An important element of the design of any modern one is the fuel pump (TN), which supplies the required amount of fuel to the carburetor or to the injectors.
Electric fuel pump - general information about it
All HPs that are currently in operation are divided into:
- electrical;
- mechanical.
The electric unit is used in diesel engines, as well as in gasoline engines, which have a distributed fuel injection system.
In this case, the mechanism we are describing is necessary in order to supply (preliminary) gasoline to the high pressure fuel pump (high pressure pump). Mechanical pumps are not suitable for this because they are able to supply fuel exclusively at low pressure. But the electric booster fuel pump can generate pressure up to 0.7 MPa in systems with direct injection and up to 0.4 MPa for diesel engine.
Many less experienced motorists are wondering where the fuel pump is located. The answer is simple. This device is located either in the very fuel tankor in the fuel line. Experts consider the first type of layout to be more efficient and reasonable (the heat pump is built into the tank). It is believed that with such an arrangement, which does not require a special suction line, the risk of fuel loss is minimal. At the same time, the pump cools much better and faster, and its filter operates with one hundred percent efficiency.
If you look at the design of the fuel system of modern foreign cars, you can see that on many of them the fuel pump is indeed integrated into the tank. However, with the described arrangement, the injection fuel line becomes more prone to breakdowns and breakdowns due to its long length.
AT in general terms we figured out where the fuel pump is located on vehicles our days. Now let's look at the design of this unit. Such a device consists of two main components located in one metal housing - the pump itself and electric motor (drive). It also has additional elements - a fuel intake mechanism, a strainer, a fuel flow sensor, valves (reduction and intake).
All the components of the electric pump, including the filter, are constantly in contact with the fuel, but during the operation of the system, the probability of a short circuit in it is reduced to zero, since the electrical resistance of gasoline is at a high level (above 1MΩ). For maintaining in fuel system car of the required pressure value meets pressure reducing valve... And when the engine stops, the fuel system is locked (for this, it provides check valve).
Different types of electric pumps and their features
Structurally, an electric VT can be:
- centrifugal;
- gear;
- roller.
A centrifugal electric unit is usually mounted directly in the fuel tank. Relay fuel pump of this type activated by an "order" sent by the diesel control unit or gasoline engineand the electric pump starts to run. Note that the design of the described device has a special safety valve, which maintains the fuel pressure in rather narrow intervals.
Such a TN needs repair very rarely. An impeller, a working attachment equipped with a large number of blades, usually requires replacement. This component rotates in a chamber with a discharge and a suction channel. An increase in the pressure of a diesel (carburetor) engine in this case is formed when the said blades act on the turbulence of the fuel.
In roller HP, the suction of fuel and its injection is achieved by rotating the rotor, in which the rollers move. The gear pump of a diesel car (gasoline) works in a similar way. Only in it, the internal gears rotate around the stator. Roller and gear electric VT can only be mounted in the fuel line.
Features of a mechanical pump, its structure
This low pressure fuel pump is not suitable for a diesel engine. It is only used on carburetor machines. It is placed on the motor itself, the device consists of the following parts (repair of which, we note, is not so rare):
- body with top and bottom;
- cover covering the body;
- mesh;
- diaphragm (located between the body parts);
- mechanical drive (without it, the device cannot work, as you yourself know);
- stock;
- two valves (discharge and suction);
- spring put on the stem (returnable).
The drive, which is equipped with a mechanical low pressure fuel pump, is carried out from the camshaft (from its eccentric). And the most important element of the mechanism is the diaphragm, which is connected to the drive and the stem. On imported cars, the drive circuit is implemented, as a rule, with a rocker arm (with a special lever with two arms). Russian carmakers usually use a scheme that includes a lever with a balance bar and a pusher.
How to check the fuel pump?
Signs that the HP is not functioning properly are not as noticeable as drivers would like. But, nevertheless, they are available. The following are the main signs that are a signal that it makes sense to check the fuel pump of your gasoline or diesel engine:
- Difficulty starting the engine. Perhaps they are to blame for a malfunction of the fuel pump relay, starter, or maybe it's just a small battery charge. But, in any case, the reason will have to be identified. It is likely that it will tell you exactly about the malfunction of the fuel pump.
- the ignition is turned off;
- the high pressure fuel line is disconnected;
- turn on the ignition, provided that there is no fuel leakage;
- after that, the fuel pump relay is examined (in most cases, the subsequent removal and installation of the fuel pump is not necessary, since it is only necessary to replace its fuse).
- In cases where there is a voltage supply after replacing the fuse, the problem is most likely in a cable break (less often a full repair and replacement of the fuel pump is required) due to the fact that the device is out of order. If fuel does not enter the pipeline (distribution), there is a risk that the fuel line has been damaged or the fuel filter (fuel pump mesh) is clogged.
