Moderne motorer intern forbrænding består af et stort antal dele. Blandt dem kan du finde helt forskellige elementer, der har helt andre, men meget nyttige formål for motoren. Sådan en lille del som en pumpe-injektor er ingen undtagelse. I denne artikel vil vi analysere enheden, driftsprincippet og reparationen af pumpeinjektoren.
Design og princip for drift af pumpe-injektorer
Dysen er et metalrør med et specielt tværsnit designet til sprøjtning brændstofblanding. For første gang og den dag i dag bruges en sådan enhed på dieselmotorer, hvor så vigtige parametre som motoreffektivitet, lavt niveau dets støj og lave toksicitet udstødningsgasser.
Injektorpumpen er installeret over hver cylinder og har samme struktur. Det inkluderer normalt: et afspærringsstempel, et specielt stempel, en sprøjteanordningsnål, en kontrol- og kontrolventil og en sprøjteanordningsfjeder.
Stemplet er en del, der skaber et vist tryk inde i dysen. Pumping sker under den translationelle bevægelse af stemplet. For at gøre dette er der specielle knaster på knastakslen, som på bestemte tidspunkter virker på stemplet og bringer det i gang.
Kontrolventilen åbner sammen med stemplets bevægelse og tillader brændstof at strømme ind i forbrændingskammeret. Ventildesignet er valgt på en sådan måde, at dieselbrændstof leveres i forstøvet form. På denne måde brænder den mere effektivt og økonomisk. I henhold til deres driftsprincip kan kontrolventiler opdeles i elektromagnetisk og piezoelektrisk. Piezoelektriske ventiler er de mest effektive, da de virker hurtigt og forhindrer dannelsen af overskydende brændstof, såvel som dets sult i visse områder af indsprøjtningssystemet. Hovedelementet i enhver kontrolventil er dens nål, som er ansvarlig for systemets hastighed.
Forstøverfjederen er installeret for at sikre en stram nålepasning. Fjederkraften suppleres normalt af brændstoftryk skabt i brændstofpumpen højt tryk. For at gøre dette er et specielt låsestempel installeret på den modsatte side af fjederen, som presser på det under påvirkning af brændstof.
Styring af enhver pumpeinjektor leveres vha. ECU'en modtager forskellige aflæsninger fra alle sensorer, analyserer dem og, baseret på de modtagne data, åbner eller lukker injektorerne på bestemte tidspunkter.
Funktionsprincip:
- Præ-injektion. I dette øjeblik virker en speciel timing cam på stemplet og tvinger den til at bevæge sig nedad. Brændstof-luftblandingen kommer ind i injektorkanalerne, og kontraventilen lukker. Stemplet skaber et tryk på 13 mPa, og i dette øjeblik aktiveres dysereguleringsventilen, som fører blandingen under tryk ind i forbrændingskammeret. I sidste øjeblik åbner indløbsventilen, og en ny portion brændstof kommer ind i injektorkanalerne. Samtidig falder brændstoftrykket inde i elementet.
- Hovedindsprøjtning. På dette stadium går stemplet ned igen, reguleringsventilen lukker, men der skabes et tryk på 30 mPa i dysen. Denne gang tilføres brændstoffet under højt tryk, hvilket sikrer dets effektive kompression og forbrænding i arbejdskammeret. Hver efterfølgende kompressionsproces ledsages af en stigning i trykket inde i dysen. Den maksimale værdi er 220 mPa. Afslutningen af denne fase sker på nøjagtig samme måde som ved foreløbig brændstofindsprøjtning.
- Yderligere injektion. Den består i at rense alle elementer i injektoren for spor af sod og sod. Yderligere injektion udføres umiddelbart efter den vigtigste. Alle injektionshandlinger udføres på samme måde som under hovedstadiet. På en anden måde kaldes dette fænomen også for dobbelt brændstofindsprøjtning.
Video - Sådan bestemmes hvilken pumpeinjektor der ikke virker eller banker på
Sådan repareres en pumpe-injektor med dine egne hænder
Selvfølgelig vil udskiftning af en defekt injektor være meget mere korrekt. Men hvis vi tager højde for dagens priser på bildele, opstår tanken uundgåeligt: hvorfor ikke reparere den gamle, for den er billigere. Faktisk koster et injektorreparationssæt meget mindre end et nyt element, og det vil derfor være meget mere rentabelt.
Svigt af injektorer består normalt af deres tilstopning eller forringelse af tætningsegenskaberne af de indvendige gummipakninger. Samtidig begynder motoren at fungere ustabilt og udvikler ikke nominel effekt, og brændstofforbruget stiger mærkbart.
Når du vælger et reparationssæt, er det vigtigt at observere mærket og modellen. For at undgå fejl anbefaler vi at fjerne den gamle og tage den med til en autoreservebutik. Konsulenter vil udvælge det sæt, du skal bruge til reparationer. Hvis du installerer pakninger designet til en injektor af en anden model, vil injektoren sandsynligvis slet ikke fungere korrekt. Selvom de i de fleste tilfælde har absolut forskellige størrelser pakninger, hvilket vil gøre selve reparationen mere problematisk end den videre drift af et sådant element.
For at reparere den gamle injektor skal den fjernes. For at gøre dette skal du først lette trykket i brændstofsystemet. Dette er nødvendigt for ikke at blive snavset med brændstof og ikke få en kraftig stråle direkte i dit ansigt.
Herefter skrues metalfastgørelsen af røret til dysen af, og den drejes ud. Skil elementet ad og husk omhyggeligt placeringen og rækkefølgen af delene. Dette er nødvendigt for efterfølgende montering, så der ikke er sådan noget som udseendet af "ekstra" dele. Rengør nu metaldelene, hvis de er tilstoppede, udskift gummitætningerne og andre dele, der er i reparationssæt injektorer. Herefter samles delen igen i omvendt adskillelsesrækkefølge.
Skru injektoren i og tilslut den til brændstofsystemet. Da trykket er reduceret, er det nødvendigt at skrue det manuelle brændstofpumpehåndtag af og skabe tryk i systemet igen. Du bør pumpe, indtil håndtaget spænder. Skru den derefter på igen, og du kan begynde at starte motoren.
Video - Reparation af BOSCH enhedsinjektorer
Dette afslutter reparationen af pumpeinjektoren. Det skal erindres endnu en gang denne procedure Det er slet ikke kompliceret, og vigtigst af alt vil det kræve de mindste omkostninger af dig. Forlæng trods alt livet gammel injektor meget billigere end at installere en ny
Brugen af et sådant system gør det muligt at øge motorkraften, reducere brændstofomkostninger, toksicitet og støjniveauer.
I indsprøjtningssystemet af denne type En enkelt central enhed, pumpeinjektoren, er ansvarlig for forsyningen af brændstof og dets distribution. I dette tilfælde er hver cylinder udstyret med sin egen dyse.
Systemet drives af en knastaksel udstyret med specielle knaster, som virker gennem en vippearm på pumpeinjektoren, hvilket sikrer dens drift.
Hvordan fungerer pumpe-injektorsystemet?
Pumpe-injektorsystemet omfatter sådanne elementer som: et stempel, et afspærringsstempel, kontrol- og kontraventiler og en spraynål.
Stemplet er designet til at skabe arbejdstryk inde i dysen. I dette tilfælde er stemplets translationsbevægelse sikret af knastakselkammene, og returbevægelsen er tilvejebragt af en fjeder.
Kontrolventilens hovedfunktion er brændstofindsprøjtning, eller rettere indsprøjtningsstyring. I sådanne systemer kan der bruges to typer ventiler - elektromagnetiske og piezoelektriske.
En ventil baseret på et piezoelektrisk element er mere avanceret på grund af dens høje hastighed. Hovedelementet i kontrolventildesignet er dens nål.
Sprøjtefjederen er nødvendig for at sikre, at sprøjtenålen sidder sikkert i sædet. Fjederkraften suppleres med kraften fra brændstoftrykket, og alt dette gøres ved hjælp af et låsestempel installeret på den ene side af fjederen og kontraventil placeret på den modsatte side af fjederen.
Spraynålen giver direkte injektion dieselbrændstof ind i motorens forbrændingskammer.
Pumpeinjektorerne styres af motorens styreenhed, som, baseret på data modtaget fra sensorerne, styrer driften af pumpens injektorventil.
Hvordan fungerer et pumpeinjektorsystem?
Effektiv produktion og distribution af brændstofsamlinger i pumpe-injektorsystemet sker i tre trin - foreløbig, hoved- og yderligere brændstofindsprøjtning.
Præ-injektion
Forindsprøjtningstrinnet er designet til at sikre en jævn forbrænding af brændstofsamlingen under hovedindsprøjtningsfasen. Hovedindsprøjtningstrinnet sikrer til gengæld en uafbrudt forsyning af brændstofblandingen i alle driftstilstande af forbrændingsmotoren.
Så i den indledende fase af brændstofforsyningen fungerer pumpeinjektoren i henhold til følgende skema. Knastakselknasten overfører mekanisk kraft til vippearmen, som skubber stemplet ned.
Brændstofblandingen begynder at strømme gennem kanalerne placeret i injektorlegemet. Dernæst lukker ventilen og stopper midlertidigt brændstoftilførslen. Dette skaber et højt tryk på køretøjet, der når 13 MPa.
Ved dette trykniveau udfører nålen, der overvinder kraften, der udøves på den af fjederen, en foreløbig indsprøjtning af den brændbare blanding.
Afslutningen af brændstof-for-tilførselsfasen er åbningen af indløbsventilen. Brændstof kommer ind i linjen, og det falder samtidig driftstryk. På dette stadium kan en eller to indsprøjtninger af køretøjet udføres afhængigt af dieselmotorens driftstilstand.
Hovedindsprøjtning
Begyndelsen af hovedinjektionsstadiet ledsages af den efterfølgende sænkning af stemplet. Efter lukning af ventilen fortsætter køretøjets tryk med at stige og når 30 MPa. Ved dette tryk stiger nålen, og hovedbrændstofforsyningen sker.
