Привод сцепления предназначен для обеспечения выключения сцепления, а именно отжимания диафрагменной пружины. На современных автомобилях применяются приводы сцепления следующих видов: механический, гидравлический и электрогидравлический.
Наибольшее применение в автомобиле нашли механический и гидравлический приводы сцепления. Электрогидравлический привод используется для автоматизации управления сцеплением в роботизированной коробке передач , например, в коробке передач Easytronic .
Механический привод используется в качестве привода сцепления небольших легковых автомобилей. Данный вид привода отличает простота конструкции и невысокая стоимость.
Механический привод сцепления объединяет педаль сцепления, приводной трос и рычажную передачу. На тросе располагается механизм регулирования свободного хода педали сцепления.
Основным конструктивным элементом механического привода сцепления является трос, который соединяет педаль сцепления с вилкой выключения. Трос заключен в оболочку. При нажатии на педаль сцепления усилие через трос передается на рычажную передачу, которая в свою очередь перемещает вилку сцепления и обеспечивает выключение сцепления.
В системе предусмотрен механизм регулирования свободного хода педали сцепления, включающий регулировочную гайку на конце троса. Необходимость регулировки обусловлена постепенным изменением положения педали сцепления вследствие износа фрикционных накладок.
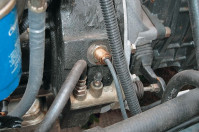
Гидравлический привод сцепления по конструкции аналогичен гидравлическому приводу тормозной системы. В нем используется свойство несжимаемости жидкости. В качестве рабочей жидкости применяется тормозная жидкость.
Гидравлический привод сцепления имеет более сложную конструкцию. Помимо педали привод включает главный и рабочий цилиндры, бачек рабочей жидкости и соединительные трубопроводы.
Конструктивно главный и рабочий цилиндры состоят из поршня с толкателем, размещенных в корпусе. При нажатии на педаль сцепления толкатель перемещает поршень главного цилиндра, происходит отсечка рабочей жидкости от бачка. При дальнейшем движении поршня рабочая жидкость по трубопроводу поступает в рабочий цилиндр. Под воздействием жидкости происходит движение поршня с толкателем. Толкатель воздействует на вилку сцепления и обеспечивает выключение сцепления.
Для удаления воздуха из системы гидропривода сцепления (прокачки системы) на главном и рабочем цилиндрах установлены специальные клапаны (штуцеры ).
Для облегчения управления на некоторых моделях автомобилей используются пневматический или вакуумный усилитель привода сцепления.
Важной составляющей автомобиля, оснащенного механической коробкой передач, является сцепление. Оно состоит непосредственно из муфты (корзины) сцепления и привода. Остановимся более подробно на таком элементе, как привод сцепления, который играет важную роль в общем узле сцепления. Именно при его неисправности муфта теряет свою функциональность. Разберем устройство привода, его виды, а также преимущества и недостатки каждого.
Привод предназначен для дистанционного управления сцеплением непосредственно водителем из салона. Нажатие на педаль сцепления напрямую воздействует на нажимной диск.
Известны следующие виды привода:
- механический
- гидравлический
- электрогидравлический
- пневмогидравлический
Наибольшее распространение получили первые два вида. На грузовиках и автобусах используется пневмогидравлический привод. Электрогидравлический устанавливают в машинах с роботизированной коробкой передач.
В некоторых автомобилях для облегчения управления применяется пневматический или вакуумный усилитель привода.
Механический привод
Механический или тросовый привод отличается простой конструкцией и невысокой ценой. Он неприхотлив в обслуживании и состоит из минимального количества элементов. Механический привод устанавливается в легковых и малотоннажных грузовых автомобилях.
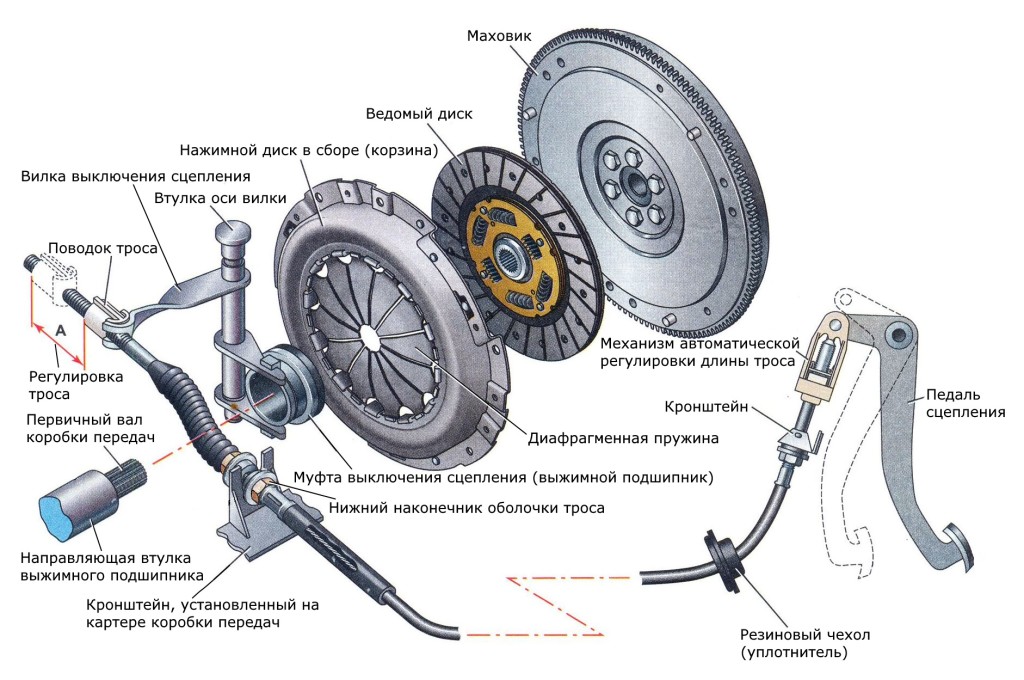
К элементам механического привода относятся:
- трос сцепления
- педаль сцепления
- вилка выключения сцепления
- выжимной подшипник
- механизм регулировки
Трос сцепления, заключенный в оболочку, является основным элементом привода. Трос сцепления крепится к вилке, а также к педали, находящейся в салоне автомобиля. В момент выжимания педали водителем действие через трос передается на вилку и выжимной подшипник. В результате происходит разъединение маховика двигателя с трансмиссией и, соответственно, выключение сцепления.