- the car does not start or often stalls;
- engine troit;
- extraneous noise in the engine;
- drop in engine power;
- lack of characteristic noise during the operation of the gas pump;
- Development of a mechanical inner rod;
- Worn gasket;
- Damage to the inner membrane;
- Failure of the delivery or suction valve.
- Wear of rollers or gears in volumetric hydraulic blowers;
- Impeller breakage in centrifugal blowers;
- Wear or burning of the lamellae of the electric motor collector;
- Wear of the plastic coupling that connects the electric motor shaft to the hydraulic blower.
Scheme for checking the performance of the VT and possible repairwhich may require a fuel pump cover remover:
Due to the need to pump gasoline through fuel lines, devices for cleaning it and feed it to the carburetor, which is usually located above the level of gasoline in the fuel tank, cars are equipped with fuel pumps.
On domestic cars from carburetor engines Mechanically driven diaphragm fuel pumps are used.
For two-stroke engines with crank-chamber blowing, diaphragm pumps are used, operating as a result of pressure pulsations in the crank chamber.
Electrically driven fuel pump
Special vehicles with gasoline injection equipment are equipped with electrically driven fuel pumps installed near the fuel tank or directly in the fuel tank (submersible pumps).
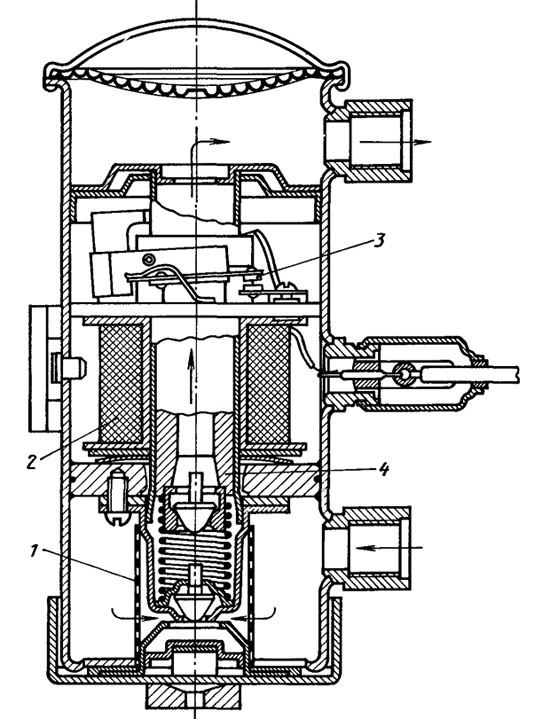
Working conditions automotive fuel pumps are characterized by an extremely wide range of changes in fuel supply from zero (on forced idling) up to the maximum value at full load and during filling of the float chamber after a long stay.
To avoid overfilling or draining the carburetor float chamber, the fuel pump should automatically change flow to exactly match the fuel consumption. To fulfill this requirement, the diaphragm actuator has a one-way rigid connection between the actuator mechanism and the stem membranes, serving only for the implementation of the suction stroke. The discharge stroke is carried out as a result of the action of a spring, the characteristic of which, taking into account the diaphragm diameter, is selected so that the supply pressure does not exceed certain limits.
The design of the fuel pump has lamellar discharge and suction valves.
On engines with a large cylinder displacement, fuel pumps with two or more parallel valves are often used to increase pump performance. To protect the valves from contamination, a sump and strainers are installed in the suction cavity of the pump, which retain large foreign particles.
Pumps with a mechanical drive have a manual priming lever. If the engine stops when the diaphragm is retracted to the bottom position, you must turn crankshaft about one turn with the starter or crank.
To prevent fuel from entering the crankcase if the membrane is damaged, a drain hole is made through which the fuel that has penetrated through the leaks is drained out without entering the crankcase. On fuel pumps of VAZ engines, as well as on pumps unified with them, available on parts engines MeMZ, ZMZ, UMZ, in addition to the two-layer main membrane, there is a second one located on the same rod. The drain hole is made in the gasket between the membranes.
