustibles à l'étage d'injection principal. L'étage d'injection principal, à son tour, assure une alimentation ininterrompue du mélange de carburant dans tous les modes de fonctionnement du moteur à combustion interne.
Ainsi, au stade préliminaire de l'alimentation en carburant, la pompe-injecteur fonctionne selon le schéma suivant. La came d'arbre à cames transmet la force mécanique au culbuteur, qui abaisse le piston vers le bas.
Le mélange de carburant commence à s'écouler à travers les canaux situés dans le boîtier de l'injecteur. Ensuite, la vanne se ferme avec un arrêt temporaire de l'alimentation en carburant. Cela crée une haute pression TS, atteignant 13 MPa.
A ce niveau de pression, l'aiguille, surmontant la force exercée sur elle par le ressort, effectue une injection préliminaire du mélange combustible.
L'achèvement de la phase de pré-alimentation en carburant correspond à l'ouverture de la soupape d'admission. Le carburant entre dans la ligne, en même temps il est réduit pression de service. A ce stade, une ou deux injections du véhicule peuvent être réalisées, selon le mode de fonctionnement du moteur diesel.
Injection principale
Le début de l'étape d'injection principale est suivi de l'abaissement ultérieur du piston. Après fermeture de la vanne, la pression TS continue d'augmenter et atteint 30 MPa. A cette pression, l'aiguille est soulevée et l'alimentation principale en carburant se produit.
La haute pression fournit une compression importante du carburant, à la suite de quoi une plus grande partie pénètre dans la chambre de combustion. Le plus grand volume de mélange combustible est fourni à la pression maximale possible de 220 MPa, ce qui permet d'atteindre la puissance maximale du moteur.
L'achèvement de l'étape d'injection principale se produit de manière similaire à l'étape précédente après l'ouverture de la soupape d'admission. Cela s'accompagne d'une diminution de la pression du carburant et d'un abaissement de l'aiguille de pulvérisation.
Injection supplémentaire
La dernière étape est une injection supplémentaire, qui sert à nettoyer filtre à particules de la suie, de la suie et de la saleté. L'alimentation en carburant supplémentaire est effectuée lorsque le piston est abaissé selon un schéma similaire à l'injection principale. A ce stade, en règle générale, deux injections de carburant diesel sont effectuées.
Les injecteurs-pompes se composent de trois sous-systèmes : alimentation en carburant basse pression, alimentation en carburant haute pression, alimentation en air et échappement des gaz d'échappement.
Le sous-système d'alimentation en carburant basse pression est nécessaire pour fournir du carburant à la pompe haute pression et nettoyer le carburant.
Le sous-système d'alimentation en carburant haute pression sert à créer une injection de carburant haute pression dans la chambre de combustion.
Le sous-système d'alimentation en air et de gaz d'échappement comprend des dispositifs de nettoyage de l'air entrant dans les cylindres du moteur et de nettoyage des gaz d'échappement après leur sortie des cylindres.
Les principaux composants du système d'alimentation du moteur diesel avec injecteurs-pompes sont illustrés dans la figure:
Riz. Système d'alimentation du moteur diesel avec injecteurs-pompes :
1 - réservoir de carburant ; 2 - conduite de carburant vers chauffage supplémentaire; 3 – refroidisseur de carburant ; 4 - capteur de température de carburant ; 5 - vanne restrictive dans la canalisation de vidange; 6 - canalisation de vidange; 7 - distributeur de carburant ; 8 - pipeline à haute pression ; 9 - pompe-injecteur; 10 - pompe d'amorçage de carburant; Onze - détendeur dans la conduite d'alimentation en carburant ; 12 - clapet anti-retour; 13 - filtre à carburant; 14 - canalisation basse pression; 15 - pompe d'amorçage de carburant
Située dans le réservoir, une pompe électrique d'amorçage de carburant 15 pompe le carburant vers le filtre. Le clapet anti-retour 12 empêche le carburant de s'écouler du distributeur 7 et de la canalisation basse pression 14 dans le réservoir après l'arrêt du moteur.
La pompe d'alimentation en carburant 10 sert à prélever du carburant du filtre et à l'amener sous haute pression aux injecteurs-pompes. La soupape de réduction de pression 11 maintient la pression du carburant fourni aux injecteurs-pompes à moins de 8,5 kgf/cm2. La soupape de restriction 5 maintient la pression du carburant dans le tuyau de vidange à 1 kgf/cm2, grâce à quoi les pulsations de pression dans le système sont réduites. En raison de la pression d'injection élevée dans les systèmes de carburant diesel des voitures particulières avec injecteurs-pompes et dans certains systèmes à rampe commune, le carburant est chauffé à un point tel que, pour éviter tout dommage, réservoir d'essence et le capteur de niveau de carburant, il doit refroidir avant de retourner au réservoir. Le carburant revenant des injecteurs traverse le refroidisseur 3 en dégageant de la chaleur dans le circuit de refroidissement. Le capteur de température de carburant 4 génère un signal vers l'unité de commande du moteur.
Depuis le filtre, le carburant est fourni à la conduite d'alimentation dans la tête du bloc. Dans la conduite d'alimentation, le carburant s'écoule le long des parois internes du distributeur de carburant 7 en direction du premier cylindre. À travers les trous dans les parois, le carburant est fourni à la cavité annulaire entre le distributeur et les parois de la tête de bloc.
Le carburant est mélangé avec du carburant chauffé, qui est expulsé des injecteurs de la pompe dans la conduite d'alimentation. Grâce à cela, la même température est atteinte, et donc la même quantité de carburant fournie à tous les injecteurs-pompes, ce qui garantit un fonctionnement uniforme du moteur. Sans distributeur, le carburant s'écoulerait de manière inégale dans les injecteurs de la pompe. Le carburant chauffé expulsé des injecteurs unitaires dans la conduite d'alimentation serait propulsé par le carburant entrant du quatrième cylindre vers le premier cylindre. De ce fait, la température du carburant augmenterait du quatrième cylindre au premier, et différentes quantités de carburant seraient fournies aux injecteurs unitaires. Cela entraînerait un fonctionnement inégal du moteur et des températures trop élevées au niveau des cylindres avant.
N° 14 Injecteurs-pompes avec vanne de commande piézoélectrique
Le système d'injection pompe-injecteur est système moderne moteurs diesel à injection de carburant. Contrairement au système d'injection rampe commune dans ce système, les fonctions de création de haute pression et d'injection de carburant sont combinées dans un seul appareil - une pompe-injecteur. En fait la pompe-injecteur est le système d'injection du même nom.
L'utilisation d'injecteurs unitaires vous permet d'augmenter la puissance du moteur, de réduire la consommation de carburant, les émissions substances dangereuses ainsi que le niveau sonore.
Dans le système, chaque cylindre du moteur a sa propre buse. L'entraînement de la pompe-injecteur est effectué à partir de l'arbre à cames, sur lequel se trouvent des cames correspondantes. La force des cames est transmise par le culbuteur directement à l'injecteur-pompe.
La buse de la pompe a le dispositif suivant : piston ; soupape de commande; piston de blocage ; clapet anti-retour ; aiguille d'atomiseur. http://systemsauto.ru/feeding/shema_nasos_forsunka.html
Le piston est utilisé pour créer une pression de carburant. Le mouvement vers l'avant du plongeur est effectué grâce à la rotation des cames de l'arbre à cames, le mouvement de retour est dû au ressort du plongeur.
La soupape de commande est conçue pour contrôler l'injection de carburant. Selon l'actionneur, on distingue les types de vannes suivants :
électromagnétique; piézoélectrique.
La vanne piézoélectrique a remplacé l'électrovanne. La vanne piézoélectrique a une vitesse élevée. L'élément structurel principal de la soupape est le pointeau de soupape.
Le ressort de la buse garantit que l'aiguille de l'atomiseur repose sur le siège.
La force du ressort est soutenue par la pression du carburant si nécessaire. Cette fonction est réalisée au moyen d'un piston d'arrêt et d'un clapet anti-retour. L'aiguille de l'atomiseur est conçue pour fournir injection directe carburant dans la chambre de combustion.
Les injecteurs-pompes sont contrôlés par le système de gestion du moteur. L'unité de commande du moteur commande la soupape d'injection de la pompe en fonction des signaux des capteurs.
Le principe de fonctionnement de la buse de pompe
La conception de l'injecteur-pompe assure une formation optimale et efficace du mélange air-carburant. Pour ce faire, les phases suivantes sont prévues dans le processus d'injection de carburant :
pré-injection ; injection principale ; injection supplémentaire.
La pré-injection est effectuée pour obtenir une combustion douce du mélange lors de l'injection principale. L'injection principale fournit une formation de mélange de haute qualité dans différents modes de fonctionnement du moteur. Une injection supplémentaire est effectuée pour la régénération (nettoyage de la suie accumulée) du filtre à particules.
Le fonctionnement de l'injecteur-pompe s'effectue comme suit. La came de l'arbre à cames déplace le piston vers le bas à travers le culbuteur. Le carburant s'écoule à travers les canaux de la buse. Lorsque la vanne est fermée, le carburant est coupé. La pression de carburant commence à monter. En atteignant une pression de 13 MPa, l'aiguille de l'atomiseur, surmontant la force du ressort, monte et une injection préliminaire de carburant se produit. La pré-injection de carburant est arrêtée à l'ouverture de la vanne. Le carburant est versé dans la conduite d'alimentation. Chutes de pression de carburant. Selon les modes de fonctionnement du moteur, une ou deux injections préliminaires de carburant peuvent être réalisées. L'injection principale se fait à mouvement supplémentaire piston vers le bas. La vanne se referme. La pression de carburant commence à monter. En atteignant une pression de 30 MPa, l'aiguille de l'atomiseur, surmontant la force du ressort et la pression du carburant, monte et l'injection principale de carburant se produit. Plus la pression est élevée, plus le carburant est comprimé et, par conséquent, plus est injecté dans la chambre de combustion du moteur. À une pression maximale de 220 MPa, la plus grande quantité de carburant est injectée, assurant ainsi une puissance maximale du moteur.