В соединении троса и рычажного привода предусмотрен регулировочный механизм, обеспечивающий свободный ход педали сцепления.
Ход педали сцепления представляет собой свободное перемещение до момента срабатывания привода. Расстояние, пройденное педалью без особого усилия водителя при нажатии, и есть свободный ход.
Если переключение передач сопровождается шумом, а в начале движения наблюдаются небольшие рывки автомобиля, то необходима регулировка хода педали.
Зазор в сцеплении должен находиться в пределах 35-50 мм свободного хода педали. Нормативы этих показателей указаны в технической документации автомобиля. Регулировка хода педали осуществляется путем изменения длины тяги с помощью регулировочной гайки.
В грузовых автомобилях используется не тросовый, а рычажный механический привод.
К плюсам механического привода относятся:
- простота устройства
- невысокая стоимость
- надежность в эксплуатации
Главным минусом считается более низкий КПД по сравнению с гидроприводом.
Гидравлический привод сцепления
Гидропривод имеет более сложную конструкцию. К его элементам, помимо выжимного подшипника, вилки и педали, относится также гидравлическая магистраль, которая заменяет трос сцепления.
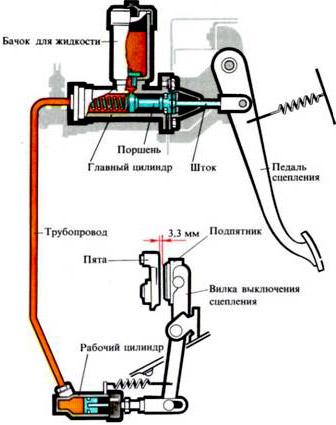
По сути эта магистраль аналогична гидроприводу тормозной системы и состоит из следующих элементов:
- главный цилиндр сцепления
- рабочий цилиндр сцепления
- бачок и трубопровод с тормозной жидкостью
Устройство главного цилиндра сцепления напоминает устройство главного тормозного цилиндра. Главный цилиндр сцепления состоит из поршня с толкателем, расположенных одном в корпусе. Также к его элементам относятся резервуар для жидкости и уплотнительные манжеты.
Рабочий цилиндр сцепления, имеющий схожую с главным цилиндром конструкцию, дополнительно оснащен клапаном для удаления воздуха из системы.
Механизм действия гидропривода такой же, как и у механического, только усилие передается с помощью находящейся в трубопроводе жидкости, а не через трос.
Во время нажатия водителем на педаль усилие через шток передается на главный цилиндр сцепления. Затем за счет несжимаемого свойства жидкости в действие приводятся рабочий цилиндр сцепления и рычаг привода выжимного подшипника.
В качестве плюсов гидропривода можно выделить следующие его особенности:
- гидравлическое сцепление позволяет передавать усилие на значительное расстояние с высоким КПД
- сопротивление перетеканию жидкости в элементах гидропривода способствует плавному включению сцепления
Главный минус гидропривода – более сложный ремонт по сравнению с механическим. Течь рабочей жидкости и попадание в систему гидропривода воздуха — вот, пожалуй, наиболее распространенные поломки, которыми могут «похвастаться» главный и рабочий цилиндры сцепления.
Гидропривод применяется в легковых автомобилях, а также на грузовых автомобилях с опрокидывающейся кабиной.
Нюансы эксплуатации сцепления
Зачастую водители склонны связывать неравномерность и рывки при движении автомобиля с неисправностями сцепления. Эта логика в большинстве случаев ошибочна.
Например, автомобиль при переключении передач с первой на вторую, резко сбрасывает обороты. Здесь виновато не само сцепление, а датчик положения педали сцепления. Находится он за самой педалью сцепления. Неисправности датчика устраняются путем несложного ремонта, после которого сцепление будет вновь работать плавно и без рывков.
Другая ситуация: при переключении передач автомобиль немного дергается, а при трогании с места может заглохнуть. В чем может быть причина? Чаще всего в этом виноват клапан задержки сцепления. Этот клапан обеспечивает определенную скорость, при которой может схватываться маховик, независимо от того, насколько быстро была «брошена» педаль сцепления. Для начинающих водителей эта функция необходима, т.к. клапан задержки сцепления предотвращает чрезмерный износ поверхности диска сцепления.
1.1. Назначение, устройство и работа сцепления
Сцепление предназначено для кратковременного отключения трансмиссии от двигателя и плавного их соединения во время начала движения и при переключении передач. Сцепление состоит из привода и механизма.
Сцепление автомобиля ГАЗ-3307 однодисковое, сухое, рычажное, с периферийными пружинами, гасителем крутильных колебаний, установлено в картере 2 (рис.1).
Рис. 1 Устройство механизма сцепления автомобиля: 1 - маховик; 2 - картер; 3 - ведомый диск; 4 - нажимной диск; 5 - рычаг нажимного диска; 6 - масленка; 7 - регулировочная гайка; 8 - муфта выключения сцепления; 9 - первичный вал коробки передач; 10 - вилка; 11 - кожух; 12 - нажимная пружина.
Основными элементами сцепления являются ведомый диск 3 в сборе с фрикционными накладками и нажимной диск 4 в сборе с кожухом 11 и рычагами 5.