Højt tryk giver betydelig kompression af brændstoffet, som et resultat af hvilket mere brændstof kommer ind i forbrændingskammeret. Det største volumen af den brændbare blanding tilføres ved det maksimalt mulige tryk på 220 MPa, hvilket opnår maksimal motoreffekt.
Afslutningen af hovedindsprøjtningstrinnet sker på samme måde som det foregående trin efter åbningen af indløbsventilen. Dette er ledsaget af et fald i brændstoftrykket og sænkning af sprøjtenålen.
Yderligere injektion
Den sidste fase er en ekstra injektion, som bruges til rengøring partikelfilter fra sod, sod og snavs. Yderligere brændstof tilføres, når stemplet sænkes i henhold til et skema svarende til hovedindsprøjtningen. På dette stadium udføres som regel to indsprøjtninger af dieselbrændstof.
Pumpeinjektorer består af tre undersystemer: brændstofforsyning lavt tryk, højtryksbrændstofforsyning, lufttilførsel og udstødningsgas
Lavtryksbrændstofforsyningsundersystemet er nødvendigt for at levere brændstof til højtrykspumpen og rense brændstoffet.
Højtryksbrændstofforsyningsundersystemet bruges til at skabe højtryksbrændstofindsprøjtning i forbrændingskammeret.
Luftforsynings- og udstødningsundersystemet omfatter anordninger til rensning af luften, der kommer ind i motorcylindrene, og rensning af udstødningsgasserne, efter at de er frigivet fra cylindrene.
Hovedkomponenterne i strømforsyningssystemet til en dieselmotor med pumpeinjektorer er vist i figuren:
Ris. Dieselmotor strømforsyningssystem med pumpeinjektorer:
1 - brændstoftank; 2 – brændstofledning til ekstra varmelegeme; 3 - brændstofkøler; 4 - brændstoftemperaturføler; 5 – grænseventil i afløbsrørledningen; 6 - drænrørledning; 7 - brændstoffordeler; 8 - højtryksrørledning; 9 - pumpedyse; 10 - brændstofpumpe; elleve - trykreduktionsventil i brændstofforsyningsrørledningen; 12 - kontraventil; 13 - brændstoffilter; 14 - lavtryksrørledning; 15 – brændstofpumpe
En elektrisk brændstofpumpe 15 placeret i tanken pumper brændstof til filteret. Kontraventilen 12 forhindrer brændstof i at dræne fra fordeleren 7 og lavtryksrørledningen 14 ind i tanken, efter at motoren er standset.
Brændstofforsyningspumpen 10 bruges til at tage brændstof fra filteret og tilføre det under højt tryk til pumpeinjektorerne. Trykreduktionsventilen 11 holder trykket af brændstoffet tilført til pumpeinjektorerne inden for 8,5 kgf/cm2. Grænseventil 5 holder brændstoftrykket i afløbsrørledningen på niveauet 1 kgf/cm2, takket være hvilket trykpulseringer i systemet reduceres. På grund af det høje indsprøjtningstryk i personbilers dieselbrændstofsystemer med enhedsinjektorer og nogle common rail-systemer opvarmes brændstoffet i en sådan grad, at det er umuligt at forhindre skader. brændstoftank og brændstofniveausensoren, skal den afkøles, før den returneres til tanken. Brændstoffet, der returneres fra injektorerne, passerer gennem køleren 3 og afgiver varme i kølekredsløbet. Brændstoftemperatursensor 4 genererer et signal sendt til motorstyreenheden.
Fra filteret tilføres brændstof til forsyningsledningen i topstykket. I forsyningsledningen strømmer brændstof langs brændstoffordelerens 7 indvendige vægge i retning af den første cylinder. Gennem huller i væggene tilføres brændstof til det ringformede hulrum mellem fordeleren og blokhovedets vægge.
Brændstoffet blandes med opvarmet brændstof, som presses ud fra pumpens injektorer og ind i forsyningsledningen. Takket være dette opnås den samme temperatur, og derfor tilføres den samme mængde brændstof til alle pumpeinjektorer, hvilket sikrer ensartet motordrift. Uden en fordeler ville brændstof strømme ujævnt til enhedsinjektorerne. Det opvarmede brændstof, presset fra pumpens injektorer ind i forsyningsledningen, ville blive drevet af det indkommende brændstof fra den fjerde cylinder mod den første cylinder. På grund af dette ville brændstoftemperaturen stige fra den fjerde cylinder til den første, og en anden mængde brændstof ville strømme til enhedsinjektorerne. Konsekvensen ville være ujævn motordrift og for høje temperaturer i det forreste cylinderområde.
nr. 14 Pumpeinjektor med piezoelektrisk styreventil
Pumpeinjektorindsprøjtningssystemet er moderne system brændstofindsprøjtning af dieselmotorer. I modsætning til indsprøjtningssystemet Jernbane i dette system er funktionerne til at skabe højtryk og brændstofindsprøjtning kombineret i en enhed - en pumpeinjektor. Selve pumpeinjektoren udgør indsprøjtningssystemet af samme navn.
Brugen af pumpeinjektorer giver dig mulighed for at øge motorkraften, reducere brændstofforbruget og emissionerne skadelige stoffer, samt støjniveau.
I systemet har hver motorcylinder sin egen injektor. Pumpeinjektoren drives af en knastaksel, som har tilsvarende knast. Kraften fra knasterne overføres gennem vippearmen direkte til pumpeinjektoren.
Injektorpumpen har følgende anordning: stempel; kontrol ventil; låsestempel; kontraventil; spraynål. http://systemsauto.ru/feeding/shema_nasos_forsunka.html
Stemplet bruges til at skabe brændstoftryk. Stemplets fremadgående bevægelse udføres på grund af drejningen af knastakselkammene, og returbevægelsen skyldes stempelfjederen.
Reguleringsventilen er designet til at styre brændstofindsprøjtning. Afhængigt af drevet skelnes der mellem følgende typer ventiler:
elektromagnetiske; piezoelektrisk.
Den piezoelektriske ventil har erstattet magnetventilen. Den piezoelektriske ventil har stor hastighed. Det vigtigste strukturelle element i ventilen er ventilnålen.
Dysefjederen sikrer, at dysenålen sidder på sædet.
Fjederkraften understøttes af brændstoftrykket, hvis det er nødvendigt. Denne funktion realiseres ved hjælp af et afspærringsstempel og en kontraventil. Spraynålen er designet til at give direkte injektion brændstof ind i forbrændingskammeret.
Pumpeinjektorerne styres af motorstyringssystemet. Motorstyringsenheden styrer pumpens injektorventil baseret på sensorsignaler.
Funktionsprincip for en pumpeinjektor
Udformningen af pumpeinjektoren sikrer optimal og effektiv dannelse af brændstof-luftblandingen. For at opnå dette har brændstofindsprøjtningsprocessen følgende faser:
præ-injektion; vigtigste injektion; yderligere injektion.
Foreløbig injektion udføres for at opnå en jævn forbrænding af blandingen under hovedinjektion. Hovedindsprøjtningen sikrer blandingsdannelse af høj kvalitet ved forskellige motordriftstilstande. Yderligere indsprøjtning udføres for at regenerere (rense ophobet sod) partikelfilteret.
Pumpeinjektoren fungerer som følger. Knastakslens knast bevæger stemplet ned gennem vippearmen. Brændstof strømmer gennem injektorkanalerne. Når ventilen lukker, afbrydes brændstoffet. Brændstoftrykket begynder at stige. Når trykket når 13 MPa, stiger dysenålen, der overvinder fjederens kraft, og der sker en foreløbig brændstofindsprøjtning. Forindsprøjtning af brændstof stopper, når ventilen åbner. Brændstof hældes i forsyningsledningen. Brændstoftrykket falder. Afhængigt af motorens driftstilstande kan der udføres en eller to foreløbige brændstofindsprøjtninger. Hovedindsprøjtningen foretages kl yderligere bevægelse stemplet ned. Ventilen lukker igen. Brændstoftrykket begynder at stige. Når trykket når 30 MPa, stiger dysenålen, der overvinder fjederkraften og brændstoftrykket, og den primære brændstofindsprøjtning sker. Jo højere tryk, jo mere brændstof komprimeres, og følgelig sprøjtes der mere ind i motorens forbrændingskammer. Ved et maksimalt tryk på 220 MPa indsprøjtes den største mængde brændstof, og derved sikres maksimal motoreffekt.
Hovedbrændstofindsprøjtningen slutter, når ventilen åbner. Samtidig falder brændstoftrykket, og dysenålen lukker.
Yderligere injektion udføres med yderligere nedadgående bevægelse af stemplet. Funktionsprincippet for pumpeinjektoren med yderligere indsprøjtning svarer til hovedindsprøjtningen. Typisk udføres yderligere to brændstofindsprøjtninger.
nr. 15 Gløderør
For at gøre det lettere at starte dieselmotorer i koldt vejr (fra +5 til –30°C), opvarmes luften i cylindrene ved hjælp af gløderør. I deres kerne er gløderør en af forvarmningsanordningerne.
Gløderøret har forskellige installationssteder afhængigt af dieselmotorens design: i hvirvelkammeret (motorer med separat forbrændingskammer); i forkammeret (motorer med et separat forbrændingskammer); i forbrændingskammeret (motorer med et udeleligt forbrændingskammer).
Strukturelt er et gløderør en elektrisk varmeanordning, der består af en glødetrådsspole placeret i en beskyttende skal. Der er to typer gløderør: med en metalspiral; keramisk.
Keramiske gløderør har høj temperatur glødelampe (op til 1350°C), kortere opvarmningstid end med en metalspiral (2 sek) og følgelig, bedste egenskaber kold start. De førende producenter af gløderør er virksomheder Bosch, NGK, Lucas. Gløderørene styres vha relæ eller separat elektronisk styreenhed. Disse enheder regulerer mængden af spænding, der tilføres tændrørene og giver derved det nødvendige drejningsmoment og glødetemperatur samt varigheden af opvarmningen.