L'injection principale de carburant est terminée lorsque la soupape est ouverte. Dans le même temps, la pression du carburant chute et l'aiguille de l'atomiseur se ferme.
Une injection supplémentaire est effectuée avec un mouvement vers le bas supplémentaire du piston. Le principe de fonctionnement de l'injecteur-pompe avec une injection supplémentaire est similaire à l'injection principale. Habituellement, deux injections supplémentaires de carburant sont effectuées.
№15 Bougies de préchauffage
Pour faciliter le démarrage des moteurs diesel par temps froid (de +5 à -30°C), l'air des cylindres est réchauffé à l'aide de bougies de préchauffage. À la base, les bougies de préchauffage font partie des dispositifs de préchauffage.
La bougie de préchauffage a des emplacements d'installation différents selon la conception du moteur diesel : dans la chambre vortex (moteurs avec une chambre de combustion séparée) ; dans la préchambre (moteurs à chambre de combustion séparée); dans la chambre de combustion (moteurs à chambre de combustion intégrée).
Structurellement, une bougie de préchauffage est un dispositif de chauffage électrique constitué d'une bobine de filament placée dans une gaine de protection. Il existe deux types de bougies de préchauffage : à spirale métallique ; céramique.
Les bougies de préchauffage en céramique ont haute température chauffage (jusqu'à 1350°C), temps de préchauffage plus court qu'avec une spirale métallique (2 sec) et, par conséquent, Meilleure performance démarrage à froid. Les principaux fabricants de bougies de préchauffage sont les entreprises Bosch, NGK, Lucas. Les bougies de préchauffage sont contrôlées par relais ou unité de commande électronique séparée. Ces dispositifs régulent la quantité de tension appliquée aux bougies et fournissent ainsi le moment et la température de lueur nécessaires, ainsi que la durée de chauffage.
Les bougies de préchauffage sont allumées sous certaines conditions de température lors du démarrage du moteur ( première position de la clé dans le contacteur d'allumage), ce qui indique lampe témoin sur le tableau de bord. Une fois que la lampe s'est éteinte et que le préchauffage est terminé, le moteur est démarré ( la deuxième position de la clé dans le contacteur d'allumage). Sur les moteurs diesel modernes, les bougies de préchauffage, en plus du préchauffage préliminaire (pré-démarrage), fournissent lueur supplémentaire après le démarrage du moteur. De la chaleur supplémentaire est produite pour réduire le bruit lors de la combustion du mélange sur un moteur froid, ainsi que pour réduire les émissions nocives dans l'atmosphère. La phase de chauffage supplémentaire a une durée d'environ 3 minutes et se termine lorsque le liquide de refroidissement atteint une température de 20-30°C.
N ° 16) Nomination de pressurisation, systèmes existants suralimentation, suralimentation avec entraînement mécanique !
Suralimentation - une augmentation de la quantité d'une nouvelle charge d'un mélange combustible fournie à un moteur à combustion interne en raison d'une augmentation de la pression d'admission. La suralimentation est généralement utilisée pour augmenter la puissance (de 20 à 45 %) sans augmenter la masse et les dimensions du moteur, ainsi que pour compenser les baisses de puissance dans des conditions de haute altitude. La suralimentation avec « régulation de la qualité » peut être utilisée pour réduire la toxicité et l'opacité des gaz d'échappement. La pressurisation globale est réalisée à l'aide d'un compresseur, d'un turbocompresseur ou d'un combiné. La suralimentation la plus largement utilisée est un turbocompresseur, qui utilise l'énergie des gaz d'échappement pour l'entraîner.
La suralimentation unitaire est utilisée dans presque tous les types de moteurs diesel de transport (bateau, locomotive diesel, tracteur). Suralimentation activée moteurs à carburateur limité à la détonation. Les principaux inconvénients de la pressurisation globale comprennent :
augmentation des contraintes mécaniques et thermiques du moteur dues à une augmentation de la pression et de la température des gaz;
baisse de la rentabilité ;
complication du dessin.
La suralimentation sans unité comprend :
dynamique (précédemment appelé inertiel, résonant, acoustique), dans lequel l'effet est obtenu grâce à des phénomènes oscillatoires dans les pipelines;
à grande vitesse, utilisé sur piston Moteurs d'avionà des altitudes supérieures à celle calculée et à des vitesses supérieures à 500 km/h ;
réfrigération, obtenue par évaporation de carburant ou d'un autre liquide combustible à bas point d'ébullition et à haute chaleur de vaporisation dans l'air entrant.
La suralimentation dynamique est de plus en plus répandue dans les moteurs à combustion interne de transport, ce qui, avec des changements mineurs dans la conception des canalisations, entraîne une augmentation du facteur de remplissage jusqu'à une large gamme de changements de régime moteur. Une augmentation du boost permet de booster un moteur diesel au niveau des indicateurs énergétiques en cas d'augmentation simultanée de l'alimentation cyclique en carburant ou d'améliorer les indicateurs économiques tout en maintenant la puissance (avec la même alimentation cyclique en carburant). Le boost dynamique augmente la durabilité des pièces du groupe cylindre-piston en raison de conditions thermiques plus faibles lors du fonctionnement sur des mélanges pauvres.
Il existe plusieurs systèmes de boost. Tout d'abord, ils doivent inclure le type le plus courant - turbocompresseur - suralimentation par l'utilisation de l'énergie des gaz d'échappement (Fig. a). Ce type de boost sera discuté plus en détail ci-dessous.
La deuxième option de suralimentation est la suralimentation à partir d'un compresseur d'entraînement - le soi-disant SUPERCHARGER. Sur le moteurs modernes ce schéma est rarement utilisé en raison de la complexité de la conception du compresseur et de sa fiabilité insuffisante. Son avantage par rapport à la turbocompression est une pression de suralimentation plus élevée dans les modes bas, ainsi que l'absence du soi-disant "turbo lag", c'est-à-dire "défaillance" caractéristique de la puissance avec une forte ouverture de l'accélérateur. Cela détermine la portée du compresseur d'entraînement - principalement sur les moteurs pas trop rapides (FORD, GM), bien que dans dernières années on a eu tendance à les utiliser sur des moteurs à grande vitesse (MERCEDES).
Les moteurs diesel MAZDA sont équipés d'un échangeur de pression à ondes COMPREX, qui fournit une suralimentation due à l'interaction des ondes de pression et de raréfaction se propageant dans les canaux d'un rotor en rotation. Ce type de suralimentation permet d'obtenir une suralimentation plus élevée que les autres systèmes de suralimentation, mais ne s'est pas encore généralisé en raison de la complexité de la conception.
N ° 17) turbocompresseur, son UVO et le principe de fonctionnement
La base de la suralimentation
La base du système de suralimentation du moteur, et en même temps son élément le plus complexe, est le turbocompresseur. Le principe de fonctionnement d'un turbocompresseur est que l'énergie restant dans les gaz d'échappement ne va pas dans l'atmosphère, mais va augmenter la pression et la densité de l'air entrant dans le moteur.
Les gaz évacués par le moteur à travers le collecteur d'échappement pénètrent dans le carter de turbine (volute chaude). La pression des gaz et l'énergie thermique des gaz font tourner la roue de turbine (roue chaude), qui à son tour fait tourner la roue du compresseur (roue froide). Les gaz d'échappement sont ensuite rejetés dans l'atmosphère.
Lorsque la roue du compresseur tourne, elle aspire l'air à travers le filtre à air. Les aubes de la roue du compresseur accélèrent et poussent l'air dans le carter du compresseur (volute froide), où l'air est comprimé et collecteur d'admission moteur. L'air sortant du compresseur a non seulement hypertension artérielle, mais aussi la température, qui réduit la densité de charge, ce qui nuit au remplissage et, par conséquent, à la puissance du moteur. Par conséquent, sur de nombreux moteurs turbocompressés, afin d'augmenter la densité de l'air et, par conséquent, d'améliorer le remplissage des cylindres, un refroidissement intermédiaire de l'air de suralimentation (intercooler) est utilisé. Pour ce faire, après le compresseur, l'air est dirigé vers un radiateur spécial "air-air" installé à côté du radiateur du système de refroidissement.
N° 18) circuit de commande électronique de suralimentation
ligne de vide
l'unité de commande du moteur
capteurs de pression de suralimentation et de température d'air d'admission
unité de commande de volet d'air
refroidisseur intermédiaire
Vanne EGR
soupape de commande de pression de suralimentation
turbocompresseur
collecteur d'admission
entraînement par le vide des aubes directrices
un collecteur d'échappement
A-air
B - gaz d'échappement
N° 19. TURBOCOMPRESSEUR À GÉOMÉTRIE VARIABLE DE TURBINE (VGT).