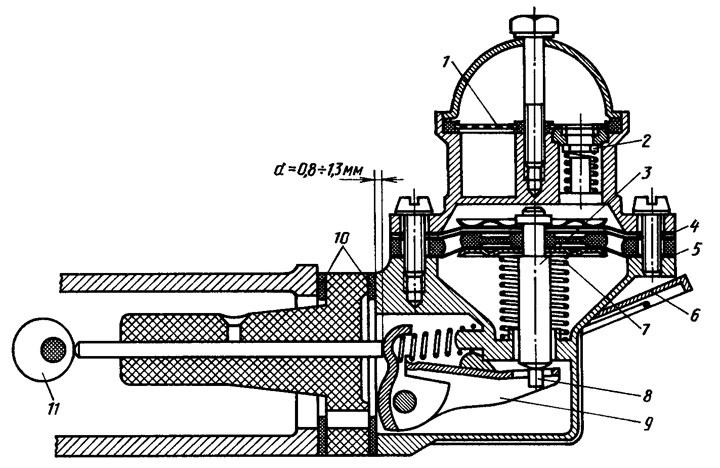
The principle of the fuel pump
The fuel pump works as follows. When filling float chamber all fuel entering the pump during the suction stroke is pushed out by the spring force through the discharge valves... During this period, both on the suction stroke and the discharge stroke, the stem head membranes does not break away from drive arm... As the fuel level in the float chamber rises, the flow area of \u200b\u200bthe shutoff valve decreases, causing increase in pressure in the pump discharge cavity... When the back pressure reaches a certain value, which, on average for most pumps, is 0.01 ... 0.025 MPa (0.10 ... 0.25 kg / cm2), the spring cannot fully straighten out during the discharge stroke due to resistance from the diaphragm. As a result, the stem head at the end of the discharge stroke and at the beginning of the suction stroke begins to detach from the drive lever, i.e., the working stroke of the diaphragm is automatically reduced. During this period, the pump develops greatest pressure fuel in the delivery cavity, which is often referred to in the reference literature as zero delivery pressure.
The control parameters when assessing its technical state of operation are the maximum performance in the absence of back pressure and a certain speed of rotation of the drive eccentric and the height of fuel suction by a dry pump.
An important issue is to ensure optimal operating conditions for the fuel pump on the car, excluding or reducing the possibility of vapor plugs.
Steam plug
Under steam plug means a sudden disruption of fuel supply, which externally manifests itself in the same way as when a fuel line is clogged. The essence of this phenomenon is as follows. Due to an increase in the temperature of the fuel in the pipeline before entering the pump, as well as an increase in vacuum due to partial clogging of filters and the fuel pipeline, gas bubbles may appear in the fuel flow, which are formed as a result of the evaporation of low-boiling fractions of gasoline. As a result the pump soon becomes completely filled with fuel vapor.
The described phenomenon is often aggravated by the deteriorated tightness of the valves, the effect of which on the operation of the pump is most pronounced when pumping fuel vapors.
When the pump is located in the lower part of the engine (VAZ engines of the first generation, GAZ, UMP) and, therefore, the minimum vacuum at the inlet, the requirements for its technical condition (mainly leaks in the channels) are not so high, as a result of which there are practically no cases of fuel supply disturbance in operation on these engines due to steam locks.
And vice versa, when the fuel pump is located in the upper part of the engine (ZIL, AZLK, VAZ-2108 engines and its modifications), in the case of increased temperature, valve leaks, leaks in the line from the tank to the pump, fuel supply disturbances occur much more often.
To exclude engine failure due to the occurrence of steam plugs, fuel pumps with a capacity 2.3 times higher than the maximum required are used.
To reduce overheating, visors are sometimes made to protect the fuel lines and the pump from overheating. Nowadays, a continuous fuel circulation system is used more often. A feature of such a system is the presence of a branch of the fuel line at the carburetor fuel intake fitting, which directs the excess fuel supplied by the pump through a nozzle (with a diameter of 0.7 ... 1.5 mm) back to fuel tank... When the fuel is circulated through the pump, even in such a most unfavorable operating mode for it, as driving at low speeds and at idle speed, constant cooling of the pipelines and pump parts is ensured by a flow of relatively cold fuel from the tank that is continuously pumped through them. If there is no circulation and in the hot season the car has stopped due to steam plugs, you need to cool the pump and the fuel line, for example, by putting a wet cloth on them.
The gas pump is critical node, which is responsible for supplying fuel to the system and maintaining the right pressure fuel. What happens when the gas pump breaks down, what are the signs of a malfunction of the gas pump and what you should pay attention to in such situations, this material will tell you about all this.
Two types of gas pumps
In old, still carbureted cars, as a rule, a mechanical gas pump was used, but gradually, it was replaced by an electric analogue. And today, cars with a mechanical gasoline pump are extremely rare.
The fuel pump is located in the fuel tank and its main task is to organize the supply of gasoline from the tank to the car's fuel system. Moreover, in many ways, it is this pump that is responsible for maintaining the required pressure, in many ways, but not in everything.
Symptoms of a malfunction of the fuel pump
Fuel pump for VAZ
Actually, these are more likely two stages of the same malfunction, although it happens that failures in the operation of the fuel pump do not lead to its complete failure. Especially when these failures are caused by some kind of extraneous factors. And so, the fuel pump either simply fails or does not work at all. This is all his breakdowns. Another thing is that there are many breakdowns of other elements, which in their symptoms are very similar to breakdowns of a gasoline pump.
