ABS system - anti-lock braking system... An extremely useful option that prevents the wheels of the car from locking during emergency braking. Almost all car owners know this statement, but how this system works, how to behave when it is triggered in different situations and how to identify problems with the ABS, we will tell you in our review article.
Modern cars are equipped with a wide variety of systems and sensors. Some improve comfort, others improve environmental performance and much more. But passive and passive systems are especially useful. active safety... The ABS system is an active safety element, that is, it functions and benefits even before the accident.
For reference: systems passive safety - these are seat belts, airbags, safety glasses, crossbars in doors and much more. All these elements perform one or another role directly at the moment of a collision in an accident.
Anti-lock braking system is installed on most vehicles as additional option... There are models with standard ABS, that is, it is available on all trim levels. One of these, in the simplest configuration, it already has ABS + BAS (Anti-lock braking system with emergency brake booster).
ABS prevents the wheels from blocking during hard braking, and as a result, prevents the car from falling into a skid. With the correct functioning of the system, the car effectively brakes and remains fully controllable.
Why is it so important to eliminate blocking of even one wheel when braking? When sliding, the coefficient of friction is significantly lower than when at rest. When a wheel is blocked, it slides over the road surface - friction is reduced and braking is ineffective.
When the surface of the tire and the road are at rest, relative to each other, the coefficient of friction is maximally high and braking is efficient.
An experienced driver himself can feel the moment when the wheels are locked and slightly loosen the pressure on the brake pedal. In this case, the wheels begin to rotate again and grip road surface It gets better. But brake system the vehicle does not allow control of the braking force on each wheel.
The modern ABS system controls the rotation of each wheel and is able to increase or decrease the braking force on each wheel separately from the others. As soon as one wheel is locked, the system reduces the brake pressure on it, allows it to start spinning and again increases the braking force to improve braking. And so it happens with each wheel - effective intermittent braking is achieved while maintaining vehicle control.
ABS device
The anti-lock braking system is not a big deal. It consists of several main elements, which are partially integrated into the vehicle's standard braking system:
Wheel speed sensors that are mounted directly on the wheel hubs;
The system of control valves, it is with their help that the braking pressure on each individual wheel increases or decreases;
All signals from the sensors come to the electronic control unit, which analyzes them and sends the necessary signals to the valves of specific wheels.
Modern four-channel aBS systems are able to analyze the speed of rotation of the wheels 15-20 times per second and send the appropriate commands to prevent wheel blocking.
ABS performance
The main role of the ABS is to maintain control over the vehicle during emergency braking. If you brake smoothly, then the system does not participate in braking in any way, although it continues to constantly analyze the speed of rotation of the wheels.
During emergency braking "to the floor", the system revives and takes an active part in braking, adjusts the braking force and does not allow any wheel to lock. For the driver, the most important thing is that the car, with effective braking, remains fully controllable, that is, you can go around an obstacle, avoid a collision, or simply "refuel" the car into a turn at a higher speed.
The combination of effective braking and controllability is a major plus in terms of active vehicle safety.
Experienced drivers are able to simulate the operation of the ABS system, but the maximum that can be achieved is to weaken and increase the total braking pressure on all wheels at the same time. The very first single-channel ABS systems worked similarly - when one wheel was blocked, they weakened the braking pressure on all wheels. In modern ABS, one channel is responsible for one wheel, due to which the maximum efficiency of the system is achieved.
The system is especially useful for novice drivers who feel insecure while driving even in normal situations, and if emergency braking is necessary, they can quickly lock the wheels and lose control. ABS allows you to perform intuitive actions in emergency situations - to press the brake pedal "to the floor" and maneuver.
Depending on the type of road surface, the ABS system can be both an advantage and a disadvantage.
On loose surfaces (gravel, sand, snow) ABS increases the braking distance. This is explained by the fact that locked wheels on loose surfaces are buried in the surface, which has a good effect on braking efficiency. It is important to note that the car still loses controllability.
On slippery and hard surfaces (ice, dry and wet asphalt) ABS is much more effective.
The anti-lock braking system on some cars is turned off or with functions of adjusting to the type of road surface. In some cars, the driver himself indicates the type of coverage, in others the system determines automatically using special sensors.
The driver is informed about the activation of the ABS by a special indicator on the instrument panel, but in most cases it is not needed. And all because during the operation of the ABS, a quiet characteristic crackling is heard, and slight and frequent jolts are felt on the brake pedal.
Tasks performed by the ABS:
- Provides safe braking;
- Reduces braking distances on the most dangerous surfaces: slippery or wet road surfaces;
- Maintains control under heavy braking.