VGT (Variable Geometry Turbine) est un type spécifique de turbocompresseur qui fonctionne en utilisant l'énergie du flux de gaz d'échappement. Le graphique ci-dessous montre Caractéristiques comparatives capacités de vitesse des véhicules équipés d'un turbocompresseur conventionnel et d'un turbocompresseur VGT. Vitesse maximale : VGT vous permet d'augmenter vitesse de pointe de 4,1 %.
Temps d'accélération : Par rapport à un turbocompresseur VGT conventionnel, le temps d'accélération de 0 km/h à 100 km/h peut être réduit de 15,1 %.
Temps d'accélération d'accélération : cette caractéristique montre la capacité du véhicule lors d'une forte accélération (de 60 km/h à 100 km/h) pendant la conduite. Plus il est petit, meilleures sont les performances.
PRINCIPE DE FONCTIONNEMENT
Fonctionnant à bas régime moteur
Lorsque le moteur tourne à bas régime, la quantité de gaz d'échappement est relativement faible, l'énergie de leur écoulement est faible et, dans un turbocompresseur conventionnel, il n'y a pas d'effet de turbocompresseur significatif, et dans un turbocompresseur VGT, il est possible de passer l'échappement gaz à travers une section transversale plus étroite du canal d'écoulement, grâce à quoi la vitesse et l'énergie de leur écoulement augmentent considérablement. Par conséquent, le système VGT améliore les performances du moteur à bas régime.
Principe de fonctionnement à bas régime
Cette conception utilise le principe du tube Venturi, dont l'essence est que lorsque l'air traverse une section rétrécie (point "A"), le débit augmente et la pression diminue. Avec une diminution du diamètre de la section de passage, le débit augmentera proportionnellement (voir équation).
Fonctionnement à haut régime
À haut régime, l'énergie du flux de gaz d'échappement est suffisamment élevée et est capable de créer la force nécessaire pour faire tourner la turbine. Dans ce cas, la section du canal de passage augmente et tout le flux de gaz d'échappement se précipite vers la turbine, tandis que la résistance de pompage du conduit d'échappement diminue. Les caractéristiques de sortie du moteur dépendront du volume d'air d'admission.
Contrôle du système VGT
Le signal de commande du système VGT est formé sur la base de l'analyse des signaux des capteurs de vitesse vilebrequin un(CV), position de la pédale d'accélérateur, pression atmosphérique, pression de suralimentation, température du liquide de refroidissement (liquide de refroidissement), température de l'air d'admission et signal d'embrayage.
Dans ce cas, l'ECU détermine les conditions de conduite de la voiture et la pression de suralimentation requise en fonction du régime moteur et de la quantité de carburant injectée. Ensuite, l'ECU sort vers électrovanne le signal correspondant avec une fréquence de 300 Hz avec les paramètres donnés. Un tel système vous permet de maintenir un fonctionnement efficace du moteur à n'importe quelle vitesse.
Il convient de noter que le capteur de pression de suralimentation est également conçu pour mesurer la pression d'air réelle dans le collecteur d'admission et fournir un retour au système de contrôle de la pression de suralimentation (via l'ECU). Cette rétroaction contribue à la précision du contrôle.
Conditions excluant la possibilité de fonctionnement du système VGT
1. Régime moteur inférieur à 700 tr/min
2. La température du liquide de refroidissement est descendue à 0°
3. Dommages à toute partie du système EGR
4. Dommages à la tige d'entraînement du système VTG
5. Capteur de pression de suralimentation défectueux
6. Endommagement du capteur de débit d'air (MAF)
7. Dommages à l'accélérateur
8. Capteur de position de pédale d'accélérateur défectueux
Si l'une de ces conditions existe, l'ECU cessera de contrôler le système VTG.
N ° 20. Mesures supplémentaires pour réduire la toxicité des gaz d'échappement
Afin de réduire le niveau d'émission dans l'atmosphère de composants toxiques qui entrent dans la composition des gaz d'échappement du moteur à la suite de l'évaporation et de la combustion incomplète du carburant, ainsi que de maintenir l'efficacité de la puissance du moteur et de réduire la consommation de carburant , voitures moderneséquipé d'une gamme de systèmes spéciaux, qui peuvent être regroupés sous le nom général de système de gestion moteur et réduire la toxicité des gaz d'échappement. Considérez les systèmes les plus courants :
1. Contrôle du dosage du carburant.
Le contrôle de la composition du mélange est effectué par des systèmes de contrôle du carburant.
Avec un taux d'excès d'air de λ=0,9, le moteur fonctionne à puissance et couple maximum.
Une efficacité optimale et des émissions minimales de CO et de CH sont obtenues en travaillant avec des mélanges avec un facteur λ=1,1. Cependant, la teneur en oxydes d'azote dans les gaz d'échappement s'avère en même temps maximale.
Pour faire fonctionner le moteur en mouvement oisif la composition du mélange doit être caractérisée par le coefficient λ=0,9 - 1,05.
Le mode ralenti forcé (frein moteur) vous permet de couper complètement l'alimentation en carburant des cylindres. Les émissions de substances toxiques seront absentes.
2. Recirculation des gaz d'échappement.
Le retour d'une partie des gaz d'échappement dans la chambre de combustion (recirculation) permet de réduire la température de combustion du mélange afin de réduire la formation d'oxydes d'azote et la consommation de carburant. Cependant, cela réduit également la puissance du moteur.
Recirculation des gaz d'échappement ( Système EGR) est mis en œuvre de deux manières : 1) par recirculation interne, assurée par le contrôle des phases de distribution de gaz, et d'abord par chevauchement de vannes ; 2) la recirculation externe, dans laquelle les gaz d'échappement sont prélevés à la sortie du collecteur d'échappement et renvoyés à la chambre de combustion par un système de soupapes.
3. Ventilation du carter moteur.
La toxicité des gaz de carter étant plusieurs fois supérieure à celle des gaz d'échappement, leur rejet dans l'atmosphère est interdit. Lorsque le moteur tourne, les gaz du carter passent à travers le système de ventilation du carter dans le conduit d'admission du moteur, où ils se mélangent aux gaz de travail et pénètrent dans le cylindre à la course d'admission pour une postcombustion ultérieure.
4. Post-combustion thermique des gaz d'échappement.
La postcombustion des composants des gaz d'échappement qui n'ont pas brûlé dans le cylindre du moteur se produit dans le système d'échappement, où de l'air supplémentaire est fourni par un compresseur spécial, ce qui est nécessaire pour que la réaction de postcombustion ait lieu.
Avec le développement des systèmes de traitement catalytique des gaz d'échappement, la postcombustion thermique n'est plus aussi largement utilisée qu'auparavant.
5. Postcombustion catalytique.
La postcombustion des composants des gaz d'échappement se produit dans un dispositif spécial - un convertisseur catalytique. Le convertisseur est monté dans le système d'échappement et est situé sous le bas de la voiture. Dans le corps du convertisseur se trouve un bloc de céramique recouvert d'un matériau catalytique (métaux - Pt, Rh, Rd).
Les convertisseurs de type oxydant oxydent le CO et le CH en utilisant de l'oxygène résiduel dans des mélanges pauvres ou en fournissant de l'air supplémentaire au système.
Les convertisseurs de type réducteur réduisent les NOx en azote inoffensif.
Les neutralisants à deux composants combinent des types de neutralisants oxydants et réducteurs.
Les convertisseurs à trois voies (convertisseurs catalytiques sélectifs) avec une sonde λ sont de loin le système d'épuration des gaz d'échappement le plus courant et le plus efficace. Le capteur d'oxygène (λ - sonde) de ce système est utilisé pour calculer le rapport air/carburant dans le mélange combustible.
6. Systèmes avec retour d'information(λ - régulation).
Ce système permet de neutraliser jusqu'à 96 % des substances nocives dans les gaz d'échappement. Le système utilise deux capteurs d'oxygène. Un capteur est installé avant le convertisseur catalytique, l'autre après celui-ci. Les capteurs, mesurant la quantité d'oxygène libre dans les gaz d'échappement, via le système de gestion du carburant, affectent la composition mélange air-carburant entrer dans les cylindres du moteur. Pour assurer un nettoyage correct des gaz d'échappement avec un convertisseur, le moteur doit fonctionner dans une plage étroite de valeurs \u200b\u200bλ \u003d 1 ± 0,005, appelée la "fenêtre" convertisseur catalytique.
N° 21. Schéma d'un système de changement continu du calage des soupapes avec un embrayage à commande hydraulique. Calage des soupapes réglable.
Le système de calage variable des soupapes (nom international commun Variable Valve Timing, VVT) est conçu pour contrôler les paramètres du mécanisme de distribution de gaz, en fonction des modes de fonctionnement du moteur. L'utilisation de ce système permet d'augmenter la puissance et le couple du moteur, le rendement énergétique et la réduction des émissions nocives.
Les paramètres réglables du mécanisme de distribution de gaz comprennent :
Le moment d'ouverture (fermeture) des vannes ;
La durée d'ouverture des vannes ;
Hauteur de levée des soupapes.
Ensemble, ces paramètres constituent le calage des soupapes - la durée des courses d'admission et d'échappement, exprimée par l'angle de rotation du vilebrequin par rapport aux points "morts". Le calage des soupapes est déterminé par la forme de la came de l'arbre à cames agissant sur la soupape.
Différents modes de fonctionnement du moteur nécessitent un calage des soupapes différent. Ainsi, à bas régime, le calage des soupapes doit avoir une durée minimale (phases « étroites »). À haut régime, au contraire, le calage des soupapes doit être le plus large possible et en même temps assurer le chevauchement des courses d'admission et d'échappement (recirculation naturelle des gaz d'échappement).