Gløderør tænder under visse temperaturforhold under motorstart ( første position af nøglen i tændingslåsen), hvad det signalerer advarselslampe på instrumentpanelet. Når lampen slukker og opvarmningen er afsluttet, startes motoren ( anden position af tændingsnøglen). På moderne dieselmotorer giver gløderør, ud over foreløbig (før-start) glød, ekstra varme efter start af motoren. Yderligere opvarmning produceres for at reducere støj, når blandingen brændes på en kold motor, samt for at reducere skadelige emissioner til atmosfæren. Den ekstra opvarmningsfase varer ca. 3 minutter og slutter, når kølevæsken når en temperatur på 20-30°C.
nr. 16) Formål med trykblæsning, eksisterende systemer tryksætning, tryksætning med mekanisk drev!
Superladning er en stigning i mængden af frisk ladning af den brændbare blanding, der tilføres forbrændingsmotoren ved at øge indsugningstrykket. Superladning bruges normalt til at øge effekten (med 20-45%) uden at øge motorens vægt og dimensioner, samt til at kompensere for krafttabet i høje højder. Superladning med "kvalitetskontrol" kan bruges til at reducere toksiciteten og røgen af udstødningsgasser. Aggregat overladning udføres ved hjælp af en kompressor, turbolader eller en kombination. Det mest udbredte boost er en turbolader, som bruger udstødningsgas energi til at drive den.
Aggregeret overladning bruges på næsten alle typer transportdieselmotorer (marine, diesellokomotiver, traktorer). Boost på karburatormotorer begrænset af forekomsten af detonation. De største ulemper ved samlet overladning omfatter:
øget mekanisk og termisk belastning af motoren på grund af øget tryk og temperatur af gasser;
nedsat effektivitet;
komplikation af designet.
Ikke-samlet overladning inkluderer:
dynamisk (tidligere kaldet inerti, resonant, akustisk), hvor effekten opnås på grund af oscillerende fænomener i rørledninger;
høj hastighed, brugt på stempelmotorer flymotorer ved højere højder end beregnet og ved hastigheder over 500 km/t;
køling, opnået ved fordampning i den indkommende luft af brændstof eller en anden brændbar væske med lavt kogepunkt og høj fordampningsvarme.
Stadig mere udbredt i transportmotorer Forbrændingsmotoren får dynamisk tryk, som med mindre ændringer i rørledningernes design fører til en stigning i fyldningskoefficienten op til en lang række ændringer i motorhastigheden. En stigning under overladning giver dig mulighed for at booste dieselen med hensyn til energiindikatorer i tilfælde af en samtidig stigning i den cykliske brændstofforsyning eller forbedre de økonomiske indikatorer, mens du bibeholder strømindikatorerne (med samme cykliske brændstofforsyning). Dynamisk overladning øger holdbarheden af cylinder-stempel-dele på grund af lavere termiske forhold ved drift på magre blandinger.
Der er flere supercharge systemer. Først og fremmest omfatter disse den mest almindelige type - turboladning - overladning ved brug af udstødningsgasenergi (fig. a). Vi vil overveje denne type overladning mere detaljeret nedenfor.
Den anden mulighed for overladning er overladning fra en drev-superlader - den såkaldte SUPERCHARGER. På moderne motorer Denne ordning bruges sjældent på grund af kompleksiteten af supercharger-designet og dets manglende pålidelighed. Dens fordel sammenlignet med turboopladning er højere ladetryk ved lavere hastigheder, samt fraværet af det såkaldte "turbolag", dvs. karakteristisk "dip" af kraft, når gasspjældet åbnes skarpt. Dette bestemmer anvendelsesområdet for drivkompressoren - hovedsageligt på ikke særlig højhastighedsmotorer (FORD, GM), selvom i de sidste år Der har været en tendens til at bruge dem på højhastighedsmotorer (MERCEDES).
På dieselmotorer MAZDA biler der er installeret en COMPREX bølgetrykveksler, som giver boost på grund af samspillet mellem tryk- og sjældne bølger, der forplanter sig i den roterende rotors kanaler. Denne type superladning kan opnå højere boost end andre superladningssystemer, men er endnu ikke blevet udbredt på grund af designets kompleksitet.
nr. 17) turbolader, dens enhed og driftsprincip
Grundlaget for turboopladning
Grundlaget for motorens turboladesystem, og samtidig dets mest komplekse element, er turboladeren. Princippet for driften af en turbolader er, at den energi, der er tilbage i udstødningsgasserne, ikke går ud i atmosfæren, men går til at øge trykket og densiteten af luften, der kommer ind i motoren.
De gasser, som motoren udleder, kommer ind i turbinehuset gennem udstødningsmanifolden (varm snegl). Gassernes tryk og gassernes termiske energi roterer turbinehjulet (varmt pumpehjul), som igen roterer kompressorhjulet (koldt pumpehjul). Herefter frigives udstødningsgasserne til atmosfæren.
Når kompressorhjulet roterer, trækker det luft gennem luftfilteret. Kompressorhjulets blade accelererer og skubber luft ind i kompressorhuset (cold scroll), hvor luften komprimeres og indsugningsmanifold motor. Luften, der forlader kompressoren, har ikke kun højt blodtryk, men også temperaturen, som reducerer ladningstætheden, hvilket påvirker fyldningen og dermed motorkraften negativt. På mange turboladede motorer bruges derfor mellemkøling af den ladede luft (intercooler) for at øge luftdensiteten og dermed forbedre cylinderfyldningen. For at gøre dette, efter kompressoren, ledes luften ind i en speciel "luft-til-luft" radiator installeret ved siden af kølesystemets radiator.
nr. 18) elektronisk turbolade styrekreds
vakuum linje
motorstyringsenheden
boosttryk og indsugningslufttemperaturfølere
luftspjæld styreenhed
intercooler
udstødningsgas recirkulationsventil
boosttrykreguleringsventil
turbolader
indsugningsmanifold
vakuumdrev af ledeskovle
en udstødningsmanifold
A - luft
B - udstødningsgasser
nr. 19. TURBOLARGER MED TURBINE MED VARIABEL GEOMETRI (VGT).
VGT (Variable Geometry Turbine) er en specifik type turbolader, der fungerer ved at udnytte energien fra udstødningsgasstrømmen. Grafen nedenfor viser Sammenlignende egenskaber hastighedsegenskaber for køretøjer udstyret med en konventionel turbolader og en VGT turbolader. Maksimal hastighed: VGT giver dig mulighed for at øge maksimal hastighed med 4,1 pct.
Accelerationstid: Sammenlignet med en konventionel turbolader reducerer VGT-turboladeren accelerationstiden fra 0 km/t til 100 km/t med 15,1 %.
Acceleration accelerationstid: denne karakteristik viser køretøjets evner under pludselig acceleration (fra 60 km/t til 100 km/t) under kørsel. Jo mindre den er, jo bedre egenskaber.
DRIFTSPRINCIP
Operation kl lave omdrejninger motor
Når motoren kører ved lave hastigheder, er mængden af udstødningsgasser relativt lille, energien af deres flow er lille, og i en konventionel turbolader skabes der ingen væsentlig turboladereffekt, men i en VGT turbolader er det muligt at lede udstødningsgasserne igennem en smallere sektion af passagekanalen, på grund af hvilken hastigheden og energien af deres strømning øges betydeligt. Som følge heraf forbedrer VGT-systemet motorens ydeevne ved lave hastigheder.
Driftsprincip ved lave motorhastigheder
Dette design bruger princippet om et Venturi-rør, hvis essens er, at når luft strømmer gennem en indsnævret sektion (punkt "A"), øges strømningshastigheden, og trykket falder. Når borediameteren falder, vil strømningshastigheden stige proportionalt (se ligning).
Operation kl høj hastighed motor
Ved høje motorhastigheder er energien i udstødningsgasstrømmen ret høj og er i stand til at skabe den nødvendige kraft til at rotere turbinen. I dette tilfælde øges tværsnittet af passagekanalen, og hele strømmen af udstødningsgas skynder sig til turbinen, mens udstødningskanalens pumpemodstand falder. Motorydelseskarakteristika vil afhænge af indsugningsluftmængden.
VGT system kontrol
VGT-systemets styresignal genereres baseret på analysen af signalerne fra hastighedssensorerne krumtapaksel EN(CF), gaspedalposition, atmosfærisk tryk, ladetryk, kølevæsketemperatur, indsugningslufttemperatur og koblingsindkoblingssignal.
I dette tilfælde bestemmer ECU'en køretøjets køreforhold og det nødvendige ladetryk afhængigt af motorhastigheden og mængden af indsprøjtet brændstof. ECU'en udsteder derefter magnetventil tilsvarende signal med en frekvens på 3 00 Hz med de specificerede parametre. Dette system giver dig mulighed for at opretholde en effektiv motordrift ved enhver hastighed.
Det skal bemærkes, at ladetrykssensoren også er designet til at måle det faktiske lufttryk i indsugningsmanifolden og give feedback til ladetrykskontrolsystemet (via ECU). Denne feedback bidrager til præcis kontrol.
Forhold, der udelukker driften af VGT-systemet
1. Motorhastighed under 700 o/min
2. Kølevæsketemperaturen er faldet til 0°
3. Beskadigelse af enhver del af EGR-systemet
4. Beskadigelse af VTG-systemets aktuatorstang
5. Defekt ladetryksensor
6. Beskadigelse af luftstrømssensoren (MAF)
7. Skader på gasspjældet
8. Fejl i gaspedalens positionssensor
Hvis nogen af disse forhold er til stede, stopper ECU'en med at styre VTG-systemet.
nr. 20.Yderligere foranstaltninger til at reducere udstødningsgas toksicitet
For at reducere niveauet af emissioner til atmosfæren af giftige komponenter, der kommer ind i motorens udstødningsgasser som følge af fordampning og ufuldstændig forbrænding af brændstof, samt for at opretholde motorens effektivitet og reducere brændstofforbruget, moderne biler udstyret med en række af specielle systemer, som kan kombineres under det generelle navn motorstyring og udstødningsemissionskontrolsystemer. Lad os se på de mest almindelige systemer:
1. Brændstofdoseringskontrol.
Blandingens sammensætning styres af brændstofforsyningskontrolsystemer.