As for the symptoms of a fuel pump malfunction, there can be a lot of them, and as already mentioned, they may coincide with the symptoms of malfunctions in other components and systems of the car. Therefore, we will describe only the most common and most characteristic of these symptoms.
The signs are very eloquent, but it is not always possible to understand what they are talking about. And here we cannot do without methods for diagnosing the fuel pump.
How to determine the malfunction of the fuel pump
Be that as it may, but most of the signs indicating a malfunction of the gas pump may indicate malfunctions in other systems and components of the machine. Troit the car - maybe candles, maybe ignition, maybe some kind of sensor is junk. Extraneous noise in the motor - in general, can be caused by various breakdowns. Even when the engine stalls immediately after starting, it will not work to sin only on the gas pump. For example, without the readings of the crankshaft position sensor, the ECU can stop the pump, which is quite a normal reaction of the car to such a problem. And even a decrease in pressure in the system can be caused by violations of the tightness of the fuel lines, breakdowns of the bypass valve and other failures.
What can you do right away? First of all, you can check the operation of the fuel pump before starting the engine. To do this, open the fuel tank cap and have someone turn on the ignition without starting the starter. In the first seconds after turning on the ignition, you should hear a specific noise from the fuel pump. If it is missing, most likely, the pump will have to be changed, although it is possible that the reason for the failure in the power supply of the device.
Measuring the pressure in the fuel rail is another way to check the fuel pump. Normal pressure readings, like correct procedure installation of a pressure gauge, you need to look in the documentation for your car.
Most often, in modern cars if the fuel pump fails, it is replaced. But there is no need to rush into this. Perhaps the cause of the failures is not the fuel pump itself, but for example, a coarse filter, which is simply clogged. In this case, banal cleansing of this mesh will help and you will not need to change anything. It is also worth checking the wiring, fuse, as well as the fuel pump relay, perhaps the reason for the failure of the device lies right here. Again, checking the fuel lines, the bypass valve, or even the injectors themselves, will also not be superfluous.
Fuel pump malfunction prevention
What should you pay attention to so that the gas pump runs as long as possible? First of all, this is the quality of the fuel and, of course, timely replacement fuel filter... If the gasoline you fill contains various impurities, this will most likely negatively affect the condition and service life of the fuel pump, and not only it. Therefore, it is not worth saving on the quality of fuel, since such savings then translate into very substantial spending on car repairs.
Monitor the fuel level in the tank. The fact is that the gasoline pump is cooled from the same gasoline that it pumps. Accordingly, if there is little fuel, or the pump is idling, it can overheat and therefore fail. Also knowledgeable people advise to clean the gas tank in due time and not to neglect this procedure. That is, perhaps, all the prevention of problems with the gas pump.
Video on the topic
› Say a word about the reserve fuel pump ...
Here is a thread that seemed interesting on one of the forums. the problem of choosing EBS (both the main and the backup) is on our face. EBS price monitoring showed that it is cheaper to take a suspended Bosch not from the Volga than the same one from the Volga ... Two times cheaper. Well, or take TSN-Citron, such as Russian products, probably of Chinese bottling, which does not inspire confidence.
Electric petrol pumps
For the normal functioning of the fuel injection systems, the gasoline pump must supply the required amount of fuel to the injectors and at the same time maintain its pressure sufficient for efficient injection in all engine operating modes. A conventional diaphragm-type gasoline pump from carburetor engines is not applicable in injection systems, since its performance and operating pressure several times less than required. In addition, such a pump is mechanically driven by the engine and begins to supply fuel only after the starter is turned on and the engine is started. At the same time in injection systems the working pressure in the fuel line of the injectors must be ensured immediately before starting the engine. These contradictions were avoided in a design where the pump is independent of the engine. It is driven by an electric motor direct currentpowered by the vehicle's electrical system - a 12-volt battery.
The electric petrol pump is designed as a whole in one body - a pumping unit was added to the electric motor. Now the entire electrical part is "bathed" in gasoline. It would seem that electric motors should “genetically” hate liquids in general and gasoline in particular. However, the armature (rotor), manifold and brushes of the electric fuel pump are constantly in the gasoline. The developers faced two obvious problems. The first is the "incompatibility" of the sparking collector and gasoline: it is clear to anyone that a spark threatens to explode. This problem resolved on its own. In liquids that do not conduct current (gasoline also belongs to them), sparking is impossible. In addition, it is not the gasoline itself that explodes, but a mixture of its vapors with air of a strictly defined composition. A spark that is too poor or too rich will not ignite. This made it possible to combine the pump and its drive in one housing.