La came d'arbre à cames a une certaine forme et ne peut pas fournir simultanément un calage des soupapes étroit et large. En pratique, la forme de la came est un compromis entre un couple élevé à bas régime et une puissance élevée à haut régime. Cette contradiction est exactement ce que résout le système de changement de calage des soupapes.
En fonction des paramètres réglables du mécanisme de distribution de gaz, on distingue les méthodes suivantes de calage variable des soupapes:
rotation de l'arbre à cames ;
l'utilisation de cames avec différents profils ;
modification de la levée des soupapes.
Les plus courants sont les systèmes de calage variable des soupapes utilisant la rotation de l'arbre à cames :
VANOS (Double VANOS) de BMW ;
VVT-i (Dual VVT-i), calage variable des soupapes avec intelligence de Toyota ;
VVT, calage variable des soupapes de Volkswagen ;
VTC, contrôle de distribution variable de Honda ;
CVVT, calage variable continu des soupapes de Hyundai, Kia, Volvo, General Motors ;
VCP, Phases de cames variables par Renault.
Le principe de fonctionnement de ces systèmes est basé sur la rotation de l'arbre à cames dans le sens de rotation, ce qui permet d'obtenir une ouverture précoce des soupapes par rapport à la position initiale.
Le système de calage variable des soupapes de ce type présente les caractéristiques suivantes dispositif général:
Embrayage hydraulique ;
Système de contrôle.
Un embrayage à commande hydraulique (communément appelé déphaseur) fait tourner directement l'arbre à cames. L'embrayage est constitué d'un rotor relié à arbre à cames, et le boîtier, qui est la poulie d'entraînement de l'arbre à cames. Entre le rotor et le boîtier, il y a des cavités auxquelles l'huile moteur est fournie par les canaux. Le remplissage d'une cavité ou d'une autre avec de l'huile assure la rotation du rotor par rapport au carter et, par conséquent, la rotation de l'arbre à cames selon un certain angle.
Pour la plupart, un embrayage à commande hydraulique est installé sur l'arbre à cames d'admission. Pour étendre les paramètres de contrôle dans certaines conceptions, les accouplements sont installés sur les arbres à cames d'admission et d'échappement.
Le système de commande assure le contrôle automatique du fonctionnement de l'embrayage à commande hydraulique. Structurellement, il comprend des capteurs d'entrée, l'unité électronique commandes et actionneurs. Le système de contrôle utilise des capteurs à effet Hall qui évaluent les positions arbres à cames, ainsi que d'autres capteurs du système de gestion du moteur : vitesse du vilebrequin, température du liquide de refroidissement, débitmètre d'air. L'unité de commande du moteur reçoit les signaux des capteurs et génère des actions de commande sur l'actionneur - un distributeur électrohydraulique. Le distributeur est une électrovanne et assure l'alimentation en huile de l'embrayage à commande hydraulique et son retrait, en fonction des modes de fonctionnement du moteur.
Le système de calage variable des soupapes prévoit généralement un fonctionnement dans les modes suivants:
Ralenti (vitesse minimale du vilebrequin);
Couple maximal.
N° 22. Système de levée de soupape
Le représentant de l'entraînement mécanique est le système Valvetronic utilisé sur Voitures BMW, qui contrôle la levée des soupapes d'admission et dose le mélange de travail entrant dans les cylindres, ce qui permet d'augmenter le rendement du moteur sans perte de puissance tout en respectant les normes Euro-4 et en maintenant le système d'injection dans le collecteur d'admission. En changeant la course de la vanne à haute fréquence la rotation du vilebrequin permet d'obtenir la meilleure ventilation du cylindre et le remplissage avec le mélange air-carburant. Au régime minimum du vilebrequin, la course des soupapes est minimale. Dans le même temps, l'effet du chevauchement des soupapes est réduit, de sorte que la consommation de carburant est minimale. Avec une augmentation de la fréquence de rotation du vilebrequin, la quantité d'ouverture des soupapes augmente. Dans le même temps, la résistance aux flux de gaz à l'intérieur du cylindre diminue, la vitesse de soufflage et de remplissage du cylindre avec un mélange air-carburant augmente. De plus, l'effet de l'effet d'inertie est augmenté. Le mélange air-carburant à l'intérieur du cylindre est fermé par des soupapes à une pression beaucoup plus élevée, sa densité est plus élevée qu'à la vitesse minimale du vilebrequin. Grâce à la course de vanne variable, les pertes par frottement sont réduites par rapport à un actionneur de vanne conventionnel, en raison de la faible résistance à une petite course de vanne.
Schéma du système de contrôle de la levée des soupapes d'admission du moteur BMW Valvetronic :
1 - ressort de levier ; 2 - moteur électrique; 3 - roue dentée à vis sans fin; 4 - arbre de commande excentrique; 5 - arbre à cames; 6 - levier avec support à rouleaux; 7 - bascule; 8 - soupape.
Entre l'arbre à cames 5 et chaque paire de soupapes d'admission 8 se trouve un levier supplémentaire 6, qui est monté sur l'axe. Le moteur électrique 2 à travers l'engrenage à vis sans fin fait tourner l'arbre de commande excentrique 4 à un angle déterminé par système électronique la gestion. L'ouverture des soupapes s'effectue directement par des leviers 6 à roulements à rouleaux lorsqu'ils agissent sur les culbuteurs, qui s'appuient sur la soupape d'un côté et sur le poussoir hydraulique de l'autre. Les leviers 6 sont pressés contre la came d'arbre à cames au moyen de ressorts torsadés 1. Pour réduire les pertes par frottement, des roulements à aiguilles sont installés sur les axes du levier avec un roulement à rouleaux et le culbuteur. Lors de la rotation de l'arbre excentrique, l'excentrique tournant sur le levier 6 le fait tourner d'un certain angle. En déplaçant l'arbre excentrique, le moteur électrique augmente ou diminue l'épaulement du levier intermédiaire, allongeant ou raccourcissant ainsi la course des soupapes d'admission en fonction de la charge du moteur. Considérant que l'excentrique déplaçant l'axe du poussoir a entraînement électrique, cela vous permet de définir l'angle de rotation comme non linéaire et de le programmer individuellement pour chaque moteur.
La modification de la hauteur de la levée de soupape peut être effectuée en modifiant la hauteur de la came d'arbre à cames agissant par l'intermédiaire du culbuteur sur la soupape. Cette solution appelée "VTEC-System" est utilisée par Honda. L'abréviation VTEC est entièrement déchiffrée comme suit - Variable Valve Timing and Lift Electronic Control. Le mécanisme de commutation est monté sur l'axe des culbuteurs. Ce système vous permet de modifier la course des soupapes en fonction de la vitesse du vilebrequin (haute ou basse), ainsi que d'éteindre les cylindres du travail. Arbre à cames, en plus de deux cames de petite hauteur 3, comporte une grande came 6 au milieu d'elles pour entraîner les soupapes de chaque cylindre avec une course et une durée d'ouverture accrues. Une grande came agit sur un culbuteur supplémentaire 7, qui est soutenu par un dispositif à ressort spécial 9. À l'intérieur de l'axe de l'arbre à cames se trouve un canal d'alimentation en huile 2 vers le piston de verrouillage, qui se compose de deux parties. L'alimentation en huile des pièces du système s'effectue par un canal réalisé à l'intérieur de l'arbre à cames. Pour créer la pression nécessaire, un la pompe à huile alimenté par la conduite d'huile principale. Le poussoir de verrouillage est constitué de deux pistons mobiles sous pression d'huile et relient le culbuteur supplémentaire 7 aux culbuteurs principaux 4. En même temps, la came 6, qui a une hauteur supérieure aux cames 3, agit sur les culbuteurs supplémentaires. culbuteur 7 relié aux culbuteurs principaux 4, ouvrant fortement la soupape et augmentant la durée d'alimentation du mélange air-carburant. Lorsque l'alimentation en huile s'arrête, le piston de verrouillage revient à son état d'origine sous l'influence du ressort et le culbuteur supplémentaire est déconnecté des principaux.
N° 23. Entraînement de vanne électromécanique
L'actionneur de soupape électromagnétique EVA (Electromagnetic Valve Actuator) permet d'améliorer le remplissage des cylindres sans augmenter le nombre de soupapes, sans allonger la phase d'admission et sans augmenter la levée des soupapes. De tels systèmes sont actuellement développés intensivement en Europe et aux États-Unis.
La commande de vanne électromagnétique est une vanne à ressort, qui est placée entre deux électroaimants qui la maintiennent dans ses positions extrêmes : fermée ou complètement ouverte. Un capteur spécial fournit à l'unité de commande des informations sur la position actuelle de la vanne. Cela est nécessaire pour réduire sa vitesse au minimum au moment de l'atterrissage en selle.
Le principe de fonctionnement du système est illustré sur la figure. Comme le montre le schéma de fonctionnement de ce système, l'arbre à cames avec son entraînement est complètement absent du système de commande des soupapes, qui est remplacé par des électroaimants pour chaque soupape.
Riz. Actionneur de vanne électromécanique :
1 - électroaimant d'ouverture de soupape ; 2 - ancre; 3 – électroaimant de fermeture de vanne ; 4 - ressort de soupape
L'armature du solénoïde forme une combinaison avec deux ressorts pour ouvrir et fermer la vanne. Lorsqu'aucun courant n'est appliqué aux électroaimants, les ressorts de soupape et d'électroaimant maintiennent la soupape en position médiane, correspondant à la moitié de la course de la soupape, alors qu'elle est à moitié ouverte, ce qui facilite le défilement du vilebrequin du moteur dans la phase initiale de démarrage . Lorsque la vitesse requise est atteinte, un signal est reçu de l'unité de commande et un signal est fourni à l'électroaimant d'ouverture supérieure. électricité, la vanne se ferme. En même temps, du carburant est injecté.