Ведомый диск состоит из ступицы, которая установлена на шлицах первичного вала коробки передач и может по ним передвигаться. В ступице изготовлены восемь окон, в которых размещены пружины демпферного механизма, которые предназначены для гашения резких изменений крутящего момента двигателя. Кроме того, в ступице прорезаны четыре паза, в которых размещены опорные пальцы, соединяющие диск сцепления и пластину демпфера. Между ступицей ведомого диска и диском, а также между ступицей и пластиной демпфера размещены фрикционные шайбы. Пластина демпфера выштампована из листовой стали, в ней сделаны восемь вырезов под демпферные пружины. Вырезы имеют отбортовки, предназначенные для удержания пружин. Такие же вырезы есть и в диске сцепления. Диск соединен с пластиной демпфера с помощью четырех расклепаных опорных пальцев, проходящих через вырезы в ступице диска сцепления. На ведомый диск приклепаны фрикционные накладки, причем спереди накладка приклепана непосредственно к диску, а с противоположной стороны - через пружинную пластину. Пружинная пластина обеспечивает необходимое «отпружинивание» ведомого диска, что обеспечивает плавное включение сцепления.
Ведомый диск при включенном сцеплении зажат между маховиком двигателя и нажимным диском.
Нажимной диск - литой чугунный, имеет три выступа, которыми устанавливается в окна кожуха. Нажимной диск соединен с маховиком двигателя через кожух, который крепится к маховику болтами. С обратной стороны диска и с внутренней кожуха есть выштамповки для установки нажимных пружин.
Отвод нажимного диска от ведомого в момент выключения сцепления осуществляется тремя нажимными рычагами. Рычаги - кованые, стальные, имеют по два отверстия. Через верхнее отверстие рычаг пальцем со шплинтом крепится к нажимному диску. Рычаг может поворачиваться относительно пальца на подшипнике. Через нижнее отверстие нажимной рычаг с помощью опорной вилки, пружины, вилки и регулировочной гайки соединен с кожухом.
Выключение сцепления осуществляется путем перемещения свободных концов нажимных рычагов. Рычаг поворачивается относительно оси, соединяющей рычаг с опорной вилкой и отводит нажимной диск от ведомого.
Кожух сцепления закреплен на маховике 1 коленчатого вала шестью центрирующими (специальными) болтами. Между кожухом и диском 4 установлено двенадцать нажимных пружин. Усилие сжатия пружин обеспечивает создание необходимой силы трения и передачи крутящего момента от маховика через кожух и нажимной диск на ведомый диск сцепления. Что бы не допустить перегрев пружин и их отпуск (усадку) они установлены через текстолитовые прокладки.
Для выключения сцепления служат три рычага 5. Точками опоры рычагов на кожухе являются специальные гайки 7. Одновременность нажатия выжимным подшипником на все рычаги регулируют гайками 7, которые после регулировки раскернивают. В процессе эксплуатации автомобиля эти рычаги, как правило, не регулируют.
Для выключения сцепления служит упорный (выжимной) подшипник, установленный на муфте 8. Муфта выключения сцепления изготовлена из чугуна и имеет два прилива, в которые упирается своими концами вилка выключения сцепления. В передней части муфта имеет буртик, на который напрессован шарикоподшипник. В корпусе муфты имеется резьбовое отверстие, в который затянуты гибкий шланг 6 для смазки подшипников. Муфта с напрессованном на нее подшипником установлена на направляющей передней крышки коробки передач и может передвигаться по ней. Для того, чтобы при включенном сцеплении подшипник не дотрагивался нажимных рычагов, муфта выключения сцепления удерживается пружиной.
Между концами рычагов нажимного диска и подшипником выключения сцепления необходим зазор 2,5-3,0 мм, который обеспечивается при свободном ходе 4-5 мм наружного конца вилки 10 включения сцепления и соответствует свободному ходу педали 40-55 мм при неработающем двигателе.
Привод выключения сцепления - гидравлический, состоит из подвесной педали 8 (рис. 2), главного цилиндра 3, трубопровода и рабочего цилиндра 13.
Рис. 2 Устройство гидравлического привода выключения сцепления: 1 - питающий бачок; 2 - питающий шланг; 3 - главный цилиндр; 4 защитный колпак; 5 - толкатель главного цилиндра; 6 - муфта выключения сцепления; 7 - вилка; 8 педаль; 9 - регулировочная гайка; 10 - контргайка; 11 - толкатель; 12 - оттяжная пружина; 13 цилиндр; 14 - поршень; 15 - клапан прокачки; 16 - поршень главного цилиндра; 17 - манжета; А компенсационное отверстие; В - перепускное отверстие.
Педаль сцепления установлена на оси кронштейна педали на двух пластмассовых втулках, не требующих смазки в эксплуатации, и передает усилие на толкатель 5 главного цилиндра 3. В крайнее заднее положение педаль возвращается оттяжной пружиной 12. При этом ограничение хода педали в заднем положении осуществляется упором сферической головки толкателя 5 в шайбу главного цилиндра. Между толкателем 5 и поршнем 16 главного цилиндра сцепления предусмотрен постоянный зазор, который при сборке и в процессе эксплуатации не регулируется.
Главный цилиндр управления сцепления установлен на щитке передка кабины и соединен шлангом 2 с одной из секций трехсекционного питающего бачка 1, снабженного датчиком сигнализатора аварийного падения уровня тормозной жидкости (две друга секции бачка питают гидравлический привод двухконтурной рабочей тормозной системы). Цилиндр состоит из чугунного корпуса, в котором размещен поршень уплотненный двумя манжетами и пружина. С одного торца цилиндр закрыт пробкой, с другого имеет стопорное кольцо в которое упирается поршень. С этого конца цилиндр прикрыт пыльником. В верхней части цилиндр имеет штуцер для подвода жидкости из пополнительного бачка.
Рабочий цилиндр сцепления крепится к картеру сцепления двумя болтами.
Имеет похожее устройство с главным цилиндром. Отличается размерами (он меньше) и тем, что штуцер подвода жидкости находится с торца корпуса цилиндра. Для удаления из системы воздуха в рабочий цилиндр ввернут клапан 15, закрытый резиновым колпачком.