By the way, there is another potential sparking device in the gas tank of every car - the fuel gauge. And yet, fuel tanks don't explode. The second problem is the low lubricating properties of gasoline, the viscosity of which at +200 C is half that of water. The gasoline pumped by the pump freely passes through the electric motor and simultaneously cools the entire unit. Such a constructive solution made it possible to abandon rolling bearings: they were replaced by plain bearings, for which gasoline serves as a lubricant. The low lubricity of this type of fuel was compensated by the high precision in the manufacture of the electric pump parts.
Typical designs
According to the principle of operation, electric petrol pumps are divided into volumetric and centrifugal. Differences in designs relate mainly to their pumping units.
The operation of positive displacement pumps is based on a cyclical change in the volumes of the suction and delivery cavities. For example, Bosch gasoline pumps have a roller hydraulic blower. It has a disc with five slots, each with a cylindrical roller. The disk is located on the same axis with the electric motor, but is offset (eccentric) with respect to the supercharger cage, inside which it rotates. The rollers act as movable seals between the rotor sections and the cage. When rotating, each section of the rotor, due to eccentricity, increases its volume in the fuel intake zone. A vacuum is created, which contributes to the suction of gasoline into the pump. Further rotation causes a decrease in volume (fuel injection zone), and gasoline is released through the outlet under pressure. A non-return valve in the pump outlet connection prevents the fuel from draining from the system after the ignition is turned off.
The principle of operation of positive displacement pumps from Pierburg is similar to roller pumps, only instead of a disc rotor, two gears are used in the supercharger - an external and an internal one.
Roller pumps are capable of developing maximum pressure up to 6-10 atm., gear - up to 4 atm.
Centrifugal pumps are divided into turbine and vortex pumps, and their pumping element is an impeller with blades of various configurations. If the blades are flat, we have a representative of turbine pumps. The maximum pressure developed by these pumps does not exceed 4 atm., And the efficiency is 10-15%, however, they differ in a stable flow and operate practically without pressure pulsations. They are usually used as the first stage of multistage pumping systems with distributed and central injection.
The vortex pump has an impeller with spherical recesses - this design of the blades, when rotating, creates additional vortices of the liquid. During one revolution of the impeller, the same amount of fuel is repeatedly thrown from the center to the periphery under the action of centrifugal force, as a result of which its kinetic energy is successively increased. Vortex pumps develop a pressure 4-9 times higher than turbine ones, and their efficiency is 30-45%. Such pumps are good for pumping not only gasoline, but also other low-viscosity, highly volatile liquids - alcohol, ether, etc. However, when pumping mixtures with abrasive inclusions, for example, low-quality gasoline, they quickly fail. Even a mesh filter at the inlet of the inlet pipe does not save from breakage.
EBN device
Parameters
The main characteristics of any gasoline pump are performance and developed pressure (there are others - power, efficiency, pump speed). For guaranteed pumping of gasoline through the filter fine cleaning the gas pump must provide a pressure 1.3-2 times greater than the required operating pressure in the injection system (2.5-5.5 atm.). The pump performance should significantly exceed the engine demand, even at modes maximum power and, depending on the engine size, be 1-2 l / min. Regardless of the engine operating mode, the fuel pump is constantly on. As a result, the electric motor of the pump consumes the same power from the car battery (about 60 W) and pumps gasoline at a constant speed. In fact, the fuel pump is "indifferent", the engine runs on idle or at maximum - in any case, the required fuel supply to the injectors is provided by the pressure regulator, and the excess gasoline is returned to the gas tank through the "return".
Dislocation
Electric petrol pumps can be installed both outside the gas tank and inside it. Accordingly, there are two types of them - external and internal. External fuel pumps, often called outboard pumps, are mounted under the bottom of the car on rubber "shock absorbers" and have a protective metal crankcase. This arrangement makes it easier to inspect the pump, diagnose it, and, if necessary, replace it.
The design of the internal, so-called submersible fuel pump, includes a fuel-reflecting chamber that ensures a constant fuel supply when the vehicle is moving in a straight line and in a corner, a fuel level sensor and the necessary electrical and hydraulic connections. The pump unit has a built-in pressure regulator and a coarse strainer installed at the inlet of the discharge section.
The pressure regulator dumps excess gas directly into the tank. This eliminates the need for a long pipeline - "return", stretching through the entire bottom of the car to the engine. In case of failure of the submersible fuel pump, it can only be removed outside by removing the gas tank, and this requires significant time costs.
The electric motor of a gasoline pump, subject to its high-quality manufacturing, rarely fails. First of all, the brushes wear out, then the collector, etc. Nevertheless, until these parts are completely worn out, the electric motor usually "nurses" 150-200 thousand km ... The situation is worse with the resource of the pump discharge section. And all because the "national" feature of our gasoline (in many cases) is the content of the smallest mechanical impurities in it, which perform the function of an abrasive. They also cause accelerated wear of the parts of the injection section. Therefore, the pump fails after a year and a half year of car operation on low-quality gasoline.