№24. Entraînement hydraulique vannes
Application entraînement électromagnétique les soupapes nécessitent beaucoup d'électricité pour les ouvrir, c'est pourquoi les fabricants de moteurs allemands proposent d'ouvrir les soupapes à l'aide de l'hydraulique et de contrôler l'hydraulique à l'aide de l'électricité. Contrairement à d'autres types d'ouverture de soupape, l'utilisation d'un entraînement de soupape électro-hydraulique vous permet d'abandonner non seulement l'arbre à cames et le papillon des gaz, mais également les ressorts de soupape. Avec l'utilisation de ce type de soupapes, ainsi qu'une simple ouverture-fermeture des soupapes et de la course des soupapes, il est possible de modifier le calage des soupapes et leur fonctionnement indépendamment pour chaque cylindre, réduisant ainsi la consommation de carburant et l'émission de substances toxiques dans les gaz d'échappement et augmenter la puissance du moteur.
Le schéma de l'entraînement de soupape électro-hydraulique:
1 - pompe haute pression ; 2 – ligne haute pression (50…200 kgf/cm2) ; 3 - vanne de régulation haute pression ; 4 – conduite de pression de commande (5…20 kgf/cm2) ; 5 - bloc de levée électro-hydraulique des soupapes; 6 - régulateur de levée de soupapes; 7 - électrovanne sur la ligne basse pression; 8 – ligne basse pression (moins de 5 kgf/cm2) ; 9 - vanne du mécanisme de distribution de gaz; 10 - vanne électromagnétique sur la ligne haute pression ; 11 - cylindre; 12 - piston.
Le principe de fonctionnement du système est le suivant. La pompe haute pression crée une pression d'huile dans le système jusqu'à 200 kgf/cm2. Le réducteur électromagnétique 3 régule la pression dans la conduite haute pression entre 50 ... 200 kgf / cm2 au signal de l'unité de commande, en fonction de la vitesse du vilebrequin, de la charge, de la température, etc. Cette vanne régule la course variable de la vanne lever simultanément pour toutes les vannes immédiatement. Lorsqu'une tension est appliquée à l'électrovanne 10, celle-ci s'ouvre et l'huile de la conduite haute pression pénètre dans le cylindre par le dessus du piston. L'électrovanne de la ligne basse pression 7 est fermée à ce moment car elle n'est pas alimentée. Le piston, agissant sur la soupape du mécanisme de distribution de gaz, le déplace vers le bas, de sorte que la soupape s'ouvre. Selon le mode de fonctionnement du moteur, le régulateur de levée de soupape 6 est activé, modifiant simultanément la vitesse d'assise de toutes les soupapes. Le changement du calage de soupape se produit lorsque le temps d'alimentation en tension de l'électrovanne sur la ligne haute pression 10 change.
Lorsque l'électrovanne 10 est désactivée, l'huile de la conduite haute pression pénètre dans le cylindre par le bas du piston. Le piston, agissant sur la soupape du mécanisme de distribution de gaz, le déplace vers le haut, de sorte que la soupape se ferme. L'huile provenant du dessus du piston est introduite dans la conduite basse pression, puis renvoyée à la pompe.
Des pistons en deux parties sont utilisés pour augmenter la force d'ouverture de la vanne et en même temps réduire la consommation d'énergie lorsque la course d'ouverture de la vanne est importante. Avec une pression moyenne d'environ 100 kgf/cm2 et un temps de réponse relativement court, la course complète de la vanne est de 1 mm, et la vitesse d'assise varie de 0,05 à 0,5 m/s.
L'actionneur de soupape électro-hydraulique est relié au système de circulation d'huile moteur. Les points communs au système de lubrification du moteur sont le carter d'huile moteur, une pompe à huile pour fournir de l'huile au système de lubrification du moteur et à la pompe d'entraînement de soupape haute pression, un filtre à huile et une conduite de vidange d'huile depuis la tête de bloc. A l'huile utilisée, idem pour système commun la lubrification et les entraînements de vannes sont soumis à des exigences de qualité élevées pour un fonctionnement à long terme et des caractéristiques de viscosité. Par conséquent, de l'huile de type 0W40 doit être versée dans le système de lubrification. Pour surveiller la viscosité pendant le fonctionnement du moteur, un capteur spécial est fourni qui envoie un signal sur la perte de viscosité.
Les lève-soupapes électro-hydrauliques peuvent être installés et montés indépendamment les uns des autres. La surface plane du bloc, réalisée avec une grande précision, permet d'assurer l'étanchéité hydraulique nécessaire de la liaison entre le bloc et le carter moteur.
N° 25. Systèmes pour modifier le degré de compression du mélange air-carburant. Différentes manières arrêts de cylindre.
Le taux de compression d'un moteur à combustion interne est étroitement lié à l'efficacité. Dans les moteurs à essence, le taux de compression est limité par la zone de combustion par détonation. Ces limitations sont particulièrement importantes pour le fonctionnement à pleine charge du moteur, alors qu'à charges partielles un taux de compression élevé n'entraîne pas de risque de détonation. Pour augmenter la puissance du moteur et améliorer l'économie, il est souhaitable de réduire le taux de compression, cependant, si le taux de compression est faible pour toutes les plages de fonctionnement du moteur, cela entraînera une diminution de la puissance et une augmentation de la consommation de carburant à charges partielles. Dans ce cas, les valeurs du taux de compression sont généralement choisies bien inférieures aux valeurs auxquelles les performances les plus économiques des moteurs sont obtenues. Aggravant sciemment l'efficacité des moteurs, cela est particulièrement prononcé lors du fonctionnement à charges partielles. Pendant ce temps, une diminution du remplissage des bouteilles avec un mélange combustible, une augmentation de la quantité relative de gaz résiduels, une diminution de la température des pièces, etc. créer des opportunités d'augmentation du taux de compression aux charges partielles afin d'augmenter l'efficacité du moteur et d'augmenter sa puissance. Pour résoudre un tel problème de compromis, des variantes de moteurs à taux de compression variable sont en cours de développement.L'une des variantes les plus courantes d'un moteur à taux de compression variable est représentée sur la figure.
Aux charges partielles, la bielle supplémentaire 4 occupe la position la plus basse et élève la zone de la course du piston. Le taux de compression est à son maximum. Aux charges élevées, l'excentrique sur l'arbre 3 soulève l'axe de la tête supérieure de la bielle supplémentaire 4. Cela augmente le jeu sur-piston et réduit le taux de compression.
Les cylindres du moteur et la tête de bloc sont réalisés en monobloc, c'est-à-dire en un seul bloc, et non séparément comme dans les moteurs conventionnels. Un bloc séparé est également un carter de bloc et un groupe de bielle et de piston. Le monobloc peut se déplacer dans le carter. En même temps, le côté gauche du monobloc repose sur l'axe 1 situé dans le bloc, qui sert de charnière, le côté droit peut être relevé ou abaissé à l'aide d'une biellette 3 commandée par un arbre excentrique 4.
Pour sceller le monobloc et le carter, une tôle ondulée bottes en caoutchouc 2. Le taux de compression change lorsque le monobloc est incliné par rapport au carter au moyen d'un actionneur hydraulique à course de piston constante. La déviation du monobloc par rapport à la verticale entraîne une augmentation du volume de la chambre de combustion, ce qui entraîne une diminution du taux de compression.
Lorsque l'angle d'inclinaison diminue, le taux de compression augmente. L'écart maximal du monobloc par rapport à l'axe vertical est de 4 %.
Au régime minimum du vilebrequin et à la réinitialisation de l'alimentation en carburant, ainsi qu'à faible charge, le monobloc occupe la position la plus basse dans laquelle le volume de la chambre de combustion est minimal (taux de compression - 14). Le système de suralimentation est désactivé et l'air entre directement dans le moteur.
Sous charge, en raison de la rotation de l'arbre excentrique, la bielle dévie le monobloc sur le côté et le volume de la chambre de combustion augmente (taux de compression - 8). Dans ce cas, l'embrayage connecte le compresseur et l'air commence à s'écouler dans le moteur sous une surpression. Le taux de compression optimal est calculé par l'unité de commande du système électronique, en tenant compte de la vitesse du vilebrequin, du degré de charge, du type de carburant et d'autres paramètres.
En raison de la nécessité de réagir rapidement aux changements du taux de compression dans ce moteur J'ai dû abandonner le turbocompresseur au profit d'une suralimentation mécanique avec intercooling d'air avec une pression de suralimentation maximale de 2,8 kgf/cm2.
La consommation de carburant du moteur développé est inférieure de 30 % à celle du moteur conventionnel de même volume et les indicateurs de toxicité des gaz d'échappement sont conformes aux normes en vigueur.
Les principaux moyens d'éteindre les cylindres sont les suivants : éteindre les cylindres en coupant l'alimentation en carburant tout en maintenant un degré variable d'étranglement des cylindres au ralenti (méthode 1); éteindre les cylindres en coupant l'alimentation en carburant avec communication simultanée des cylindres inactifs directement avec l'atmosphère ou avec la conduite d'échappement (méthode 2); désactivation des cylindres en maintenant les soupapes d'admission et d'échappement en position fermée et en arrêtant l'échange de gaz dans cylindres au ralenti(méthode 3).