ABS video
Principle of operation modern system ABS is clearly shown in this video:
ABS malfunctions and how to fix them
ABS does not function
- Check for errors with ABS fault codes;
- We check the power lines of the electronic control unit;
- We check the power supply lines of the sensors and the sensors themselves for correct functioning (correct installation and connection, measure the speed sensor signal with a multimeter, check that there is no short circuit between the sensor terminals);
- We check the brake system for brake fluid leaks.
All these checks can be carried out independently, it is enough to have a multimeter, a device for reading errors on-board computer (if there is no regular one), and general idea about electrical circuits.
ABS works, but ineffective
- We carry out all checks, as with a completely inoperative system;
- Additionally, we check the supply voltage of the electronic unit aBS control, must match the voltage on-board network.
A disabled or non-functioning ABS system allows continued movement. But please note that all malfunctions standard system ABS must be taken into account by the driver when driving: more accurately assess the road surface, observe speed mode, keep a great distance from the vehicle in front, etc.
The electric valve of the hydromodulator does not work
- We use standard programs for checking the hydromodulator.
If all components are working well, then most likely it will be necessary to change the electronic-hydraulic unit.
CONTENT: Anti-lock braking system ABS. Principle of operation. Oddly enough, many accidents occur precisely because of the high efficiency of the brakes. On slippery roads - wet or ice-covered - emergency braking to quickly stop the car or drastically reduce its speed usually leads to the exact opposite result.
Anti-lock braking system ABS. Principle of operation.
Oddly enough, many accidents occur precisely because of the high efficiency of the brakes. On slippery roads - wet or ice-covered - emergency braking to quickly stop the car or drastically reduce its speed usually leads to the exact opposite result. The wheels are blocked and lose grip on the road surface, and the car does not slow down at all and, moreover, completely stops obeying the steering wheel.
An experienced driver in such cases will brake intermittently, adjusting the force on the brake pedal in such a way as to maintain maximum grip of the wheels and prevent the car from skidding. However, not all drivers have sufficient experience to accurately assess the situation, and very few have the endurance and the necessary skills to react to changing traffic conditions properly. Hence the accidents and the legitimate desire of engineers to put a "shepherd" on the brakes, absolutely impartial, capable of correcting the driver's mistakes and keeping him in control of the car in any driving conditions.ABS history
So, anti-lock braking systems owe their appearance to the work of designers to improve the active safety of the car. The first ABS variants were introduced back in the early 70s. They coped well with the assigned duties, but they were built on analogue processors, and therefore turned out to be expensive to manufacture and unreliable in operation. Further, the production of prototypes did not progress, although, in any case, it was certainly a step forward.
The ice was broken, and the next step of the designers was to replace the analog processor with more reliable and inexpensive digital electronic blocks based on integrated circuits. In 1978, the second generation ABS was released, and the first car to receive it (although not in basic configuration, and on order for an additional fee), became the Mercedes-Benz 450 SEL. And today it is already difficult to calculate both the number of ABS generations and the number of cars on which the anti-lock braking system is installed as standard.
General structure and principle of operation of ABS
The anti-lock braking system (see diagram ABS Mercedes W123) of three main elements: an electronic control unit (4), a hydraulic unit (3) and wheel speed sensors (1, 2). ABS is brought into working condition after turning on the ignition and reaching a certain speed of the vehicle.
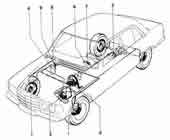
During braking, as soon as the sensor detects that the wheel begins to lock, the electronic unit, which processes signals from all sensors, sends a control impulse to the solenoid valves of the hydraulic unit (see the principle diagram of ABS operation). The hydraulic unit is installed in the brake line immediately after the brake master cylinder, and its valves control the fluid pressure in the brake circuits. If the braked wheel begins to slide, the valve body valves reduce or temporarily cut off the fluid supply to the working brake cylinder. This may not be enough to unlock the wheel, and then the solenoid valve will direct the brake fluid into the return line, thereby reducing the pressure in the working brake cylinder. When the wheel starts to rotate again, when it reaches a certain angular velocity, the ABS electronic unit removes its command, the valves open, and the hydraulic pressure is again transmitted to the brake mechanism. Wheel braking and release will occur periodically (this process is called modulation, and the valve body is sometimes called a brake pressure modulator), and the driver feels the ABS work with frequent sharp jolts on the brake pedal until the threat of blocking disappears or until the car comes to a complete stop.
When ABS is in operation, the deceleration efficiency of the car, in addition to the fact that the control does not get out of control of the driver, remains higher than when braking with skid. Tests have established that on slippery surface the braking distance of a car equipped with ABS can be 15% shorter than that of a conventional car. In addition, the mileage of the tire tread when using ABS increases by 5-7%.