Информация о работе «Организация работ по диагностированию, техническому обслуживанию и ремонту сцепления ГАЗ 3307 в агрегатном цехе автотранспортного предприятия»
Автомобилей. – М.: Транспорт, 1987. 6. Карташов В.П. Технологическое проектирование автотранспортных предприятий. – М.: Транспорт, 1981. Приложение 1 Министерство сельского хозяйства Российской Федерации ФГОУ ВПО «Ижевская государственная сельскохозяйственная академия» Кафедра «Эксплуатация машинно-тракторного парка» КУРСОВОЙ ПРОЕКТ пояснительная записка Тема проекта: ...
Комплекса (выходные формы); - производит анализ по результатам обработки информации и передает материалы руководству для принятия конкретных мер и разработки мероприятий по совершенствования работы информационно технической системы автотранспортного предприятия; - в лицевых карточках автомобиля ведет учет цепочки пробега, отмечает случаи замен основных агрегатов (двигателя, коробки передач, ...
Технической готовности представлен на рисунке 1. Коэффициент технической готовности Рис. 1 Коэффициент использования подвижного состава для "перевозок" (коэффициент выпуска) зависит от интенсивности эксплуатации и «возраста» автопарка. Совершенствование транспортного процесса обеспечивает постоянное повышение интенсивности эксплуатации автомобильного парка, увеличивает пробег автомобилей...
0,5 данные виды работ следует предусматривать по кооперации на других предприятиях или специально оговариваться заданием на проектирование. 1.17. При разработке технологической части проекта следует использовать типовые технологические процессы ТО и ремонта подвижного состава автомобильного транспорта, разработанные научными организациями с применением прогрессивной технологии и оборудования. ...
Сцепление - неотъемлемая часть любого современного автомобиля. Именно этот узел принимает на себя все колоссальные нагрузки и удары. Особенно испытывают устройства на автомобилях с механической КПП. Как вы уже поняли, в сегодняшней статье мы рассмотрим принцип работы сцепления, его конструкцию и назначение.
Характеристика элемента
Сцепление представляет собой силовую муфту, которая осуществляет передачу крутящего момента между двумя основными составляющими автомобиля: двигателем и коробкой передач. Состоит оно из нескольких дисков. В зависимости от типа передачи усилий данные муфты могут быть гидравлическими, фрикционными или же электромагнитными.
Назначение
Автоматическое сцепление предназначено для временного отсоединения трансмиссии от двигателя и плавной их притирки. Необходимость в ней возникает по мере того, как начинается движение. Временное разъединение мотора и КПП нужно и при последующем переключении скоростей, а также при резком торможении и остановке транспортного средства.
Во время движения машины система сцепления находится по большей части во включенном состоянии. В это время она передает мощность от двигателя к коробке переключения передач, а также предохраняет механизмы КПП от различных динамических нагрузок. Тех, которые возникают в трансмиссии. Таким образом, нагрузки на нее возрастают по мере торможения двигателя, при резком включении сцепления, снижении частоты оборотов коленвала либо при наезде транспортного средства на неровности дорожного полотна (ямы, выбоины и так далее).
Классификация по связи ведущих и ведомых частей
Сцепление классифицируют по нескольким признакам. По связи ведущих и ведомых частей принято различать следующие типы устройств:
- Фрикционные.
- Гидравлические.
- Электромагнитные.
По типу создания нажимных усилий
По данному признаку различают типы сцепления:
- С центральной пружиной.
- Центробежные.
- С периферийными пружинами.
- Полуцентробежные.
По количеству ведомых валов системы бывают одно-, двух- и многодисковые.
По типу привода
- Механический.
- Гидравлический.
Все вышеуказанные типы сцеплений (за исключением центробежных) являются замкнутыми, то есть постоянно выключенными или включенными водителем при переключении скоростей, остановке и торможении транспортного средства.
На данный момент большую популярность обрели системы фрикционного типа. Такие узлы используются как на легковых, так и на грузовых автомобиля, а также на автобусах малого, среднего и большого класса.
2-дисковые сцепления используются только на крупнотоннажных тягачах. Также они устанавливаются на автобусы большой вместимости. Многодисковые же практически не применяются автопроизводителями в данный момент. Раньше они использовались на большегрузах. Также стоит отметить, что гидромуфты в качестве отдельного узла на современных машинах не применятся. До недавнего времени они использовались в коробках автомобилей, однако только совместно с последовательно установленным фрикционным элементом.
Что касается электромагнитных сцеплений, то они на сегодняшний день не получили широкого распространения в мире. Связано это со сложностью их конструкции и с дорогостоящим обслуживанием.
Принцип работы сцепления с механическим приводом
Стоит отметить, что данный узел имеет одинаковый принцип работы вне зависимости от количества ведомых валов и типа создания нажимных усилий. Исключение составляет тип привода. Напомним, он бывает механическим и гидравлическим. И сейчас мы рассмотрим принцип работы сцепления с механическим приводом.
Как же действует данный узел? В рабочем состоянии, когда педаль сцепления не затронута, ведомый диск зажат между нажимным и маховиком. В это время передача крутящих усилий на вал производится за счет силы трения. Когда водитель нажимает ногой на педаль, трос сцепления перемещается в корзине. Далее рычаг поворачивается относительно своего места крепления. После этого свободный конец вилки начинает давить на выжимной подшипник. Последний, перемещаясь к маховику, - давить на пластины, которые отодвигают нажимной диск. В данный момент ведомый элемент освобождается от прижимающих усилий и таким образом происходит отсоединение сцепления.
Далее водитель свободно производит переключение передачи и начинает плавно отпускать педаль сцепления. После этого система вновь включает в связь ведомый диск с маховиком. По мере отпускания педали сцепление включается, происходит притирка валов. Через некоторое время (пару секунд) узел в полной мере начинает передавать крутящий момент на двигатель. Последний через маховик осуществляет привод на колеса. Стоит отметить, что трос сцепления присутствует только на узлах с механическим приводом. Нюансы конструкции другой системы мы опишем в следующем разделе.