N° 26. Recirculation des gaz d'échappement dans un moteur diesel.
Les gaz d'échappement des moteurs diesel contiennent une petite quantité de substances nocives, donc avant il n'était pas nécessaire d'installer sur une voiture dispositifs spéciaux. Mais au fil du temps, les règles sont devenues plus strictes. Et tout cela grâce au contenu de particules de suie et d'oxyde d'azote dans les gaz d'échappement. Par conséquent, pour les moteurs diesel, des systèmes ont été utilisés pour réduire la toxicité des gaz d'échappement, qui comprennent la recirculation des gaz d'échappement diesel ainsi qu'un convertisseur qui permet de réduire la toxicité des gaz d'échappement en réduisant l'oxyde d'azote et en utilisant l'oxygène résultant pour brûler le monoxyde de carbone avec les hydrocarbures non brûlés et filtre à suie.
Le filtre à particules est un matériau filtrant poreux en carbure de silicium. Si l'on considère les conceptions des années passées, ils ont effectué un nettoyage périodique des filtres de la suie accumulée avec les gaz d'échappement, dans lesquels la température a été augmentée, enrichissant le mélange. Le filtre a été nettoyé par la commande de l'unité de contrôle après 400 500 km de course. Dans ce cas, il y a eu une forte augmentation des émissions d'autres substances nocives. Par conséquent, les filtres à particules modernes fonctionnent avec un catalyseur oxydant, avec lequel la suie est brûlée à la température la plus basse d'environ 250 degrés Celsius.
Dans les filtres de la nouvelle génération, le principe n'a pas beaucoup changé : rétention et destruction. Comment atteindre la température requise pour la combustion des particules de suie ? D'une part, le filtre est placé derrière le collecteur d'échappement. D'autre part, tous les 300 à 500 km de parcours, le contrôleur active le mode "injection multiphase", ce qui entraîne une augmentation de la quantité de carburant entrant dans le cylindre. Plus important encore, une fine couche de catalyseur recouvre la surface de l'élément filtrant, ce qui permet d'augmenter encore la température des gaz d'échappement à celle requise (560-600 degrés Celsius).
L'élément filtrant est une éponge microporeuse en céramique. Entre ses canaux, l'épaisseur de la paroi ne dépasse pas 0,4 mm, la surface filtrante est donc grande. Une telle "éponge" est souvent constituée de fibres d'acier ultra-fines recouvertes d'un catalyseur. En raison du garnissage dense, jusqu'à 80 % des particules dont la taille varie de 20 à 100 nm sont retenues.
De nouveaux filtres ont commencé à être utilisés pour contrôler le fonctionnement du moteur. Des capteurs de pression sont installés à l'entrée et à la sortie du filtre, et après réception d'un signal de leur part, le mode d'enrichissement s'active. Lorsque la différence entre les lectures devient significative, l'ordinateur indiquera clairement que "l'éponge" est obstruée par de la suie. La combustion est contrôlée par un capteur de température.
A titre d'exemple, il convient de citer un mécanisme moderne de recirculation des gaz d'échappement diesel, un système électronique qui contrôle moteur diesel EDC. La conception est représentée par un système d'échappement à plusieurs composants, qui comprend 7 capteurs: 2 sondes lambda, 2 température, 2 pression, un niveau de suie dans l'échappement. Cela comprend également 3 éléments de nettoyage - un convertisseur catalytique, un accumulateur de catalyseur, un filtre à particules de type stockage. À l'aide de capteurs installés dans le système d'échappement, les processus de formation du mélange et de combustion ont été optimisés. De nombreux systèmes moteur, alimentation en carburant et en air, recirculation des gaz d'échappement, accélérateur électronique et suralimentation ont été transférés pour contrôler le filtre à particules. Grâce à des capteurs de pression installés à l'entrée et à la sortie, le degré de contamination est contrôlé depuis le filtre à particules. La qualité des catalyseurs est évaluée en fonction des sondes lambda installées en entrée et en sortie. Le fonctionnement du système moteur est corrigé en fonction des lectures des sondes lambda, des capteurs de température et du niveau de suie à la sortie. À l'aide d'un convertisseur catalytique, les substances toxiques sont "transformées" en composés non toxiques et peu toxiques (eau, azote, dioxyde de carbone) et, à l'aide d'un catalyseur de stockage, une purification supplémentaire des particules d'oxyde d'azote et de suie prend place.
N ° 27. Système d'alimentation en air supplémentaire.
Ce système pompe l'air pendant 65 secondes soupapes d'échappement lorsque la température du liquide de refroidissement du moteur est comprise entre 15° et 35°C. En conséquence, des gaz d'échappement enrichis en oxygène sortent du moteur, ce qui favorise la postcombustion et permet au catalyseur de se réchauffer plus rapidement. Le système d'air auxiliaire est contrôlé par l'ECU Motronic via le relais de pompe secondaire vers la soupape d'admission d'air secondaire et la soupape combinée. Après chaque démarrage ultérieur du moteur et jusqu'à ce que la température du moteur atteigne 85 ° C, le système d'alimentation en air auxiliaire s'allume avec un retard de 20 secondes et fonctionne au ralenti du moteur pendant 5 secondes, tandis que le système est surveillé par un auto-contrôleur. -appareil de diagnostic. L'état des pièces du système d'alimentation en air auxiliaire est surveillé soit dans le "rapport de défaut final", soit si un défaut apparaît, il sera enregistré dans l'enregistreur de défauts. Lors de l'accès à la mémoire de l'enregistreur de défauts (le travail est effectué à la station-service), le défaut est facilement diagnostiqué et peut ensuite être corrigé. Pour certaines positions (voir Fig. 99) les explications supplémentaires suivantes sont données : - de l'air supplémentaire est injecté dans le conduit d'air 1 de la culasse ;
L'anneau de levage 4 est vissé à gauche sur la culasse ;
Une valve d'apport d'air supplémentaire est vissée dans la pince 5 ;
Le bouchon 7 est posé sur la soupape d'admission (couleur noire) ;
Le tuyau de dépression 8 est connecté entre le haut du collecteur d'admission et la conduite de distribution de carburant ;
Le tuyau d'arrivée 9 vient du haut filtre à air. Son raccordement doit être étanche, sans reprise d'air ;
La fiche 11 fait référence au moteur de la pompe à air. Il est noir et a deux épingles ;
Le support 12 maintient le moteur de la pompe à air. Il est vissé dans la prise d'air du ventilateur de refroidissement ;
Le collier de serrage 14 fixe le tuyau d'arrivée ;
Le tuyau de pression 15 est fixé entre le moteur de pompe 10 et la vanne combinée 17 ;
Le support 16 fixe la valve combinée au tube guide de la jauge pour contrôler le niveau d'huile ;
Changez toujours le joint torique 19.
Riz. 99. Éléments du système d'alimentation en air supplémentaire: 1 - canal d'air dans la culasse; 2 - boulon, 25 Nm ; 3 - tuyau d'aspiration ; 4 - oeil de levage; 5 - titulaire; 6 - soupape d'admission supplémentaire */** ; 7 - bloc de prise; 8 - tuyau d'aspiration ; 9 - tuyau d'arrivée ; 10 - moteur de pompe à air * ; 11 - bloc de prise; 12 - titulaire; 13 - boulon, 10 Nm; 14 - collier de serrage; 15 - tuyau sous pression; 16 - titulaire; 17 - vanne combinée; 18 - boulon, 15 Nm; 19 - Joint torique
N° 28. Système de ventilation du réservoir de carburant
Les principaux signaux d'entrée vers l'unité de commande du moteur pour réguler le système de ventilation du réservoir de carburant sont :
vitesse du vilebrequin
signal du débitmètre d'air massique correspondant à la charge du moteur
température du moteur
signaux du capteur d'oxygène
signaux des unités de contrôle papillons des gaz
Les vapeurs de carburant sont retenues dans l'adsorbeur 3. Il s'agit d'un conteneur à gicleurs reliés rempli d'un tensioactif - adsorbant. Les adsorbants, en plus d'une grande capacité d'absorption, doivent être caractérisés par des caractéristiques stables lorsque la température ambiante change, une désorption efficace (libération des vapeurs accumulées) et une stabilité lors de la répétition répétée des cycles d'adsorption-désorption, une immunité à l'humidité atmosphérique, une résistance mécanique élevée pour éviter abrasion pendant le fonctionnement du véhicule . L'adsorbant le plus acceptable est le charbon actif AG-3, obtenu à partir de charbon et de semi-coke. Après traitement des signaux d'entrée, l'unité de contrôle du moteur émet une commande d'ouverture de l'électrovanne 4. En conséquence, les vapeurs de carburant accumulées dans l'adsorbeur sont déviées vers le tuyau d'admission 6 du moteur puis brûlées dans ses cylindres. Cela modifie brièvement le rapport de carburant et d'air dans le mélange. Cette évolution du mélange est enregistrée par des capteurs d'oxygène 10, en fonction des signaux desquels le système de contrôle effectue la correction nécessaire. ventilation du carter. Le système de ventilation du carter est conçu pour réduire les émissions de substances nocives du carter moteur dans l'atmosphère. Lorsque le moteur tourne, les gaz d'échappement peuvent fuir des chambres de combustion dans le carter. Le carter contient également des vapeurs d'huile, d'essence et d'eau. Ensemble, ils sont appelés gaz de carter. L'accumulation de gaz de carter altère les propriétés et la composition huile moteur, détruit les parties métalliques du moteur.