Operating principle:
A fuel pump is a component of a car's propulsion system that supplies fuel to the engine.
Electric fuel pumps supply fuel to the engine under pressure. On older car models, the fuel pump runs at a constant speed. In new car models, the speed of the fuel pump depends on the requirements of the engine.
The operation of the electric fuel pump is controlled electronic system the vehicle, which takes into account the throttle position, air-to-fuel ratio and emissions. Since electric fuel pumps work under pressure, they are quite noisy and quickly heat up. It is for this reason that they are placed in the fuel tank - the fuel cools the fuel pump and muffles the noise.
The petrol pumps are started by an electric motor. When the ignition switch is turned on, on-board computer gives a signal to start the fuel pump. An electric charge is supplied to the gas pump. The motor inside the fuel pump starts rotating within a few seconds and creates pressure in the fuel system.
If after two seconds the computer does not receive a signal that the engine is running, the petrol pump will automatically shut off for safety. It is in the first two seconds after starting the engine that you can hear the work of the gas pump.
Further, the fuel is sucked into the fuel pump through a tube and leaves the fuel pump through the one-way valve, enters the fuel filter, which retains dirt and debris and then goes to the engine. The fuel pump runs while the engine is running.
Attention! Before installing a submersible fuel pump, it is advisable to fill it with fuel,
since a dry hydraulic blower with a small amount of fuel may not pump it.
Diagnostics
Where do you need to start diagnostics, if there is a suspicion of a gasoline pump, and what parameters to check? An electric gas pump is characterized by a fairly large number of parameters, but in practice it is enough to control two main ones - pressure and performance. On already the removed fuel pump (at the stand) it is necessary to check the third parameter - the current consumption at rated and full load.
It is advisable to start by checking the supply voltage at the submersible fuel pump connector (in most cases it is available and located near the place where the fuel pump is installed in the gas tank) or at the terminals of the outboard fuel pump (in most cases it does not have a connector). In the case of the connector, you need to stab the wires going towards the fuel pump after the connector (without disconnecting the connector) and measure the voltage with a tester. If it is close to 12 volts (with the engine running, it can be even more) - normal, but if the noise of a running gas pump is still heard at the same time - very good, you can proceed to further checks. Here you should pay attention to a typical mistakeallowed when checking the power when measuring the voltage at the disconnected connector. So it is impossible to identify a defect in poor contact in the circuits in front of the connector (fuel pump relay, fuse, adapter pads) - on the disconnected connector, the voltage will always be about 12 volts, and under load on the fuel pump there may be only a few volts and it will not provide the required pressure and performance.
Next, we check the pressure in the fuel system, having previously released the pressure in it in any convenient way. For example, you can remove the fuse or the fuel pump connector and, after starting the engine, wait until it stalls. If there is a special fitting for measuring pressure on the fuel rail, we connect a pressure gauge there, if it is not there, then the pressure gauge through a tee is connected to the fuel supply line between the fuel filter and the frame with injectors. We turn on the ignition. The fuel pump, as a rule, works out in the fuel pumping mode for 1.5 ... 2 seconds. and turns off. During this time, a serviceable gasoline pump should provide pressure in the central injection system 0.8 ... 1.2 kgf / cm?, And in the distributed injection system 2.5 ... 3.5 kgf / cm? (depending on the type of injection system). If there is no fuel pumping mode, then the fuel pump must be turned on forcibly, for example, by removing the fuel pump relay and by bridging contacts 30 and 87.
A variant is possible when the pressure was too low, or the pressure build-up was very slow. Then there is a reason to think - who is to blame: a weak fuel pump, a dirty fuel filter or a pressure regulator? Turning off the ignition, we squeeze the return line with a clamp. Turn on the ignition again. If the pressure rises, the pressure regulator is to blame. An option is possible when the pressure was too high. Turning off the ignition, disconnect the return line and direct the supply end to a suitable container. We turn on the ignition and measure the pressure again. If the pressure has not changed, the pressure regulator is to blame, if it returns to normal, the return line is clogged. We restore the return line, start the engine and measure the pressure. In the central injection system, the pressure should not change (in relation to the pressure in the fuel pumping mode), and in the distributed injection system, it should decrease by about 0.5 kgf / cm? - by supplying a vacuum to the fuel pressure regulator. Press the pedal sharply throttle - should the pressure increase abruptly by 0.5 ... 0.6 kgf / cm? (in the central injection system, it does not change). We briefly squeeze the return line (if it is not available or a rigid fuel line, then the transition hose after the pressure gauge). The pressure should increase abruptly at least 2 times in comparison with the working pressure - this is the maximum pressure that the gas pump develops.