Med en luftoverskudskoefficient på λ=0,9 kører motoren med maksimal effekt og drejningsmoment.
Optimal effektivitet og minimale CO- og CH-emissioner opnås ved drift på blandinger med en koefficient på λ=1,1. Indholdet af nitrogenoxider i udstødningsgasserne viser sig dog at være maksimalt.
For at betjene motoren i tilstand tomgang blandingens sammensætning skal karakteriseres ved en koefficient λ=0,9 – 1,05.
Den tvungne tomgangstilstand (motorbremsning) giver dig mulighed for helt at lukke for brændstoftilførslen til cylindrene. Der vil ikke være udledning af giftige stoffer.
2. Recirkulation af udstødningsgas.
At lede en del af udstødningsgasserne tilbage i forbrændingskammeret (recirkulation) bruges til at reducere blandingens forbrændingstemperatur for at reducere dannelsen af nitrogenoxider og brændstofforbruget. Dette reducerer dog også motorkraften.
Udstødningsgas recirkulation ( EGR system) implementeres på to måder: 1) intern recirkulation tilvejebragt ved kontrol af ventiltiming, og primært ved ventiloverlapning; 2) ekstern recirkulation, hvor udstødningsgasser tages fra udstødningsmanifolden og sendes tilbage til forbrændingskammeret gennem ventilsystemet.
3. Motorens krumtaphusventilation.
Da toksiciteten af krumtaphusgasser er mange gange højere end udstødningsgasser, er deres frigivelse til atmosfæren forbudt. Når motoren kører, overføres krumtaphusgasser af krumtaphusventilationssystemet til motorens indsugningskanal, hvor de blandes med arbejdsgasser og under indsugningsslaget kommer ind i cylinderen til efterfølgende efterbrænding.
4. Termisk efterbrænding af udstødningsgasser.
Efterforbrænding af udstødningsgaskomponenter, der ikke brændes i motorcylinderen, sker i udstødningssystemet, hvor yderligere luft, der er nødvendig for efterbrændingsreaktionen, tilføres af en speciel kompressor.
Med udviklingen af katalytiske udstødningsgasrensningssystemer anvendes termisk efterbrænding ikke længere så udbredt som før.
5. Katalytisk efterforbrænding.
Efterbrænding af udstødningsgaskomponenter sker i en speciel enhed - en katalysator. Konverteren er monteret i udstødningssystemet og er placeret under bunden af bilen. I neutralisatorlegemet er der en keramisk blok, hvorpå en belægning af katalytisk materiale påføres (metaller - Pt, Rh, Rd).
Neutralisatorer af oxidativ type oxiderer CO og CH på grund af resterende ilt i magre blandinger eller ved at tilføre yderligere luft til systemet.
Neutralisatorer af reduktiv type reducerer NOx til harmløst nitrogen.
To-komponent neutralisatorer kombinerer neutralisatorer af oxidativ og reduktionstype.
Tre-komponent omformere (selektive katalysatorer) med en λ-sonde er langt det mest almindelige og effektive udstødningsgasrensningssystem. Iltsensoren (λ - sonde) i dette system bruges til at beregne forholdet mellem luft og brændstof i den brændbare blanding.
6. Systemer med feedback(λ – regulering).
Dette system sikrer neutralisering af op til 96 % af skadelige stoffer i udstødningsgasser. Systemet bruger to iltsensorer. En sensor er installeret før katalysatoren, den anden efter den. Sensorer, der måler mængden af fri oxygen i udstødningsgasserne, påvirker sammensætningen gennem brændstofforsyningskontrolsystemet luft-brændstof blanding ind i motorcylindrene. For at sikre tilstrækkelig rensning af udstødningsgasser af konverteren skal motoren køre i et snævert område af værdier λ = 1±0,005, kaldet "vinduet" katalysator.
nr. 21. Diagram over et system til trinløst variabel ventiltiming med en hydraulisk styret kobling. Justerbar ventiltiming.
Det variable ventiltimingssystem (fælles internationalt navn Variable Valve Timing, VVT) er designet til at regulere driftsparametrene for gasfordelingsmekanismen afhængigt af motorens driftstilstande. Brugen af dette system giver øget motorkraft og drejningsmoment, brændstofeffektivitet og reducerede skadelige emissioner.
De justerbare driftsparametre for gasfordelingsmekanismen inkluderer:
Øjeblikket for åbning (lukning) af ventilerne;
Varighed af ventilåbning;
Ventil løftehøjde.
Tilsammen udgør disse parametre ventiltimingen - varigheden af indsugnings- og udstødningsslag, udtrykt ved krumtapakslens rotationsvinkel i forhold til de "døde" punkter. Ventiltidspunktet bestemmes af formen af knastakselkammen, der virker på ventilen.
Forskellige motordriftstilstande kræver forskellige ventiltidsværdier. Ved lave motorhastigheder bør ventiltimingen derfor have en minimumsvarighed ("smalle" faser). Ved høje hastigheder skal ventiltimingen tværtimod være så bred som muligt og samtidig sikre overlapning af indsugnings- og udstødningsslag (naturlig udstødningsgas recirkulation).
Knastakselkammen har en bestemt form og kan ikke samtidig give smal og bred ventiltiming. I praksis er knastformen et kompromis mellem højt drejningsmoment ved lave omdrejninger og høj effekt ved høj krumtapakselhastighed. Denne modsigelse er præcist løst af det variable ventiltimingssystem.
Afhængigt af de justerbare driftsparametre for gasfordelingsmekanismen skelnes følgende metoder til variabel ventiltiming:
knastaksel rotation;
brugen af knaster med forskellige profiler;
ændring af ventilløftehøjde.
De mest almindelige er variable ventiltidssystemer, der bruger en knastakselrotation:
VANOS (Dobbelt VANOS) fra BMW;
VVT-i (Dual VVT-i), Variabel ventiltiming med intelligens fra Toyota;
VVT, variabel ventiltiming fra Volkswagen;
VTC, Variable Timing Control fra Honda;
CVVT, Continuous Variable Valve Timing fra Hyundai, Kia, Volvo, General Motors;
VCP, Variable Cam Phases fra Renault.
Driftsprincippet for disse systemer er baseret på rotationen af knastakslen i rotationsretningen, hvilket opnår tidlig åbning af ventilerne i forhold til udgangspositionen.
Et variabelt ventiltimingssystem af denne type har følgende generel enhed:
Hydraulisk kobling;
Kontrolsystem.
En hydraulisk styret kobling (almindeligvis kaldet en faseskifter) roterer knastakslen direkte. Koblingen består af en rotor forbundet til knastaksel, og huset, som er knastakselens drivremskive. Mellem rotoren og huset er der hulrum, hvortil motorolie tilføres gennem kanaler. Fyldning af et eller andet hulrum med olie sikrer rotation af rotoren i forhold til huset og følgelig rotation af knastakslen i en vis vinkel.
I de fleste tilfælde er en hydraulisk styret kobling installeret på indsugningsknastakslen. For at udvide kontrolparametrene i visse designs er der installeret koblinger på indsugnings- og udstødningsknastakslerne.
Styresystemet sørger for automatisk regulering af den hydrauliske kobling. Strukturelt omfatter det inputsensorer, den elektroniske enhed styringer og aktuatorer. Styresystemet bruger Hall-sensorer, der evaluerer positionerne af knastakslerne, såvel som andre sensorer i motorstyringssystemet: krumtapakselhastighed, kølevæsketemperatur, luftflowmåler. Motorstyringsenheden modtager signaler fra sensorer og genererer kontrolhandlinger på aktuatoren - den elektrohydrauliske fordeler. Fordeleren er en elektromagnetisk ventil og sørger for olieforsyning til og fra den hydraulisk styrede kobling, afhængigt af motorens driftstilstande.
Det variable ventiltimingssystem fungerer typisk i følgende tilstande:
Tomgangshastighed (minimum krumtapakselhastighed);
Maksimalt drejningsmoment.
nr. 22. System til ændring af ventilløftehøjde
En repræsentant for det mekaniske drev er Valvetronic-systemet, der bruges på BMW biler, som styrer løft af indsugningsventilerne og måler arbejdsblandingen, der kommer ind i cylindrene, hvilket gør det muligt at øge motorens effektivitet uden tab af kraft, samtidig med at Euro-4-standarderne overholdes og indsprøjtningssystemet bibeholdes i indsugningsmanifolden. Ved at ændre ventilslaget til høj frekvens rotation af krumtapakslen opnås den bedste ventilation af cylinderen og påfyldning af luft-brændstofblandingen. Ved minimum motorhastighed er ventilslag minimal. Dette reducerer effekten af ventiloverlapning, hvilket resulterer i minimalt brændstofforbrug. Når krumtapakslens hastighed øges, øges ventilåbningen. Samtidig falder modstanden mod gasstrømme inde i cylinderen, hastigheden af udrensning og fyldning af cylinderen med luft-brændstofblandingen øges. Derudover øges inertieffekten. Luft-brændstofblandingen inde i cylinderen er lukket af ventiler ved meget højere tryk, dens tæthed er højere end ved den minimale krumtapakselhastighed. Takket være det variable ventilslag reduceres friktionstab sammenlignet med et konventionelt ventildrev, på grund af den lave modstand ved små ventilslag.
Diagram over BMW Valvetronic-motorindsugningsventilløftekontrolsystemet:
1 - løftestangsfjeder; 2 - elektrisk motor; 3 - snekkegearhjul; 4 – excentrisk kontrolaksel; 5 - knastaksel; 6 – håndtag med rullestøtte; 7 - vippearm; 8 – ventil.