Принцип работы сцепления с гидравлическим приводом
Здесь, в отличие от первого случая, усилие от педали к механизму передается посредством жидкости. Последняя содержится в специальных трубопроводах и цилиндрах. Устройство данного типа сцепления несколько отличается от механического. На шлицевом конце ведущего вала трансмиссии и стального кожуха, закрепленного к маховику, устанавливается 1 ведомый диск.
Внутри кожуха есть пружина с радиальным лепестком. Она служит выжимным рычагом. Управляющая педаль при этом подвешивается на оси к кронштейну кузова. К ней также прикреплен толкатель главного цилиндра на После того как происходит выключение узла и переключение передачи, пружина с радиальными лепестками возвращает педаль в исходное положение. Кстати, схема сцепления представлена на фото справа.
Но это еще не все. В конструкции узла присутствует как главный, так и По своей конструкции оба элемента очень схожи между собой. Оба состоят из корпуса, внутри которого присутствует поршень и специальный толкатель. Как только водитель нажимает педаль, задействуется Здесь при помощи толкателя поршень перемещается вперед, благодаря чему давление внутри увеличивается. Последующее его передвижение приводит к тому, что жидкость проникает в рабочий цилиндр через нагнетательный канал. Так вот, благодаря воздействию толкателя на вилку и происходит выключение узла. В то время, когда водитель начинает отпускать педаль, рабочая жидкость поступает обратно. Это действие приводит к включению сцепления. Данный процесс можно описать так. Сначала открывается обратный клапан, который сжимает пружину. Далее идет возврат жидкости из рабочего цилиндра в главный. Как только давление в нем становится меньше усилия нажатия пружины, клапан закрывается, а в системе образуется жидкости. Так происходит нивелирование всех зазоров, которые находятся в определенной части системы.
В чем отличие двух приводов?
Основное преимущество систем с механическим приводом заключается в простоте конструкции и неприхотливости в обслуживании. Однако в отличие от своих аналогов они имеют меньший коэффициент полезного действия.
Гидравлическое сцепление (фото его представлено ниже), благодаря высокой производительности, обеспечивает более плавное включение и выключение узлов.
Однако такой тип узлов гораздо сложнее по своей конструкции, из-за чего они менее надежны в работе, более прихотливы и затратны в обслуживании.
Требование к сцеплениям
Один из главных показателей данного узла - высокая способность к передаче усилий крутящего момента. Для оценки этого фактора используется такое понятие, как «величина коэффициента запаса сцепления».
Но, кроме основных показателей, которые касаются каждого узла машины, к данной системе предъявляется целый ряд других требований, среди которых следует отметить:
- Плавность включения. При эксплуатации автомобиля данный параметр обеспечивается квалифицированным управлением элементами. Однако некоторые детали конструкции предназначены для увеличения степени плавного включения узла сцепления даже при минимальной квалификации водителя.
- «Чистота» выключения. Данный параметр подразумевает полное выключение, при котором усилия крутящего момента на выходном валу соответствуют нулевому или близкому к нему значению.
- Надежная передача мощности от трансмиссии к двигателю при любых режимах работы и эксплуатации. Иногда при заниженном значении коэффициента запаса сцепление начинает пробуксовывать. Что приводит к повышенному его нагреву и износу деталей механизма. Чем выше данный коэффициент, тем больше масса и размеры узла. Чаще всего это значение составляет порядка 1.4-1.6 для легковых автомобилей и 1.6-2 для грузовиков и автобусов.
- Удобство управления. Данное требование является обобщенным для всех органов управления транспортного средства и конкретизируется в виде характеристики хода педали и степени усилий, требуемых для полного отключения сцепления. На данный момент в России действует ограничение в 150 и 250 Н для автомобилей с усилителями привода и без них соответственно. Сам ход педали зачастую не превышает отметки 16 сантиметров.
Заключение
Итак, мы рассмотрели устройство и принцип работы сцепления. Как видите, данный узел имеет большое значение для автомобиля. От его работоспособности зависит исправность всего транспортного средства. Поэтому не следует рвать сцепление, резко убирая ногу с педали при движении. Чтобы максимально сохранить детали узла, необходимо плавно отпускать педаль и не практиковать длительных выключений системы. Так вы обеспечите долгую и надежную работу всех ее элементов.
Дисциплина: Конструкция Автомобилей и тракторов
Тема_2: Трансмиссии автомобилей
Лекция_3: «Муфты сцепления»
Требования и классификация муфт сцепления
Механическая трансмиссия должна иметь возможность кратковременного разъединения от работающего двигателя. Это необходимо при остановках автомобиля и при переключении передач в механической ступенчатой коробке передач. Кроме того, при троганье автомобиля с места и переключении передач соединение вала двигателя и трансмиссии должно происходить плавно, без резких рывков. В связи с этим возникает необходимость в специальном устройстве, обеспечивающем постепенное нагружение двигателя. В качестве такого устройства обычно применяется управляемая муфта. Использование муфты сцепления необходимо для переключения передач т.к. если трансмиссия находится под нагрузкой крутящим моментом, переключение невозможно. Прежде чем переключить передачу, муфту сцепления необходимо выключить.
Сцеплением называется силовая муфта, в которой передача крутящего момента обеспечивается силами трения, гидродинамическими силами или электромагнитным полем. Такие муфты называются соответственно фрикционными, гидравлическими и электромагнитными.
При движении автомобиля сцепление во включенном состоянии передает крутящий момент от двигателя к коробке передач и предохраняет механизмы трансмиссии от динамических нагрузок, возникающих в трансмиссии. Такие нагрузки в трансмиссии возникают при резком торможении автомобиля, резком включении сцепления, неравномерной работе двигателя и резком снижении частоты вращения коленчатого вала, а также при наезде колес автомобиля на неровности дороги и т.д.