After clamping the return, it is necessary to carefully inspect all connections of the fuel system for fuel leaks. In this way, potentially unreliable connections can be identified and eliminated (fuel hoses in engine compartment under the influence of high temperature they age and the clamps fastening them weaken). An option is possible when the pressure does not increase, and the working pressure is close to normal. This means that no fuel flows through the return line, since the fuel pump pressure is below the opening threshold of the fuel pressure regulator. It is necessary to find out the reason: the gas pump may be to blame, or the supply voltage is low, or there is a fuel leak in the supply hose inside the gas tank.
An option is possible when the pressure rises very slowly. The reasons may be the same as above, but the main fuel filter may be heavily clogged, or low level fuel in the gas tank (the fuel pump periodically captures air and it is compressed in the fuel line). Now let's look at the behavior of the pressure gauge needle when the engine is idling. If the gauge needle swings strongly, then in most cases the reason is the dirty inlet mesh of the gasoline pump. It is very rare, but there are cases when the cause is a defect in the fuel pressure regulator. It is good if the gasoline pump is submersible and the preliminary removal of the gas tank is not required. Then we immediately remove the fuel pump and inspect the input grid.
If the fuel pump is not enclosed in a flask, then the grid is immediately visible.
If the mesh is synthetic and it is not overgrown with dirt, this does not mean that it is clean - it must be washed and blown out with compressed air.
If the fuel pump is in a flask, then you need to remember about the second grid inside the flask (for example, VW-GOLF, VW-PASSAT cars). The flask must be carefully and carefully disassembled and the inner mesh rinsed. Before installing the fuel pump back (through the hatch in the gas tank), inspect the internal volume of the anti-drain structure, where the fuel pump is immersed. Dirt and water must be pumped out, for example, using a gas pump from carburetor car... The situation is more complicated when the gas pump is suspended. This means that the inlet filter is, as it were, moved to the gas tank, to the intake pipe, and in many cases it is not available. To assess its condition, we clamp the hose between the gas tank and the gas pump with a clamp and disconnect the hose from the gas pump. We substitute a suitable container under the hose and begin to release the clamp.
If the pressure is large and the entire inner section of the hose is filled with fuel, the filter is in order. If the fuel flows out in a thin stream, the mesh is dirty. Air purging, like flushing the gas tank, is ineffective - it helps, but not for long. So if you do not take into account the replacement of the gas tank, then there is only one way - to make several punctures in the mesh with a flexible steel wire, and then install an external fuel filter in front of the gas pump. Now we start the engine and turn off the ignition, the engine has stopped, and the pressure in the fuel system should not drop.
If the pressure drops, then the reasons may be: fuel pump check valve, leaks in one or more injectors, pressure regulator. We start the engine again and turn off the ignition and immediately squeeze the fuel supply line in front of the pressure gauge. The pressure does not fall - the fuel pump check valve is to blame, if it falls - the injectors or the pressure regulator. We repeat the previous operation again and squeeze the return line.
If the pressure does not fall - the pressure regulator is to blame, if it falls - the nozzles. The consequences of these defects will be an increased start time of the engine, both cold and hot, and with leaking injectors, hot.
To measure the performance of the fuel pump, we disconnect the return line in a convenient place and direct the supply end into a measuring vessel. Now, in any convenient way, turn on the fuel pump for 1 minute (you can remove the fuel pump relay and short-circuit contacts 30 and 87, you can supply 12 volts to the fuel pump control connector (not available on all cars) or to the corresponding contact of the diagnostic connector). The fuel poured into a measuring vessel in 1 minute will be the capacity of the fuel pump in l / min. Depending on the injection system and the brand of the gasoline pump, the capacity will be in the range of 1.0 ... 2.2 l / min. If it differs from the passport data, then either the gas pump or the main fuel filter is to blame. Now you need to look, which is easier to remove: a filter or a gas pump for an autonomous test at the stand.
If, according to the results of the diagnostics, it became clear that the fuel pump needs to be changed, then what should be installed - new, used (from car dismantling) or restored? Since the decision is always made by the owner of the car, we will only express some considerations on this issue that may be useful in making a decision. It is certainly good to install a new fuel pump (if there is still confidence that it is branded). From the financial point of view, the option is the most expensive, but not directly related to the expected service life of the fuel pump. If he is unlucky, for the reasons stated above, then he will not work for a long time, and it is problematic to exchange it in the store. Installing a used fuel pump is the cheapest option from the financial point of view, but what kind of residual resource it has and how long it will work: a year, a month or one day - no one knows and does not give a guarantee. An option as a temporary measure is fine. Installing a restored fuel pump from the financial side is more expensive than the previous option, but about three times cheaper than the first option, plus a warranty from 6 to 24 months. It should be said briefly about the essence of the restoration of the fuel pump. If earlier the restoration consisted in the fact that out of two or three bad gasoline pumps one good was assembled, now in large industrial cities there are many specialized workshops and private entrepreneurs who, in the factory, make wear parts that are not inferior to branded counterparts and in their own gas pump body almost all new parts are installed. The fuel pump removed from the car can be given for restoration or immediately replaced with a similar one from the exchange fund. There may be options here. For example, instead of a gear hydraulic pump, a roller pump can be installed in a gasoline pump, which is more resistant to fuel with mechanical impurities. Therefore, a restored gasoline pump is a completely justified option, you just need to know where it can be done efficiently.