Mellem knastakslen 5 og hvert par indsugningsventiler 8 er der et ekstra håndtag 6, som er monteret på akslen. Den elektriske motor 2 roterer gennem et snekkegear den excentriske styreaksel 4 i en bestemt vinkel elektronisk system ledelse. Ventilerne åbnes direkte af håndtag 6 med rullestøtter, når de virker på vippearmene, som hviler på ventilen på den ene side og på den hydrauliske pusher på den anden. Håndtagene 6 presses mod knastakselkammen ved hjælp af spiralfjedre 1. For at reducere friktionstab er nålerullelejer installeret på håndtagets akser med en rullestøtte og vippearmen. Ved drejning af excentrikken løber excentrikken ind i håndtaget 6 og drejer den til en bestemt vinkel. Ved at flytte den excentriske aksel øger eller formindsker elmotoren mellemarmens arm, hvorved indsugningsventilernes slaglængde forlænges eller forkortes i overensstemmelse med motorbelastningen. I betragtning af at den excentriske forskydning af skubberaksen har elektrisk drev, dette giver dig mulighed for at indstille rotationsvinklen ulineært og programmere den individuelt for hver motor.
Ændring af ventilløftehøjden kan foretages ved at ændre højden på knastakselkammen, der virker gennem vippearmen på ventilen. Denne løsning, kaldet VTEC-systemet, bruges af Honda. Forkortelsen VTEC står fuldt ud for: Variable Valve Timing and Lift Electronic Control. Omskiftermekanismen er installeret på vippeaksen. Dette system giver dig mulighed for at ændre ventilslaget afhængigt af krumtapakslens hastighed (høj eller lav), samt slukke for cylindrene fra drift. Knastaksel, foruden to knaster med lille højde 3, har i midten en knast med stor højde 6 til at drive hver cylinders ventiler med øget slaglængde og åbningsvarighed. En højhøj knast virker på en ekstra vippearm 7, som er understøttet af en speciel fjederanordning 9. Inde i knastakselaksen er der en kanal 2 til tilførsel af olie til låsestemplet, som består af to dele. Olie tilføres systemdelene gennem en kanal lavet inde i knastakslen. For at skabe det nødvendige tryk, en ekstra olie pumpe, drevet fra hovedolieledningen. Låsestemplet består af to stempler, der kan bevæge sig under olietryk og forbinde den ekstra vippearm 7 med hovedvippearmene 4. Samtidig virker kammen 6, som har en større højde end knasterne 3, på den ekstra vippearm 3. vippearm 7 forbundet med hovedvippearmene 4, hvilket åbner ventilerne i en større mængde og øger varigheden af tilførslen af luft-brændstofblandingen. Når olietilførslen stopper, vender låsestemplet tilbage til sin oprindelige tilstand under påvirkning af en fjeder, og den ekstra vippearm afbrydes fra de vigtigste.
nr. 23. Elektromekanisk ventildrev
Forbedret cylinderfyldning kan opnås uden at øge antallet af ventiler, forlænge indsugningsfasen og øge ventilløftet ved at bruge en elektromagnetisk ventilaktuator EVA (Electromagnetic Valve Actuator). Sådanne systemer udvikles i øjeblikket intensivt både i Europa og USA.
Magnetventilaktuatoren er en fjederbelastet ventil, der er placeret mellem to elektromagneter, der holder den i dens yderstillinger: lukket eller helt åben. En speciel sensor giver kontrolenheden information om ventilens aktuelle position. Dette er nødvendigt for at reducere dens hastighed til et minimum ved landing i sadlen.
Funktionsprincippet for systemet er vist i figuren. Som det fremgår af driftsdiagrammet for dette system, mangler ventilstyringssystemet fuldstændig en knastaksel med eget drev, som erstattes af elektromagneter for hver ventil.
Ris. Elektromekanisk ventildrev:
1 - ventilåbning elektromagnet; 2 - anker; 3 - ventillukkende elektromagnet; 4 – ventilfjeder
Magnetarmaturet danner en kombination med to fjedre til at åbne og lukke ventilen. Når der ikke tilføres elektrisk strøm til elektromagneterne, holder ventilen og magnetfjedrene ventilen i midterpositionen, svarende til halvdelen af ventilens slaglængde, mens den er halvt åben, hvilket gør, at motorens krumtapaksel let kan krummes under den indledende start. op på scenen. Når den ønskede omdrejningshastighed er nået, modtages et signal fra styreenheden, og den øverste åbningselektromagnet tilføres elektricitet, lukker ventilen. Brændstofindsprøjtning udføres samtidig.
№24. Hydraulisk drev ventiler
Ansøgning elektromagnetisk drev ventiler kræver meget elektricitet for at åbne dem, så tyske motorproducenter foreslår at åbne ventilerne ved hjælp af hydraulik og styre hydraulikken ved hjælp af elektricitet. I modsætning til andre typer ventilåbning eliminerer brugen af et elektrohydraulisk ventildrev behovet ikke kun for en knastaksel og drosselventil, men også for ventilfjedre. Ved brug af denne type ventiler, sammen med simpel åbning og lukning af ventiler og ventilslag, er det muligt at ændre ventiltimingen og deres drift uafhængigt for hver cylinder, hvorved brændstofforbruget og emissionen af giftige stoffer i udstødningsgasserne reduceres. og øget motorkraft.
Diagram over elektrohydraulisk ventildrev:
1 - højtrykspumpe; 2 – højtryksledning (50…200 kgf/cm2); 3 - højtrykskontrolventil; 4 – kontroltrykledning (5...20 kgf/cm2); 5 – blok af elektrohydraulisk ventilløft; 6 - ventilløfteregulator; 7 - magnetventil på lavtryksledningen; 8 – lavtryksledning (mindre end 5 kgf/cm2); 9 - ventil til gasfordelingsmekanismen; 10 – magnetventil på højtryksledningen; 11 - cylinder; 12 – stempel.
Funktionsprincippet for systemet er som følger. Højtrykspumpen skaber olietryk i systemet op til 200 kgf/cm2. Den elektromagnetiske trykreduktionsventil 3 regulerer trykket i højtryksledningen inden for 50...200 kgf/cm2 i henhold til et signal fra styreenheden, afhængig af krumtapakselhastighed, belastning, temperatur osv. Denne ventil regulerer det variable slag på ventilløftehøjden samtidigt for alle ventiler med det samme. Hvis der påføres spænding til magnetventilen 10, åbner den, og olie fra højtryksledningen kommer ind i cylinderen i toppen af stemplet. Magnetventilen på lavtryksledningen 7 er lukket på dette tidspunkt, da der ikke tilføres spænding til den. Stemplet, der virker på gasfordelingsmekanismens ventil, bevæger det nedad, så ventilen åbner. Afhængigt af motorens driftstilstand aktiveres ventilløfteregulatoren 6, hvilket ændrer landingshastigheden for alle ventiler samtidigt. En ændring i ventiltimingen opstår, når spændingsforsyningstiden til magnetventilen på højtryksledningen 10 ændres.
Når magnetventilen 10 er deaktiveret, kommer olie fra højtryksledningen ind i cylinderen fra bunden af stemplet. Stemplet, der virker på gasfordelingsmekanismens ventil, bevæger det opad, så ventilen lukker. Olie fra rummet over stemplet tilføres lavtryksledningen og returneres derefter til pumpen.
For at øge ventilåbningskraften og samtidig reducere energiforbruget med et stort ventilåbningsslag, anvendes stempler bestående af to dele. Med et gennemsnitstryk på omkring 100 kgf/cm2 og en relativt kort responstid er ventilens fulde slaglængde 1 mm, og landingshastigheden varierer fra 0,05 til 0,5 m/s.
Det elektrohydrauliske ventildrev er forbundet til motoroliecirkulationssystemet. Fælles for motorsmøresystemet er motorsumpen, en oliepumpe til tilførsel af olie til motorsmøresystemet og til højtrykspumpen til ventildrevet, et olierensningsfilter og en olieaftapningsledning fra topstykket. Til den brugte olie, det samme for fælles system smøremidler og ventildrev har høje kvalitetskrav til langtidsdrift og viskositetsegenskaber. Derfor skal der hældes olie af typen 0W40 i smøresystemet. For at overvåge viskositeten under motordrift er der tilvejebragt en speciel sensor, der sender et signal om tab af viskositet.
Elektrohydrauliske ventilløfteenheder kan installeres og monteres uafhængigt af hinanden. Den flade overflade af blokken, lavet med stor præcision, giver mulighed for den nødvendige hydrauliske tæthed af forbindelsen mellem blokken og motorhuset.
nr. 25. Systemer til ændring af kompressionsforholdet af brændstof-luftblandingen. Forskellige måder slukke for cylindrene.
En forbrændingsmotors kompressionsforhold er tæt forbundet med effektiviteten. I benzinmotorer er kompressionsforholdet begrænset til detonationsforbrændingsområdet. Disse begrænsninger er af særlig betydning for motordrift ved fuld belastning, mens det høje kompressionsforhold ved delbelastning ikke udgør en risiko for detonation. For at øge motoreffekten og forbedre effektiviteten er det ønskeligt at reducere kompressionsforholdet, men hvis kompressionsforholdet er lavt på tværs af alle motordriftsområder, vil dette føre til reduceret effekt og øget brændstofforbrug ved delbelastninger. I dette tilfælde er kompressionsforholdets værdier som regel valgt meget lavere end de værdier, hvor den mest økonomiske motorydelse opnås. Med bevidst forringelse af motorernes effektivitet er dette især udtalt, når der arbejdes med delvis belastning. I mellemtiden er et fald i fyldningen af cylindrene med den brændbare blanding, en stigning i den relative mængde af resterende gasser, et fald i temperaturen af dele osv. skabe muligheder for at øge kompressionsforholdet ved delbelastninger for at forbedre motorens effektivitet og øge dens effekt. For at løse denne afvejning udvikles varianter af motorer med variabelt kompressionsforhold En af de mest almindelige varianter af en motor med variabelt kompressionsforhold er vist på figuren.