Sur les moteurs modernes, un système de ventilation forcée du carter de type fermé est utilisé. système de ventilation du carter différents fabricants et sur différents moteurs peuvent avoir des conceptions différentes. Cependant, le général suivant éléments structurels système donné :
Séparateur d'huile;
soupape de ventilation du carter ;
tuyaux d'aération.
Grâce à la ventilation, les vapeurs d'essence et les gaz d'échappement sont éliminés du carter du moteur. Il existe deux types de ventilation de carter : fermée et ouverte. Chacun a ses propres inconvénients et avantages.
ventilation ouverte
ne fonctionne pas au ralenti ou à basse vitesse ;
sature le compartiment moteur de gaz d'échappement et pollue environnement(ce qui est pertinent, puisque vous y êtes également à proximité immédiate de la source de pollution) ;
il y a une possibilité d'aspirer l'air ambiant non filtré lorsque le moteur refroidit ;
structurellement plus simple (un seul tuyau de dérivation sur le couvercle des poussoirs).
aération fermée
augmente le goudronnage du carburateur (cependant, cela était important dans les années 1960, compte tenu des huiles alors disponibles; cela est moins critique lors de l'utilisation d'une huile moteur semi-synthétique moderne de haute qualité);
problèmes possibles avec le condensat ;
à grande vitesse, trop de poussée est créée dans l'aspiration et on pense que l'huile, qui a tendance à s'oxyder à partir de l'oxygène atmosphérique, raccourcit sa durée de vie;
des flashs du mélange air-carburant dans le carburateur sont possibles;
plus efficace en termes de consommation d'huile ;
N° 29. Système de refroidissement avec contrôle électronique
Les paramètres du moteur, entre autres, sont considérablement affectés par la régime de température liquide de refroidissement. L'augmentation de la température du liquide de refroidissement à charge partielle offre des conditions favorables au fonctionnement du moteur, ce qui a un effet positif sur la consommation de carburant et les émissions d'échappement. En raison de la température inférieure du liquide de refroidissement à pleine charge, la puissance du moteur est augmentée en refroidissant l'air d'admission et en augmentant ainsi la quantité d'air entrant dans le moteur. L'utilisation d'un système de refroidissement avec contrôle électronique de la température permet de réguler la température du liquide à charge partielle du moteur dans la plage de 95 à 110°C et à pleine charge de 85 à 95°C. Le système de refroidissement du moteur à commande électronique optimise la température du liquide de refroidissement en fonction de la charge du moteur. Selon le programme d'optimisation stocké dans la mémoire de l'unité de commande du moteur, la température de fonctionnement requise du moteur est atteinte grâce à l'action du thermostat et des ventilateurs. De cette façon, la température du liquide de refroidissement est adaptée à la charge du moteur. Les principaux composants distinctifs du système de refroidissement à commande électronique de celui habituel sont la présence d'un distributeur de liquide de refroidissement avec un thermostat électronique. Dans le cadre de l'introduction de la commande électronique du système de refroidissement, l'unité de commande du moteur reçoit les éléments suivants Informations Complémentaires:
alimentation du thermostat (signal de sortie)
température du liquide de refroidissement à la sortie du radiateur (signal d'entrée)
commande de ventilateur de radiateur (2 sorties)
position du potentiomètre sur le régulateur du système de chauffage (signal d'entrée)
Lorsque le liquide de refroidissement est chauffé, la charge 2 se liquéfie et se dilate, ce qui entraîne la montée de la broche 1. Lorsque la résistance chauffante n'est pas alimentée, le thermostat agit comme un thermostat traditionnel, mais la température de son fonctionnement est augmentée et est de 110 °C (température d'eau en sortie moteur). Une résistance chauffante 3 est intégrée dans la charge.Lorsqu'un courant lui est appliqué, elle chauffe la charge 2, qui se dilate, à la suite de quoi la broche s'étend d'une certaine quantité "x" en fonction du degré de chauffage de la charge. La broche 1 se déplace désormais non seulement sous l'influence du liquide de refroidissement chauffé, mais également sous l'influence du chauffage par résistance, et le degré de son échauffement est déterminé par l'unité de commande du moteur conformément au programme d'optimisation de la température du liquide de refroidissement intégré dans ce. Selon la nature de l'impulsion et le moment de son alimentation, le degré d'échauffement de la charge change.
Le distributeur est situé à la place des raccords de connexion au niveau de la culasse et est un dispositif permettant de diriger le flux de liquide de refroidissement dans un petit ou un grand cercle. À pleine charge du moteur, un refroidissement intensif du liquide de refroidissement est nécessaire. Le thermostat du distributeur reçoit du courant et ouvre la voie au fluide du radiateur. En même temps, au moyen d'une connexion mécanique, un petit disque de soupape bloque le chemin vers la pompe dans un petit cercle. La pompe fournit le liquide de refroidissement sortant de la tête de bloc directement au radiateur. Le liquide refroidi du radiateur pénètre dans la partie inférieure du bloc moteur et est aspiré à partir de là par la pompe. La circulation combinée du liquide de refroidissement est également possible. Une partie du liquide passe à travers un petit cercle, l'autre - à travers un grand.
Contrôle du thermostat dans un système de refroidissement moteur optimisé (mouvement du liquide de refroidissement en petites ou grand cercle) est réalisé selon des graphes de dépendance tridimensionnels température optimale liquide de refroidissement sur un certain nombre de facteurs, les principaux étant la charge du moteur, le régime moteur, la vitesse du véhicule et la température de l'air d'admission. Selon ces graphiques, la valeur de la température nominale du liquide de refroidissement est déterminée.
N° 30. Moteurs fonctionnant au carburant gazeux. Le système d'alimentation, fonctionnant sur le principe de la carburation, installé sur moteur à essence avec système d'injection électronique.
MAIS) moteur à gaz- un moteur à combustion interne qui utilise des gaz d'hydrocarbures liquéfiés (propane-butane) ou du gaz naturel (méthane) comme carburant.
La différence avec les moteurs à essence fonctionnant sur ce cycle est un taux de compression plus élevé (environ 17). Cela s'explique par le fait que les gaz utilisés ont une plus grande indice d'octane que l'essence.
Les moteurs sont divisés en :
spécial (ou modifié), destiné uniquement à fonctionner au gaz, l'essence est utilisée pendant une courte période en cas de dysfonctionnement de l'équipement à gaz, lorsqu'il n'est pas possible d'effectuer des réparations sur place;
universel, conçu pour long travailà la fois le gaz et l'essence.
En voiture, le mélange propane-butane liquéfié se présente dans des bouteilles en acier sans soudure (sans soudure) installées sur le châssis, sous le plancher du bus ou dans le coffre d'une voiture. Le gaz liquéfié est dans une bouteille à une pression de 16 atmosphères (la bouteille est conçue pour une pression maximale de 25 atmosphères).
Cylindres pour comprimé gaz naturel situé sur le châssis, sous le plancher de l'habitacle du bus ou sur son toit (le gaz comprimé n'est pas utilisé sur les voitures particulières - il y a très peu de place pour les bouteilles encombrantes et lourdes). Le méthane comprimé est sous pression jusqu'à 150 atmosphères. Plusieurs bouteilles sont combinées dans une ligne commune, il y a une vanne de remplissage commune, chaque bouteille a également sa propre vanne.
Le gaz de la ligne commune entre dans l'évaporateur (réchauffeur) - un échangeur de chaleur inclus dans le système refroidissement liquide, après le réchauffement du moteur, le gaz est chauffé (le gaz liquéfié s'évapore) à une température de ≈75 °C. Ensuite, le gaz passe à travers le filtre principal.
Ensuite, le gaz entre dans un réducteur de gaz à deux étages, où sa pression est réduite à celle de travail.
De plus, le gaz pénètre dans le mélangeur (ou dans le carburateur-mélangeur ou dans l'entretoise de mélange sous le carburateur standard, déterminé par la conception de l'équipement de carburant). Les mélangeurs sont conçus de la même manière que les carburateurs, ils ont un papillon et un amortisseur d'air, un système de ralenti, un système pour travailler sur pleine puissance et etc.
B) Le système d'alimentation en gaz liquéfié, fonctionnant sur le principe de la carburation, est utilisé à la fois sur les moteurs à essence équipés d'un carburateur et sur les moteurs équipés d'un système d'injection d'essence. Un système d'alimentation qui fonctionne sur le principe de la carburation lorsqu'il est utilisé sur des moteurs avec injection électronique l'essence, en plus des principaux éléments d'un système d'injection classique, contient un récepteur 2, un réducteur-évaporateur 6, un servomoteur de contrôle du débit de gaz 7, une canalisation d'alimentation en gaz d'un diffuseur.