На автомобилях применяются различные типы сцеплений, которые классифицируются по разным признакам (рис. 2.1). Все сцепления, кроме центробежных, являются постоянно замкнутыми, т.е. постоянно включенными и выключаемыми водителем при переключении передач, торможении и остановке автомобиля.
Наибольшее применение на автомобилях получили фрикционные сцепления - однодисковые и двухдисковые.
Рисунок 2.1 – Классификация муфт сцепления по различным признакам
Однодисковые сцепления применяются на легковых автомобилях, автобусах и грузовых автомобилях малой и средней грузоподъемности, а иногда и большой грузоподъемности.
Двухдисковые сцепления устанавливают на грузовых автомобилях большой грузоподъемности и автобусах большой вместимости.
Многодисковые сцепления используются очень редко - только на грузовых автомобилях большой грузоподъемности.
Гидравлические сцепления, или гидромуфты, в качестве отдельного механизма трансмиссии на современных автомобилях не применяются. Ранее они использовались совместно с последовательно установленным фрикционным сцеплением.
Электромагнитные сцепления широкого распространения не получили в связи со сложностью их конструкции.
При анализе и оценке конструкций сцеплений, как и других механизмов, следует руководствоваться предъявляемыми к ним требованиями:
· надежная передача крутящего момента от двигателя к трансмиссии;
· плавность и полнота включения; чистота выключения;
· минимальный момент инерции ведомых элементов;
· хороший отвод теплоты от поверхностей трения;
· предохранение трансмиссии от динамических нагрузок;
· поддержание нажимного усилия в заданных пределах в процессе эксплуатации;
· минимальные затраты физических усилий на управление;
· хорошая уравновешенность.
Кроме того, к сцеплению, как и ко всем механизмам автомобиля, предъявляют такие общие требования: обеспечение минимальных размеров и массы, простота устройства и обслуживания, технологичность, ремонтопригодность, низкий уровень шума.
Надежная работа сцепления без перегрева и значительных износов особенно важна в тяжелых дорожных условиях движения автомобиля и при наличии прицепа и полуприцепа, когда имеют место более частые включения и выключения, а также буксование сцепления.
Сцепление при надежной работе должно обеспечивать возможность передачи крутящего момента, превышающего крутящий момент двигателя. С изнашиванием фрикционных накладок ведомого диска усилие нажимных пружин ослабевает, и сцепление начинает буксовать. При этом длительное буксование сцепления приводит к его сильному нагреву и выходу из строя.
Сцепление должно включаться плавно, чтобы не вызывать повышенных нагрузок в механизмах трансмиссии и очень больших ускорений автомобиля, которые отрицательно влияют на водителя, пассажиров и перевозимые грузы. Так, например, при резком включении сцепления скручивающие нагрузки в трансмиссии могут быть в 3 - 4 раза больше максимального крутящего момента двигателя. Это происходит потому, что при быстром отпускании педали управления усилие сжатия ведущих и ведомых частей сцепления в начальный момент создается не только нажимными пружинами, но и кинетической энергией перемещающегося к маховику двигателя нажимного диска и связанных с ним деталей. При этом в момент соприкосновения ведущих и ведомых частей сцепления усилие их сжатия в несколько раз превышает силу нажимных пружин.
Плавность включения сцепления обеспечивается главным образом благодаря упругим свойствами ведомого диска, которые зависят от его конструкции. Плавности включения сцепления также способствуют пружины гасителя крутильных колебаний. Однако влияние этих пружин незначительно, так как их деформация при включении сцепления невелика. На плавность включения сцепления влияет и упругость деталей привода управления сцеплением. Так, например, в сцеплении с диафрагменной пружиной большую упругость имеют рычаги (лепестки) выключения сцепления, которые выполнены вместе с диафрагменной пружиной.
Наиболее высокую плавность включения обеспечивают многодисковые сцепления. Однако они применяются очень редко и только на тяжелых грузовых автомобилях.
Крутящий момент двигателя должен передаваться на трансмиссию без буксования сцепления.
Полнота включения сцепления достигается специальными регулировками сцепления и его привода. Эти регулировки обеспечивают необходимый зазор между выжимным подшипником муфты выключения сцепления и концами рычагов выключения, а также пропорциональный указанному зазору свободный ход педали сцепления, который обычно составляет 20...40 мм.
При значительном изнашивании трущихся поверхностей ведущих и ведомых частей сцепления указанный зазор уменьшается, и рычаги выключения упираются в выжимной подшипник муфты выключения, что препятствует созданию пружинами необходимого нажимного усилия.
Чистота выключения сцепления характеризует полное разъединение двигателя и трансмиссии, при котором ведущие детали сцепления не ведут за собой ведомые.
При неполном выключении сцепления затрудняется переключение передач (оно происходит с шумом), что приводит к изнашиванию шестерен и синхронизаторов. Если же сцепление выключено не полностью, а в коробке передач включена передача, то при работающем двигателе сцепление будет буксовать. Это приводит к нагреву деталей сцепления и изнашиванию фрикционных накладок ведомого диска.
Чистоте выключения сцепления препятствует трение в ступице ведомого диска, которая установлена на шлицах первичного вала коробки передач. При выключении сцепления ведомый диск находится под действием осевой силы, которая прижимает его к маховику. Значение осевой силы ограничивается силой трения в шлицевом соединении ступицы диска и первичного вала коробки передач.
В многодисковом сцеплении остаточная осевая сила подсчитывается последовательным суммированием сил трения, возникающих в шлицевых соединениях всех ведомых дисков.
Остаточная осевая сила в многодисковом сцеплении значительно больше, чем в однодисковом, вследствие этого требуемая чистота выключения многодискового сцепления не обеспечивается.