Ved delvise belastninger indtager den yderligere plejlstang 4 den laveste position og hæver stempelslagområdet. Kompressionsforholdet er maksimalt. Ved høje belastninger hæver excentrikken på akslen 3 aksen af det øverste hoved af den ekstra plejlstang 4. Samtidig øges overstemplets frigang, og kompressionsforholdet falder.
Motorcylindrene og blokhovedet er lavet som en monoblok, det vil sige som en enkelt blok, og ikke separat som i konventionelle motorer. En separat blok består også af et krumtaphus og en plejlstang og stempelgruppe. Monoblokken kan bevæge sig i blokkens krumtaphus. Venstre side af monoblokken hviler på aksen 1 placeret i blokken, der fungerer som et hængsel; højre side kan hæves eller sænkes ved hjælp af en plejlstang 3 styret af en excentrisk aksel 4.
For at forsegle monoblokken og krumtaphuset, en korrugeret gummibetræk 2. Kompressionsforholdet ændres, når monoblokken vippes i forhold til krumtaphuset ved hjælp af et hydraulisk drev, mens stempelslaget forbliver uændret. Afvigelse af monoblokken fra lodret fører til en stigning i forbrændingskammerets volumen, hvilket forårsager et fald i kompressionsforholdet.
Når hældningsvinklen falder, øges kompressionsforholdet. Den maksimale afvigelse af monoblokken fra den lodrette akse er 4%.
Ved minimum krumtapakslens rotationshastighed og brændstoftilførsel nulstilling såvel som ved lave belastninger indtager monoblokken den laveste position, hvor volumenet af forbrændingskammeret er minimalt (kompressionsforhold - 14). Ladesystemet er slukket, og luft kommer direkte ind i motoren.
Under belastning, på grund af rotation af den excentriske aksel, afleder plejlstangen monoblokken til siden, og forbrændingskammerets volumen øges (kompressionsforhold - 8). I dette tilfælde forbinder koblingen superladeren, og luft begynder at strømme ind i motoren under overtryk. Det optimale kompressionsforhold beregnes af den elektroniske systemkontrolenhed under hensyntagen til krumtapakslens hastighed, belastningsniveau, brændstoftype og andre parametre.
På grund af behovet for hurtigt at reagere på ændringer i kompressionsforholdet i denne motor vi måtte opgive turboladeren til fordel for mekanisk overladning med mellemluftkøling med et maksimalt ladetryk på 2,8 kgf/cm2.
Brændstofforbruget for den udviklede motor er 30 % mindre end konventionel motor samme volumen, og indikatorerne for udstødningstoksicitet overholder gældende standarder.
De vigtigste metoder til at slukke for cylindrene: slukning af cylindrene ved at slukke for brændstoftilførslen, mens en variabel grad af drosling af tomgangscylindrene opretholdes (metode 1); at slukke for cylindrene ved at slukke for brændstoftilførslen, mens de tomgangscylindre samtidig kommunikerer direkte med atmosfæren eller med udstødningsrørledningen (metode 2); nedlukning af cylindrene ved at holde indsugnings- og udstødningsventilerne lukkede og standse gasudvekslingen i tomgangscylindre(metode 3).
nr. 26. Recirkulation af udstødningsgas i en dieselmotor.
Dieseludstødningsgasser indeholder en lille mængde skadelige stoffer, så tidligere var det ikke nødvendigt at installere specielle enheder. Men med tiden blev standarderne strengere. Og alt sammen takket være indholdet af sodpartikler og nitrogenoxid i udstødningen. Derfor begyndte systemer at blive brugt til dieselmotorer for at reducere udstødningstoksicitet, hvilket inkluderer recirkulation af dieseludstødningsgasser sammen med en konverter, der reducerer toksiciteten af udstødningsgasser ved at reducere nitrogenoxid og bruge den resulterende oxygen til at forbrænde kulilte sammen med uforbrændte kulbrinter. og sodfilter.
Partikelfilteret er et porøst filtermateriale bestående af siliciumcarbid. Hvis vi overvejer design fra tidligere år, rensede de periodisk filtrene fra akkumuleret sod med udstødningsgasser, hvis temperatur blev øget, hvilket berigede blandingen. Filteret blev renset af styreenhedens kommando efter 400.500 km. I dette tilfælde var der en kraftig stigning i udledningen af andre skadelige stoffer. Derfor arbejder moderne partikelfiltre sammen med en oxidativ neutralisator, ved hjælp af hvilken soden brændes af ved den laveste temperatur på cirka 250 grader celsius.
I den nye generation af filtre har princippet slet ikke ændret sig: fastholdelse og ødelæggelse. Hvordan opnås den nødvendige temperatur til forbrænding af sodpartikler? På den ene side er filteret placeret bag udstødningsmanifolden. På den anden side tænder controlleren for hver 300-500 km "multi-fase indsprøjtning", hvilket resulterer i en stigning i mængden af brændstof, der kommer ind i cylinderen. Det vigtigste er, at overfladen af filterelementet er dækket af et tyndt lag katalysator, hvilket gør det muligt yderligere at øge temperaturen af udstødningsgasserne til den nødvendige (560-600 grader Celsius).
Filterelementet er en keramisk mikroporøs svamp. Mellem dens kanaler er vægtykkelsen ikke mere end 0,4 mm, så filtreringsfladen er stor. Denne "svamp" er ofte lavet af ultrafine stålfiber belagt med en katalysator. På grund af den tætte pakning tilbageholdes op til 80 % af partiklerne i størrelse fra 20 til 100 nm.
Nye filtre begyndte at blive brugt til at styre motorens drift. Tryksensorer er installeret ved filterets indgang og udgang, og efter at der er modtaget et signal fra dem, aktiveres berigelsestilstanden. Når forskellen mellem aflæsningerne bliver væsentlig, vil computeren gøre det klart, at "svampen" er tilstoppet af sod. Afbrændingen styres ved hjælp af en temperatursensor.
Som eksempel er det værd at nævne moderne mekanisme diesel udstødningsgas recirkulation elektronisk system, der styrer dieselmotor EDS. Designet er repræsenteret af et multi-komponent udstødningssystem, som inkluderer 7 sensorer: 2 lambdasonder, 2 temperatur, 2 tryk, et sodniveau i udstødningen. Dette inkluderer også 3 renseelementer: en katalysator, en lagerkatalysator og et partikelfilter af lagertypen. Ved hjælp af sensorer installeret i udstødningssystemet blev processerne for blandingsdannelse og forbrænding optimeret. Mange motorsystemer, brændstof- og luftforsyning, recirkulation af udstødningsgas, elektronisk gasspjæld og turboopladning er blevet overført til at styre partikelfilteret. Takket være tryksensorer installeret ved ind- og udløb overvåges graden af forurening af partikelfilteret. Katalysatorernes ydelseskvalitet vurderes ud fra data fra lambdasonder installeret ved ind- og udløb. Driften af motorsystemet justeres ud fra aflæsningerne af lambdasonder, temperatursensorer og sodniveauet ved udløbet. Ved hjælp af en katalysator "forarbejdes" giftige stoffer til ikke-toksiske og lav-toksiske forbindelser (vand, nitrogen, kuldioxid), og ved hjælp af en lagerkatalysator sker der yderligere oprensning fra nitrogenoxid og sodpartikler .
nr. 27. Ekstra lufttilførselssystem.
Dette system pumper luft inden for 65 sekunder udstødningsventiler ved en motorkølevæsketemperatur mellem 15° og 35° C. Som følge heraf forlader iltberigede udstødningsgasser motoren, hvilket fremmer efterbrænding og lader katalysatoren varme op hurtigere. Driften af det sekundære lufttilførselssystem styres af Motronic ECU'en via det sekundære pumperelæ til den sekundære luftindsugningsventil og kombinationsventilen. Efter hver efterfølgende motorstart og indtil motortemperaturen når 85°C, tænder det ekstra lufttilførselssystem med en forsinkelse på 20 s og kører motoren i tomgang i 5 s, mens systemet overvåges af en selvdiagnoseanordning. Tilstanden af de ekstra lufttilførselssystemdele overvåges enten i den "endelige fejlrapport", eller hvis der opstår en defekt, vil den blive registreret i fejlskriveren. Ved adgang til fejloptagerens hukommelse (arbejdet udføres på en servicestation), diagnosticeres fejlen let og kan derefter rettes. For nogle positioner (se fig. 99) er følgende yderligere forklaringer givet: - ekstra luft pumpes ind i luftkanal 1 på topstykket;
Løfteøjet 4 er skruet til venstre for topstykket;
En ekstra lufttilførselsventil er skruet ind i klemmen 5;
Prop 7 sættes på indløbsventilen (sort);
Vakuumslangen 8 er forbundet mellem den øvre del af indsugningsmanifolden og brændstoffordelingsledningen;
Indløbsslange 9 kommer fra toppen luft filter. Dens forbindelse skal være tæt, uden at der kommer luft ind;
Stik 11 hører til luftpumpemotoren. Den er sort og har to stifter;
Holderen 12 holder luftpumpemotoren. Den er skruet ind i køleventilatorens luftindtag;
Slangeklemme 14 fastgør indløbsslangen;
Trykslangen 15 er fastgjort mellem pumpemotoren 10 og kombinationsventilen 17;
Holderen 16 fastgør kombinationsventilen til målepindens styrerør for at kontrollere olieniveauet;
Udskift altid O-ring 19.