Riz. Système d'alimentation en GPL fonctionnant sur le principe de la carburation, installé sur un moteur à essence avec un système d'injection électronique :
1 - tube de ventilation pour le récepteur de gaz ; 2 - récepteur à gaz liquéfié; 3 - raccords du récepteur de gaz; 4 - vanne de remplissage ; 5 - vanne d'arrêt de gaz ; 6 - réducteur-évaporateur; 7 – servomoteur pour le contrôle du débit de gaz ; 8 – unité de contrôle électronique ; 9 - commutateur pour le type de carburant utilisé "essence-essence"; 10 - diffuseur-mélangeur; 11 - sonde lambda; 12 – capteur de vide ; 13 - batterie d'accumulateurs; 14 - contacteur d'allumage; 15 - relais
Lors du passage à l'utilisation du gaz comme combustible, le gaz s'écoule du récepteur 2 vers le réducteur-évaporateur, où la pression du gaz diminue et il s'évapore. En fonction des signaux provenant des capteurs, l'unité de commande envoie un certain signal au servomoteur 7, qui détermine le débit de gaz à un certain mode de fonctionnement du moteur. Le gaz à travers le pipeline pénètre dans le diffuseur, où il se mélange à l'air et passe à la soupape d'admission, puis au cylindre du moteur. Pour contrôler le fonctionnement du moteur, des unités de commande séparées sont prévues pour le fonctionnement du moteur à l'essence et au gaz. Il y a un échange d'informations entre les deux unités de contrôle.
N° 31. Le système d'alimentation du moteur fonctionnant au gaz naturel comprimé.
Moteurs automobiles peut fonctionner sur gaz comprimé et liquéfié. Schéma d'implantation du système d'alimentation en fonctionnement au gaz comprimé : réchauffeur de cylindre - détendeur haute pression - mélangeur-carburateur détendeur basse pression. Système d'alimentation électrique pour moteurs à gaz comprimé. Les cylindres inclus dans le système sont en acier et sont conçus pour une pression de service de 19,6 MPa. Leur capacité est de 50 litres, poids 93 kg. Les vannes sont utilisées pour fermer les conduites lorsque le moteur ne tourne pas. Le réchauffeur de gaz sert à empêcher le gel éventuel de l'humidité dans le gaz. Il est réalisé sous la forme de plusieurs tours d'un gazoduc haute pression sur le collecteur d'échappement. Le réducteur de gaz haute pression (HRVD) est utilisé pour réduire la pression du gaz à 1,2 MPa. Le gaz du cylindre pénètre dans la cavité du réducteur à travers un raccord avec un raccord et un filtre en céramique vers la vanne. Le ressort de la boîte de vitesses appuie sur la soupape par le haut à travers le poussoir et le diaphragme. Lorsque la pression de gaz dans d'autres cavités est inférieure à celle spécifiée, le ressort réducteur abaisse la soupape à travers le poussoir, faisant passer le gaz à travers l'espace formé dans la cavité dans la même cavité. Le gaz passe ensuite à travers un filtre supplémentaire. Lorsque la pression prédéterminée dans la cavité est atteinte, sa force sur la membrane équilibre le ressort et la soupape ferme le passage du gaz. La pression de sortie est réglée avec un bouton à vis. Le fonctionnement du détendeur est contrôlé par un manomètre qui reçoit un signal d'un capteur haute pression et un dispositif de signalisation de perte de charge en sortie.
Le réducteur de gaz basse pression (GRND) réduit la pression à la valeur de travail nécessaire à l'alimentation du mélangeur (0,085 - 0,08 MPa). À
Un dispositif dans lequel une pompe à carburant haute pression est combinée dans un boîtier avec un injecteur est appelé système d'alimentation pompe-injecteur.
Histoire des inventions
La plupart des sources affirment que l'utilisation d'injecteurs de pompe dans les moteurs en série remonte au milieu des années 90, cependant, il existe des informations qui nous permettent de tirer d'autres conclusions. Dans le schéma Robert Bosch, toutes les buses sont alimentées par une pompe commune. Cependant, aux États-Unis en 1938, la société Detroit Diesel, détenue, a construit le premier moteur diesel produit en série au monde avec un système d'alimentation à pompe-injecteur.La pression dans le système d'alimentation en carburant par les injecteurs-pompes est si forte que, en cas de fuite, le jet de carburant peut "couper" en même temps les vêtements et la peau du bras
Dans le même temps, l'URSS travaillait activement à la création de son propre équipement de carburant pour camions. Mais après quelques tentatives infructueuses, il a été décidé d'acheter une licence pour la série Detroit Diesel 3-71, qui avait fait ses preuves lors des essais, et de lancer sa production à Yaroslavl. , mais le processus a d'abord été retardé à cause des Finlandais, puis de la Grande Guerre patriotique. Ce n'est qu'en 1945 que les premières machines-outils et équipements pour la production de Moteurs américains. En 1947, le premier quatre cylindres à deux temps moteurs diesel YaAZ 204 avec un système d'alimentation avec des buses de pompe. Ce moteur, ainsi qu'un analogue à six cylindres fabriqué sur sa base, ont été produits avec quelques modifications jusqu'en 1992. En 1994, il a produit son premier camion européen FH12 avec injecteurs unitaires. Après les Suédois, un tel système d'alimentation apparaît sur Scania et Iveco.
Sous pression, les injecteurs de pompe détruisent souvent l'atterrissage dans le bloc moteur diesel
Dans le segment voitures Le championnat du développement de moteurs à injecteurs-pompes appartient à Volkswagen. Sur les voitures de cette société, des moteurs diesel à injecteurs-pompes sont apparus en 1998.
Buses de pompe mécanique
L'injecteur-pompe se compose de pompe à carburant partie haute pression et pulvérisation dans un seul boîtier. La pompe à essence haute pression est en haut, l'atomiseur en bas. L'injecteur de la pompe est généralement situé sous couvercle de soupape et vous ne pouvez pas le voir de l'extérieur. La particularité de l'emplacement est due au fait que la pompe est entraînée par des cames supplémentaires fournies sur.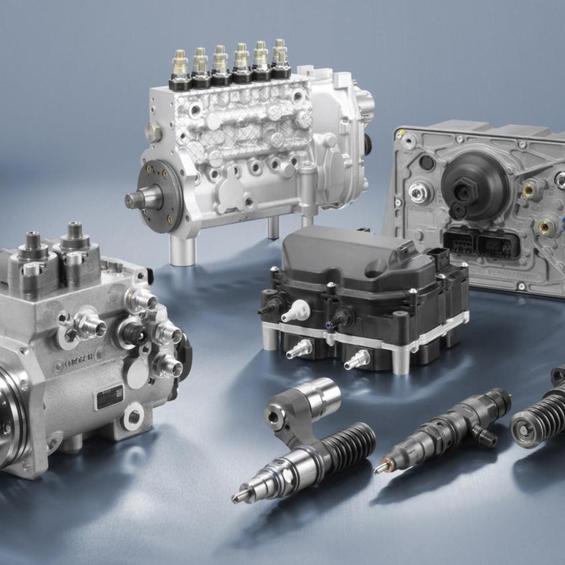
Injecteurs unitaires électroniques
Les injecteurs-pompes électroniques modernes fonctionnent un peu différemment. La pression est créée de la même manière que dans une mécanique - à l'aide d'un piston, mais l'unité de commande électronique du moteur contrôle le moment de l'injection. Le nombre de portions de carburant fournies peut atteindre jusqu'à dix par cycle en trois phases principales. La première est une injection préliminaire, lorsqu'une petite portion de carburant est fournie au cylindre pour préchauffer la chambre de combustion et mieux enflammer la seconde portion principale qui suit. La troisième phase est destinée à la postcombustion du combustible non brûlé et au chauffage (régénération).Le coût minimum d'un injecteur-pompe pour une VW Passat 2006 est de 18 000 roubles
Pour assurer un dosage précis de chaque portion de carburant et fournir plusieurs injections en un cycle, une électrovanne est utilisée qui contrôle la levée de l'aiguille de l'atomiseur.
Avantages et inconvénients de la buse de pompe
Les injecteurs pompe, contrairement à l'injection batterie, permettent d'injecter du carburant à une pression supérieure à 2000 bars. De ce fait, le carburant est atomisé plus efficacement et, par conséquent, il brûle plus complètement. Par conséquent, les moteurs à injecteurs-pompes se caractérisent par une densité de puissance, une efficacité et un respect de l'environnement élevés.En outre, les moteurs dotés d'un tel système d'injection sont plus silencieux que leurs homologues équipés de pompes à injection Common Rail ou mécaniques. De plus, le système d'injection à injecteurs-pompes est beaucoup plus compact, certes, les inconvénients de ce système ne sont pas moins sérieux. Le plus important est les exigences extrêmes des injecteurs-pompes sur la qualité du carburant. L'eau, la saleté et le carburant de substitution sont mortels pour eux.Le deuxième inconvénient majeur est le coût élevé de l'injecteur-pompe. La réparation de cet ensemble de précision est difficile à réaliser en dehors de l'usine. Par conséquent, les propriétaires de voitures équipées d'un tel système d'alimentation doivent acheter de nouveaux injecteurs de pompe.Fonctionnement et entretien de l'injecteur-pompe
Les dysfonctionnements les plus courants des injecteurs-pompes sont liés à l'usure de l'ensemble valve et des pulvérisateurs. La raison de la défaillance de ces nœuds est liée, tout d'abord, et mauvais fonctionnement voiture avec ce système Afin de prolonger la durée de vie des injecteurs-pompes, plusieurs règles simples. Premièrement, vous devez faire le plein uniquement dans des stations-service éprouvées.A la fin des années 90, les moteurs à injecteurs-pompes occupaient 20% du marché européen des équipements diesel.
Deuxièmement, il ne faut en aucun cas ajouter de l'essence, du kérosène, liquide de frein et d'autres astuces "KAMAZ" pour amener le carburant diesel d'été à la résistance au gel en hiver.Troisièmement, il est nécessaire de réduire l'intervalle de remplacement des filtres à carburant. De plus, vous pouvez installer, autorisé par le fabricant. Parce que les analogues ne fournissent souvent pas niveau requis filtration.