В однодисковых сцеплениях полное разъединение двигателя и трансмиссии обеспечивается соответствующим отводом нажимного диска от маховика. В двухдисковых сцеплениях принудительный отвод среднего ведущего диска осуществляется различными специальными устройствами (равноплечим рычагом, упорным стержнем и др.). Зазор между трущимися поверхностями при отводе нажимного диска в однодисковых сцеплениях составляет 0,75... 1,0 мм, в двухдисковых - 0,5...0,6 мм, а в многодисковых - 0,25...0,3 мм. При этом ход нажимного диска при выключении сцепления не превышает 1,5...2,0 мм для однодисковых сцеплений и 2,0...2,5 мм для двухдисковых сцеплений.
Минимальный момент инерции ведомых частей. Для уменьшения ударных нагрузок шестерен включаемых передач и работы трения в синхронизаторах при переключении передач в коробке передач момент инерции ведомых частей сцепления должен быть минимальным. При включении несинхронизованной передачи ударная нагрузка на зубья шестерен пропорциональна моменту инерции ведомых частей сцепления.
Ударный импульс при включенном сцеплении может быть в 50...200 раз больше, чем ударный импульс, возникающий при переключении передач с выключенным сцеплением.
Снижение момента инерции ведомых частей сцепления достигается уменьшением диаметра ведомого диска и массы фрикционных накладок. Так, диаметр ведомых дисков сцеплений автомобилей большой грузоподъемности обычно не превышает 400 мм . Толщина фрикционных накладок сцеплений составляет 3,3...4,7 мм. Однако это не всегда возможно, так как указанные размеры определяются крутящим моментом, передаваемым сцеплением. Кроме того, при уменьшении диаметра ведомого диска необходимо увеличивать число поверхностей трения, чтобы сцепление могло передавать крутящий момент. Но увеличение числа поверхностей трения при уменьшении диаметра ведомых дисков приводит не к уменьшению, а к значительному увеличению момента инерции ведомых частей сцепления. Так, например, момент инерции ведомых частей у двухдискового сцепления значительно больше, чем у однодискового, рассчитанного на передачу такого же крутящего момента.
Применение фрикционных накладок с повышенным коэффициентом трения (из спеченных материалов) позволяет уменьшить диаметр ведомого диска, но из-за увеличения массы фрикционных накладок момент инерции ведомых частей сцепления не снижается.
Таким образом, уменьшить момент инерции ведомых частей сцепления можно только за счет уменьшения массы ведомого диска. Поэтому ведомый диск выполняют из тонкого стального листа толщиной 2...3 мм.
До недавнего времени для фрикционных сцеплений применялись в основном фрикционные накладки, в состав которых входили асбест, наполнители и связующие материалы. В настоящее время все большее распространение получают фрикционные накладки без асбеста или с минимальным его содержанием. Это связано с тем, что асбестовая пыль признана опасной для здоровья человека. В современных механизмах сцепления применяются композитные материалы, обладающие улучшенными по сравнению с асбестом характеристиками. Но в случаях, когда требуется передать на узлы трансмиссии крутящий момент очень большой величины, фрикционные материалы оказываются непригодными. Поэтому в гоночных автомобилях и в сверхтяжелой технике (грузовиках, тягачах) применяют керамические фрикционные накладки. Они обладают очень высокой износостойкостью, нечувствительны к перегреву, но не обеспечивают плавной передачи крутящего момента на сцепление.
Стабильная и надежная работа сцепления существенно зависит от его теплового состояния. Поэтому необходимо поддерживать постоянный тепловой режим муфты сцепления .
При трогании автомобиля с места происходит буксование сцепления. Это приводит к нагреву деталей сцепления и выделению теплоты на поверхностях трения его ведущих и ведомых частей. Так, например, одно включение сцепления повышает температуру нажимного диска на 7... 15°С. Температура фрикционных накладок ведомого диска также повысится и понизится коэффициент их трения. При этом надежная работа сцепления будет нарушена, так как сцепление будет буксовать не только при трогании автомобиля с места, но и во время движения.
При длительном буксовании сцепления температура его поверхностей трения может превысить 300 °С, тогда как уже при 200 °С коэффициент трения снижается почти в два раза. Высокая температура приводит к вытеканию связующего компонента фрикционных накладок, они становятся сухими, пористыми и быстро изнашиваются.
При высокой температуре также может произойти коробление ведомого и нажимного дисков, появление трещин на нажимном диске и выход сцепления из строя.
Для предохранения сцепления от указанных негативных явлений осуществляют различные конструктивные мероприятия, способствующие хорошему отводу теплоты от трущихся поверхностей ведущих и ведомых частей. Примером могут служить вентиляционные отверстия с металлическими сетками в картере сцепления и большое количество отверстий в кожухе сцепления, сделанные для улучшения циркуляции воздуха; рычаги выключения сцепления, выполненные в форме лопастей вентилятора, охлаждающего сцепление; массивный нажимной диск в виде кольца, обеспечивающий лучший отвод теплоты от ведомого диска; канавки в фрикционных накладках для циркуляции воздуха. Кроме того, канавки в фрикционных накладках служат для удаления под действием центробежных сил продуктов износа, снижающих коэффициент трения. Они также способствуют чистоте выключения сцепления, устраняя присасывание (прилипание) фрикционных накладок к рабочим поверхностям маховика двигателя и нажимного диска.
К муфтам сцепления предъявляется так же ряд общих требований, касающихся массы, габаритов, ремонтопригодности, стоимости, динамических нагрузок и т.д. Благодаря удовлетворению большинства требований, наибольшее распространение получили фрикционные однодисковые и двухдисковые муфты сцепления.
В свою очередь фрикционные сухие муфты сцепления разделяются по ряду признаков:
· по способу действия неавтоматические и автоматические. В настоящее время обычно применяют неавтоматические сцепления. Автоматические сцепления установлены на некоторых моделях легковых зарубежных и отечественных автомобилей. Автоматическим может быть само сцепление (центробежное) по принципу его работы или система управления, обеспечивающая работу неавтоматического сцепления (обычно фрикционного или электромагнитного) по заданному алгоритму без вмешательства водителя.