Ris. 99. Elementer i det ekstra luftforsyningssystem: 1 - luftkanal i cylinderhovedet; 2 - bolt, 25 Nm; 3 - vakuumslange; 4 - løfteøje; 5 - holder; 6 - ekstra indløbsventil */**; 7 - stikblok; 8 - vakuumslange; 9 - indløbsslange; 10 - luftpumpemotor*; 11 - stikblok; 12 - holder; 13 - bolt, 10 Nm; 14 - slangeklemme; 15 - trykslange; 16 - holder; 17 - kombinationsventil; 18 - bolt, 15 Nm; 19 - O-ring
nr. 28. Brændstoftank ventilationssystem
De vigtigste indgangssignaler til motorstyringsenheden til regulering af brændstoftankens ventilationssystem er:
krumtapakslens hastighed
masseluftmængdemålersignal svarende til motorbelastning
motortemperatur
iltsensor signaler
signaler fra styreenheder drosselventiler
Brændstofdamp tilbageholdes i adsorber 3. Det er en beholder med tilsluttede rør, fyldt med et overfladeaktivt middel - adsorbent. Adsorbenter skal ud over høj absorptionskapacitet kendetegnes ved stabile egenskaber ved ændring af omgivelsestemperatur, effektiv desorption (frigivelse af akkumulerede dampe) og stabilitet under gentagne gentagelser af adsorption-desorptionscyklusser, immunitet over for atmosfærisk fugt, høj mekanisk abrasionsstyrke for at undgå abrasion. under køretøjets drift. Den bedst egnede adsorbent er aktivt kul AG-3, opnået fra kul og semi-koks. Efter behandling af inputsignalerne udsender motorstyreenheden en kommando om at åbne magnetventilen 4. Som følge heraf udledes brændstofdampene, der er akkumuleret i adsorberen, ind i motorens indsugningsrør 6 og brændes derefter i dens cylindre. I dette tilfælde ændres forholdet mellem brændstof og luft i blandingen kortvarigt. Denne ændring i blandingen registreres af oxygensensorer 10, baseret på de signaler, som styresystemet foretager den nødvendige korrektion af. Krumtaphusventilation. Krumtaphusventilationssystemet er designet til at reducere emissionen af skadelige stoffer fra motorens krumtaphus til atmosfæren. Når motoren kører, kan udstødningsgas lække fra forbrændingskamrene ind i krumtaphuset. Krumtaphuset indeholder også dampe fra olie, benzin og vand. Samlet kaldes de krumtaphusgasser. Ophobningen af krumtaphusgasser forringer egenskaberne og sammensætningen motorolie, ødelægger motorens metaldele.
Moderne motorer bruger et lukket type tvungen krumtaphusventilationssystem. Krumtaphus ventilationssystem forskellige producenter og på forskellige motorer kan have forskellige designs. Vi kan dog fremhæve følgende generelle strukturelle elementer af dette system:
olieudskiller;
krumtaphus ventilation ventil;
luftrør.
Ved hjælp af ventilation fjernes både benzindampe og udstødningsgasser fra motorens krumtaphus. Der er to typer krumtaphusventilation: lukket og åben. Hver har sine egne ulemper og fordele.
Åben ventilation
fungerer ikke i tomgang eller ved lav hastighed;
mætter motorrummet med udstødningsgasser og forurener miljø(hvilket er relevant, da du også er i umiddelbar nærhed af forureningskilden);
der er mulighed for, at omgivende ufiltreret luft vil blive suget ind, når motoren køler ned;
Strukturelt enklere (kun ét rør på skubbedækslet).
Lukket ventilation
øger tjæring af karburatoren (dette var dog vigtigt i 1960'erne, under hensyntagen til de olier, der var tilgængelige på det tidspunkt; dette er mindre kritisk, når man bruger moderne højkvalitets semisyntetisk motorolie);
mulige problemer med kondens;
ved høje hastigheder skabes for meget tryk i suget, og det menes, at olien, som har tendens til at oxidere fra atmosfærisk ilt, forkorter dens levetid;
mulige udbrud af brændstof-luftblandingen i karburatoren;
mere effektiv med hensyn til olieforbrug;
nr. 29. Kølesystem med elektronisk styret
Motorens driftsparametre er blandt andet væsentligt påvirket af optimal temperatur regime kølevæske. Øget kølevæsketemperatur ved delbelastning giver gunstige betingelser for motordrift, hvilket har en positiv effekt på brændstofforbrug og udstødningsemissioner. På grund af den lavere kølevæsketemperatur ved fuld belastning, øges motoreffekten på grund af afkøling af indsugningsluften og derved øge mængden af luft, der kommer ind i motoren. Brugen af et kølesystem med elektronisk temperaturstyring gør det muligt at regulere væsketemperaturen ved delvis motorbelastning fra 95 til 110°C og ved fuld belastning fra 85 til 95°C. Et elektronisk styret motorkølesystem optimerer kølevæsketemperaturen i henhold til motorens belastning. I henhold til optimeringsprogrammet, der er gemt i motorstyreenhedens hukommelse, er det påkrævede arbejdstemperatur motor. På denne måde tilpasses kølevæsketemperaturen til motorens belastning. De vigtigste kendetegnende komponenter i et elektronisk styret kølesystem fra et konventionelt er tilstedeværelsen af en kølevæskefordeler med en elektronisk termostat. I forbindelse med indførelse af elektronisk styring af kølesystemet modtager motorstyreenheden følgende: Yderligere Information:
termostat strømforsyning (udgangssignal)
kølevæsketemperatur ved kølerens udløb (indgangssignal)
Kølerventilatorstyring (2 udgangssignaler)
position af potentiometeret ved varmesystemregulatoren (indgangssignal)
Når kølevæsken opvarmes, bliver fyldstoffet 2 flydende og udvider sig, hvilket fører til stigningen af stiften 1. Når der ikke tilføres strøm til varmemodstanden, virker termostaten som en traditionel, men dens reaktionstemperatur øges og er 110 ° C (temperaturen af kølevæsken ved motorens udløb). I filleren er indbygget en varmemodstand 3. Når der tilføres strøm til den, opvarmer den filleren 2, som udvider sig, hvilket får stiften til at strække sig med en vis mængde "x" afhængig af graden af opvarmning af filleren. Ben 1 bevæger sig nu ikke kun under påvirkning af det opvarmede kølevæske, men også under påvirkning af opvarmning af modstanden, og graden af dens opvarmning bestemmes af motorstyringsenheden i overensstemmelse med kølevæsketemperaturoptimeringsprogrammet, der er indlejret i den. Afhængigt af arten af pulsen og den tid, den påføres, ændres graden af opvarmning af fyldstoffet.
Fordeleren er placeret i stedet for tilslutningsbeslag ved cylinderhovedet og er en anordning til at lede kølevæskestrømmen ind i en lille eller stor cirkel. Ved fuld motorbelastning kræves intensiv køling af kølevæsken. Termostaten i fordeleren modtager strøm, hvilket åbner vejen for væske fra radiatoren. Samtidig blokerer en lille ventilplade gennem en mekanisk forbindelse vejen til pumpen i en lille cirkel. Pumpen tilfører kølevæske, der kommer ud af topstykket, direkte til køleren. Den afkølede væske fra køleren kommer ind i den nederste del af motorblokken og suges derfra af pumpen. Kombineret kølevæskecirkulation er også mulig. Den ene del af væsken passerer gennem en lille cirkel, den anden gennem en stor cirkel.
Termostatstyring i et optimeret motorkølesystem (kølevæskebevægelse gennem lav eller stor cirkel) udføres i overensstemmelse med tredimensionelle afhængighedsgrafer optimal temperatur kølevæske fra en række faktorer, hvoraf de vigtigste er motorbelastning, krumtapakselhastighed, køretøjshastighed og indsugningslufttemperatur. Disse grafer bruges til at bestemme den nominelle kølevæsketemperatur.
nr. 30. Motorer, der kører på gasformigt brændstof. Et strømsystem, der fungerer efter princippet om karburering, installeret på benzinmotor med elektronisk indsprøjtningssystem.
EN) Gas motor- en forbrændingsmotor, der anvender flydende kulbrintegasser (propan-butan) eller naturgas (methan) som brændstof.
Forskellen fra benzinmotorer, der kører på denne cyklus, er et højere kompressionsforhold (ca. 17). Dette forklares ved, at de anvendte gasser har en højere oktantal end benzin.
Motorer er opdelt i:
speciel (eller modificeret) kun beregnet til drift på gas; benzin bruges i kort tid, når gasudstyret ikke fungerer, når det ikke er muligt at udføre reparationer på stedet;
universel, designet til langt arbejde både på gas og benzin.
I en bil er den flydende propan-butan-blanding placeret i sømløse stål (uden svejsede sømme) cylindre installeret på rammen, under gulvet i bussen eller i bagagerummet på en bil. Den flydende gas er i en cylinder under et tryk på 16 atmosfærer (cylinderen er designet til et maksimalt tryk på 25 atmosfærer).
Cylindre til komprimeret naturgas er placeret på rammen, under gulvet i bussens interiør eller på dens tag (komprimeret gas bruges ikke på personbiler - der er meget lidt plads til omfangsrige og tunge cylindre). Komprimeret metan er under tryk op til 150 atmosfærer. Flere cylindre er kombineret til en fælles linje, der er en fælles påfyldningsventil, hver cylinder har også sin egen ventil.
Gas fra den fælles linje kommer ind i fordamperen (varmeren) - varmeveksleren, inkluderet i systemet væskekøling, efter opvarmning af motoren opvarmes gassen (flydende gas fordamper) til en temperatur på ≈75 °C. Gassen passerer derefter gennem hovedfilteret.
Gassen kommer derefter ind i en to-trins gasreducer, hvor dens tryk reduceres til driftstryk.
Dernæst kommer gassen ind i blanderen (eller ind i karburatorblanderen eller ind i blandingsafstandsstykket under standardkarburatoren, bestemt af brændstofudstyrets design). Blandere er designet på samme måde som karburatorer, har en gas- og luftspjæld, et tomgangssystem og et operativsystem. fuld kraft og osv.
B) Systemet til flydende gas, der fungerer efter karbureringsprincippet, bruges både på benzinmotorer udstyret med en karburator og på motorer udstyret med et benzinindsprøjtningssystem. Et kraftsystem, der fungerer efter princippet om karburering, når det bruges på motorer med elektronisk indsprøjtning benzin, ud over hovedelementerne i et konventionelt indsprøjtningssystem, indeholder en modtager 2, en reduktions-fordamper 6, en servomotor til styring af gasstrømmen 7, en rørledning til tilførsel af gas til diffusoren.