In conclusion, let's note what should not be done (or should not be done).
It is impossible to put a gas pump from the central injection system into the distributed injection system - such a gas pump will not provide the required performance and pressure. On the contrary, it is also undesirable, since at a higher performance of the fuel pump in the return line (due to hydrodynamic resistance), additional fuel pressure is created, which is added to the pressure set by the pressure regulator. As a result, the central injection nozzle will operate under more high pressure with next negative consequences (increased consumption fuel, difficult hot start of the engine, etc.)
What is desirable to do when installing a gas pump? Before installing the submersible fuel pump, it is advisable to fill it with fuel, because a dry hydraulic blower with a small amount of fuel may not pump it.
Gasoline pump It is a part of the propulsion system, the task of which is to supply gasoline to an automobile engine. This car unit is necessary in a car because the gas tank and engine are located at diagonally opposite ends of the car. Obsolete cars are not equipped with gasoline pumps, because in such cars, under the influence of gravitational forces, gasoline enters the engine, passing through the fuel hose, where a gasoline pump is not required.
Photo gallery:
Types of gas pumps
The current models are equipped with both mechanical and electrical fuel pumps. Mechanical pump found in carburetor machines, electric fuel pump - injection, where fuel enters car motor under pressure.
The mechanical gasoline pump is located outside the gas tank, but the electric one, on the contrary, is inside it. In everyday life there are cars with 2 gas pumps installed. The mechanical unit operates under low-frequency pressure due to the fact that the carburetor and the fuel pump are located at a close distance from each other.
Mechanical fuel pump installed on carburetor vehicles.
How does a gasoline pump work
The electric pump seems to push the supplied fuel into the engine. Fuel pump device in old car models such that their node work is at a fixed speed. New models are designed in such a way that the speed of the unit depends on the motor. The electric petrol pump depends directly on the electrical system of the machine, which takes into account such indicators as the aerial ratio to fuel, the position of the throttle, as well as the amount of contained exhaust.
Electric fuel pump installed on injection cars.
Such units begin to work from starting the electric motor. At the moment of turning the ignition switch, the on-board computer is triggered and a signal is given to start the fuel pump. When an electric charge is applied, the motor inside such a pump starts rotation, thereby creating pressure in the fuel system. In the absence of a signal about work engine overthan for a few seconds, the gas pump will be automatically turned off.
How does a gasoline pump work, heard during the first moments of the start car engine... Further, gasoline enters the gasoline pump through a tube and exits using a one-way valve, and then passes through the fuel filter to. While walking motor operation, the fuel pump will also work.
Gas pump problems
The fuel pump, by its nature, is considered an extremely important device, and its breakdowns are found on cars that are over ten years old or whose mileage exceeds two hundred thousand kilometers.
Most significant reasons fuel pump breakdowns: dirty fuel filter car and driving with an almost empty gas tank.
True, it happens that the unit fails before the end of its operational life. Main and most frequently encountered the reason for the breakdown of the fuel pump is such that the motorist drives almost empty petrol tank... As fuel passes through the unit, the parts of the gas tank are cooled and lubricated. In the event that there is not enough fuel, then the air flow is captured by the gas pump, and then the gas pump overheats and the rotating auto parts wear out. As a result, the entire node fails.
Another reason for the breakdown of the unit is untimely replacement in the car fuel filter, both coarse and fine.
When the coarse filter is dirty, then the unit receives resistance at the inlet, and at the outlet it receives clogging. fine filter... Thus, overheating of the fuel pump is observed with further failure.
Fuel pump malfunctions
Mechanical fuel pump:
Electric fuel pump:
Mostly a gas pump is a unit that cannot be restored, therefore, if it fails, it must be completely replaced. The original pump costs a lot for the reason that it is a unit high technology production. Of course, the price reflects the cost of high-quality materials in their manufacture, as well as the use of advanced technologies, because modern gas pumps must pump more than one ton of fuel during their operation, it is affected not only by various vibrations, but also by temperature fluctuations. Therefore, for the safety of the fuel pump, first of all, you need to monitor the filters.