· по числу ведомых дисков - на одно- и двухдисковые. Однодисковые сцепления используют на легковых и грузовых автомобилях малой и сред- ней грузоподъемности. Двухдисковые сцепления устанавливают на автомобилях большой грузоподъемности.
· по расположению нажимных пружин - на периферийные и центральные. По периферии устанавливают ряд цилиндрических пружин, а центрально - одну коническую, цилиндрическую или тарельчатую. Последние получили распространение в сцеплениях легковых автомобилей, остальные типы применяют в сцеплениях грузовых автомобилей и автобусов.
· по типу привода - на сцепления с механическим и гидравлическим приводом без усилителя и с усилителем. Усилители выполняют механическими, гидравлическими, пневматическими или вакуумными.
Конструкции фрикционных муфт сцеплений (рисунок 2.10)
Фрикционным сцеплением называется дисковая муфта, в которой крутящий момент передается за счет силы сухого трения. Поэтому такие сцепления называются также сухими.
На автомобилях широкое распространение получили однодисковые и двухдисковые фрикционные сцепления. Многодисковые фрикционные сцепления применяются очень редко на тяжелых грузовых автомобилях.
Однодисковое сухое сцепление. Однодисковым сцеплением называется фрикционная муфта, в которой для передачи крутящего момента применяется один ведомый диск.
Однодисковые сцепления просты по конструкции, дешевы в изготовлении, надежны в работе, обеспечивают хороший отвод теплоты от трущихся поверхностей, чистоту выключения и плавность включения. Они удобны в обслуживании при эксплуатации и ремонте.
Принципиальная схема однодискового фрикционного сцепления показана на рисунке 2.2.
Рисунок 2.2 – Принципиальная схема работы муфты сцепления.
а - включено; б - выключено; 1 - кожух; 2 - нажимной диск; 3 - маховик; 4 - ведомый диск; 5 - пластина; 6 - пружина; 7 - подшипник; 8 - педаль; 9 - вал; 10 - тяга; 11 - вилка; 12 - рычаг
Принцип работы.
Ведущими деталями являются маховик 3 двигателя, кожух 1 и нажимной диск 2, ведомыми - ведомый диск 4 , деталями включения - пружины 6 , деталями выключения - рычаги 12 и муфта с выжимным подшипником 7.
Кожух 1 прикреплен болтами к маховику. Нажимной диск 2 соединен с кожухом упругими пластинами 5, которые обеспечивают передачу крутящего момента от кожуха на нажимной диск и осевое перемещение нажимного диска при включении и выключении сцепления. Ведомый диск установлен на шлицах первичного (ведущего) вала 9 коробки передач.
При отпущенной педали 8 сцепление включено, так как ведомый диск 4 прижат к маховику 3 нажимным диском 2 усилием пружин 6. Сцепление передает крутящий момент от ведущих деталей к ведомым через поверхности трения ведомого диска с маховиком и нажимным диском. При нажатии на педаль 8 (рисунок 2.2, б) сцепление выключается, так как муфта с выжимным подшипником 7 перемещается к маховику, поворачивает рычаги 12 , которые отодвигают нажимной диск 2 от ведомого диска 4. В этом случае ведущие и ведомые детали сцепления разъединены и сцепление не передает крутящий момент.
Пружины.
В автомобильных сцеплениях применяют цилиндрические, конические и тарельчатые пружины. Их сравнительные характеристики показаны на рисунке 2.3. Цилиндрические пружины имеют линейную характеристику во всем рабочем диапазоне. Характеристика конической пружины до посадки витков также является линейной, затем по мере выключения витков из работы жесткость пружины увеличивается. Это является недостатком, так как обусловливает увеличение усилия при выключении сцепления и значительное снижение нажимного усилия при изнашивании фрикционных накладок. Наиболее благоприятна характеристика тарельчатой пружины, усилие которой в рабочем диапазоне изменяется незначительно при выключении сцепления и изнашивании фрикционных накладок.
Рисунок 2.3 – Характеристики пружин фрикционных муфт сцепления: а – коническая; б-цилиндрическая; в-диафрагменная.
Цилиндрические пружины в современных сцеплениях устанавливают по периферии, что обеспечивает равномерное сжатие трущихся поверхностей за счет симметричного расположения пружин относительно друг друга и отжимных рычагов. В зависимости от их числа нажимные пружины располагаются на одной или двух окружностях нажимного диска. Для центрирования пружин и уменьшения их деформации при действии центробежных сил применяют стаканы, бобышки или выступы на нажимном диске и кожухе сцепления.
Вместо периферийных пружин может устанавливаться центрально одна цилиндрическая пружина. При этом уменьшается диаметр сцепления, а его осевые размеры увеличиваются. Использование более сложной в изготовлении конической пружины, устанавливаемой центрально, позволяет уменьшить и осевые размеры сцепления. В таких сцеплениях усилие сжатия пружины регулируется при помощи прокладок.
Тарельчатые пружины благодаря своим достоинствам широко используются в автомобильных сцеплениях (особенно легковых автомобилей). Тарельчатая пружина (рисунок 2.5) имеет форму усеченного конуса и состоит из сплошного кольца с меридиально расположенными лепестками, выполняющими функции упругих отжимных рычагов. Возможны два варианта установки тарельчатой пружины. В первом варианте на нажимной диск пружина действует наружным краем сплошного кольца, во втором - внутренним. Первый вариант наиболее широко применяется в силу простоты механизма выключения сцепления. Во втором варианте упрощается конструкция механизма установки пружины, уменьшаются усилие выключения и напряжения в пружине. Однако в этом случае для выключения сцепления внутренние концы лепестков пружины необходимо перемещать в направлении от нажимного диска, что усложняет конструкцию механизма выключения.
При использовании тарельчатых пружин упрощается конструкция сцепления, уменьшаются его размеры, число деталей, обеспечивается плавное включение, равномерная нагрузка на нажимной диск, малое изменение нажимного усилия при изнашивании накладок.