Ris. LPG-kraftsystem baseret på karbureringsprincippet, installeret på en benzinmotor med elektronisk indsprøjtningssystem:
1 - ventilationsrør til gasmodtageren; 2 - modtager med flydende gas; 3 – gasmodtagerbeslag; 4 - påfyldningsventil; 5 - gasafspærringsventil; 6 - reduktions-fordamper; 7 - servomotor til at styre gasstrømmen; 8 – elektronisk styreenhed; 9 - omskifter til den anvendte type brændstof "gas-benzin"; 10 – diffuser-blander; 11 – lambdasonde; 12 - vakuumsensor; 13 - akkumulator batteri; 14 – tændingskontakt; 15 – stafet
Når man skifter til at bruge gas som brændstof, strømmer der gas fra beholder 2 til fordamperreduktionen, hvor gastrykket falder og fordamper. Afhængigt af de signaler, der modtages fra sensorerne, udsender styreenheden et bestemt signal til servomotoren 7, som bestemmer gasforbruget ved en bestemt motordriftstilstand. Gassen kommer ind i diffusoren gennem rørledningen, hvor den blandes med luft og passerer til indsugningsventilen og derefter ind i motorcylinderen. For at styre motordriften er der tilvejebragt separate styreenheder til motordrift på benzin og gas. Information udveksles mellem begge styreenheder.
nr. 31. Strømforsyningssystem til en motor, der kører på komprimeret naturgas.
Bilmotorer kan fungere på komprimeret og flydende gas. Layoutdiagram af strømforsyningssystemet ved drift på komprimeret gas: cylindervarmer - højtryksreduktion - lavtryksreducer blander-karburator. Strømforsyningssystem til motorer, der kører på komprimeret gas. Cylindrene, der indgår i systemet, er lavet af stål og er designet til et arbejdstryk på 19,6 MPa. Deres kapacitet er 50 l, vægt 93 kg. Ventiler bruges til at lukke ledninger, når motoren ikke kører. Gasvarmeren bruges til at forhindre eventuel frysning af fugt i gassen. Den er lavet i form af flere omgange af en højtryksgasrørledning på udstødningsmanifolden. En højtryksgasreducer (HPGR) bruges til at reducere gastrykket til 1,2 MPa. Gas fra cylinderen kommer ind i reduktionshulrummet gennem en tilslutningsfitting og et keramisk filter til ventilen. Gearkassens fjeder presser på ventilen ovenfra gennem skubberen og membranen. Når gastrykket i andre hulrum er mindre end det specificerede, sænker gearkassefjederen ventilen gennem skubberen og sender gas ind i hulrummet gennem det resulterende hul ind i det samme hulrum. Gassen passerer derefter gennem et ekstra filter. Når et givet tryk i hulrummet nås, afbalancerer dens kraft på membranen fjederen, og ventilen lukker gaspassagen. Udgangstrykket justeres ved hjælp af et håndtag med en skrue. Driften af gearkassen overvåges ved hjælp af en trykmåler, der modtager et signal fra en højtrykssensor og en signalanordning for et fald i udgangstrykket.
En lavtryksgasreducer (LPGR) reducerer trykket til den driftsværdi, der kræves for tilførsel til blanderen (0,085 - 0,08 MPa). TIL
En enhed, hvor en højtryksbrændstofpumpe er kombineret i et hus med en injektor, kaldes et pumpe-injektor forsyningssystem.
Opfindelsens historie
De fleste kilder hævder, at brugen af pumpeinjektorer i produktionsmotorer går tilbage til midten af 90'erne, men der er information, der giver os mulighed for at drage andre konklusioner.Siden Robert Boschs opfindelse af in-line har udviklingen af brændstofudstyr. fulgte vejen med at forbedre brændstofindsprøjtningspumper. I Robert Boschs skema bliver alle injektorer fodret af én fælles pumpe. Men i USA i 1938 byggede Detroit Diesel-selskabet, ejet af , verdens første produktionsdieselmotor med et pumpe-injektor-kraftsystem.Trykket i pumpe-injektorens brændstofforsyningssystem er så stærkt, at hvis der er en lækage, kan brændstofstrålen "skære" samtidigt gennem tøjet og huden på hånden
Samtidig arbejdede USSR aktivt på at skabe sit eget brændstofudstyr til lastbiler. Men efter et par stykker mislykkede forsøg, blev det besluttet at købe en licens til Detroit Diesel 3-71-serien, som havde bevist sig godt under test, og lancere sin produktion i Yaroslavl. , men processen blev først forsinket på grund af den finske og derefter den store patriotiske krig.Først i 1945 ankom de første maskiner og udstyr til produktionen til YAZ-fabrikken amerikanske motorer. I 1947, den første fire-cylindrede, totakts dieselmotorer YaAZ 204 med et strømforsyningssystem med pumpeinjektorer. Denne motor, såvel som en sekscylindret analog lavet på dens basis, blev produceret med nogle modifikationer indtil 1992. I 1994 producerede den sin første europæiske lastbil, FH12, med pumpeinjektorer. Efter svenskerne dukker et sådant strømsystem op på Scania og Iveco.
Under tryk ødelægger pumpeinjektorer ofte sæderne i dieselmotorblokken
I segmentet personbiler Volkswagen er førende inden for udvikling af motorer med pumpeinjektorer. Dieselmotorer med pumpeinjektorer dukkede op på biler fra dette firma i 1998.
Mekaniske pumpeinjektorer
Pumpeinjektoren består af brændstofpumpe højtryks- og sprøjtedel i ét hus. Indsprøjtningspumpen er placeret i den øvre del, sprøjten er i den nederste del. Pumpeinjektoren er normalt placeret under ventildæksel og det er ikke synligt udefra. Det særlige ved placeringen skyldes det faktum, at pumpen drives af yderligere knaster på pumpen.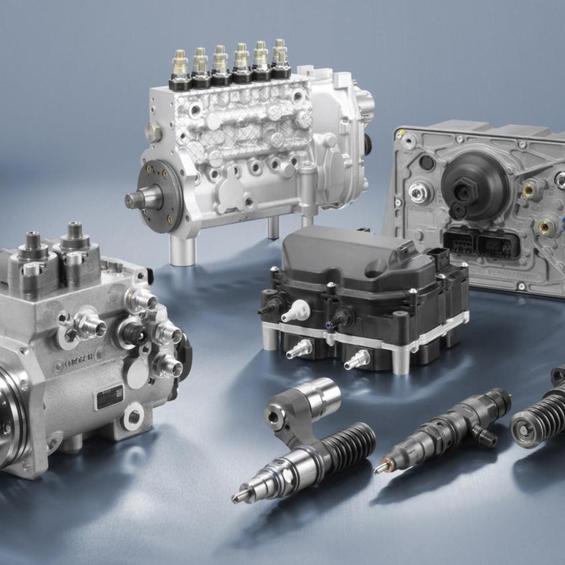
Elektroniske pumpeinjektorer
Moderne elektroniske pumpeinjektorer fungerer lidt anderledes. Trykket skabes på samme måde som i en mekanisk - ved hjælp af et stempel, men indsprøjtningsmomentet styres af den elektroniske motorstyringsenhed. Antallet af tilførte portioner brændstof kan nå op til ti pr. slag i tre hovedfaser. Den første er foreløbig indsprøjtning, når en lille portion brændstof tilføres cylinderen for at forvarme forbrændingskammeret og bedre antænde den anden hoveddel, der følger. Den tredje fase er beregnet til efterbrænding af uforbrændt brændsel og opvarmning (regenerering).Minimumsprisen for en pumpeinjektor til en VW Passat 2006 er 18 tusind rubler
For at sikre nøjagtig dosering af hver portion brændstof og give flere indsprøjtninger i et slag, bruges en elektromagnetisk ventil, der styrer hævningen af spraynålen.
Fordele og ulemper ved en pumpeinjektor
Pumpeinjektorer tillader, i modsætning til batteriindsprøjtning, brændstof indsprøjtes ved et tryk på mere end 2000 bar. Takket være dette forstøves brændstoffet mere effektivt, og derfor brænder det mere fuldstændigt. Derfor er motorer med pumpeinjektor kendetegnet ved høj specifik effekt, effektivitet og miljøvenlighed.Derudover er motorer med et sådant indsprøjtningssystem mere støjsvage end deres modstykker med Common Rail eller mekaniske indsprøjtningspumper. Derudover er indsprøjtningssystemet med pumpeinjektorer meget mere kompakt, men ulemperne ved dette system er ikke mindre alvorlige. Det vigtigste er de ekstreme krav fra pumpeinjektorer til brændstofkvalitet. Vand, snavs og surrogatbrændstof er dødeligt for dem.Den anden alvorlige ulempe er de høje omkostninger ved pumpeinjektoren. Det er vanskeligt at reparere denne præcisionsenhed uden for fabrikken. Derfor skal ejere af biler med et sådant strømsystem købe nye pumpeinjektorer.Drift og vedligeholdelse af pumpeinjektoren
De mest almindelige fejlfunktioner af enhedsinjektorer er forbundet med slid på ventilenheden og dyserne. Årsagen til svigtet af disse enheder er primært relateret til forkert brug bil med dette system.For at forlænge levetiden af enhedsinjektorerne skal du følge flere simple regler. For det første skal du kun tanke brændstof på gennemprøvede tankstationer.I slutningen af 90'erne optog motorer med pumpeinjektorer 20 % af det europæiske marked for dieselbrændstofudstyr
For det andet, tilsæt under ingen omstændigheder benzin, petroleum, bremsevæske og andre "KAMAZ"-tricks til at bringe sommerdieselbrændstof til vinterens frostbestandighed. For det tredje er det nødvendigt at reducere intervallet for udskiftning af brændstoffiltre. Desuden kan du installere dem, der er tilladt af producenten. Fordi analoger ofte ikke giver påkrævet niveau filtrering.