And yet ABS is not a panacea
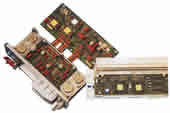
Another question is whether ABS can always reliably recognize a situation? I remember that World Off Road journalists simulated an unsuccessful entry to the hill during the tests of SUVs: loss of traction halfway up, pressing the brake pedal hard to keep the car on the slope, turning on reverse gear - and soft descent from the mountain using engine braking.
Everything was going fine until the turn came Ford explorerand then Mitsubishi pajeroequipped with ABS. The jeeps stubbornly rolled down the hill, despite the fact that the testers pressed the brake pedal all the way: the system perceived a slight downward slide on a loose slope and hard pressing on the brake at this moment as a command to unlock the wheels. As a result, both Ford and Mitsubishi could not stay on the slope without the use of the "handbrake". It is not hard to imagine what such a situation is fraught with in real life, if the slope is long enough, the collision happened closer to the top, the driver was confused (or does not act parking brake), and a car was already attached to the back. In a word, no matter how good ABS is in terms of improving the active safety of the car, the main thing is still the driver, who is obliged to critically reflect on the road situation and real opportunities his "iron friend".
ABS operation problems
Note that modern ABS has a fairly high reliability and can work for a long time without failing. ABS electronic units fail extremely rarely, since they are protected by special relays and fuses, and if such a malfunction does happen, then its cause is often associated with violations of the rules and recommendations, which we will mention below. The most vulnerable in the ABS scheme are wheel sensors located near the rotating parts of the hub or axle shafts.
The location of these sensors cannot be called safe: various pollution or even too big backlash in the hub bearings, they can cause malfunctions in the operation of the sensors, which are most often the culprits of malfunctions in the ABS operation.
In addition, the performance of the ABS is influenced by the voltage between the battery terminals. When the voltage drops to 10.5 V and below, ABS can generally turn off on its own through the safety electronic unit.
The safety relay can also trip in the event of unacceptable fluctuations and surges in the vehicle network. To prevent this from happening, here are the promised recommendations: it is impossible to disconnect the electrical connectors when the ignition is on and the engine is running, it is not advisable to start the engine by "lighting" from an external battery, or provide for this purpose as a "donor" own car and, in addition, it is necessary to strictly monitor the condition of the contact connections on the generator. What else? If the car requires repair using welding, then before starting work, disconnect the wiring from the ABS electronic control unit. In addition, it is not recommended to expose this unit to over 85 degrees Celsius for more than two hours. This is if the car is supposed to be painted and then hot dried in a special chamber.
The fact that ABS is faulty is indicated by the illumination of the warning lamp on the instrument panel. You should not react too nervously to this, the car will not remain without brakes, but when braking it will behave like a car in which ABS is absent.
If the ABS warning light comes on while driving, you must stop the car, turn off the engine and check the voltage between the battery terminals. If it turns out to be below 10.5 V, then you can continue driving, and charge the battery as soon as possible. If the ABS light periodically turns on and off, then, most likely, some contact in the ABS electrical circuit is junk. The car should be driven into the inspection ditch, check all wires and clean the electrical contacts. If the cause of the flashing of the ABS lamp is not found, then further troubleshooting should be continued in a specialized car service.
There are a number of features associated with servicing or repairing an ABS braking system. For example, before changing the brake fluid, the pressure accumulator in the ABS valve body must be discharged. To do this, with the ignition off, you must press the brake pedal twenty times. It should be remembered that by switching on the ignition, you are simultaneously connecting the electric pump in the ABS valve body. If the system is depressurized, then the liquid will simply be expelled from it. But the same technique can be used when pumping the system - the ignition is turned on just as much as air bubbles will come out of the transparent hose put on the pumping fitting.
Braking systems |
|||||||
|
Anti-lock braking system
[edit]
From Wikipedia, the free encyclopedia
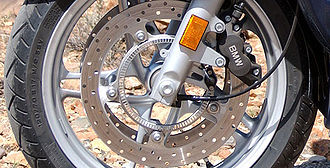
ABS on bMW motorcycle
Anti-lock braking system (ABS , ABS), it. antiblockiersystem English Anti - lock Brake System or Anti - skid system - a system that prevents wheel locking vehicle when braking. The main purpose of the system is to prevent the loss of vehicle control during hard braking and to exclude the possibility of uncontrolled slipping.
Currently, the ABS is usually part of a more complex electronic braking system, which may include an anti-slip system, a system electronic control stability, as well as an emergency braking assistance system.
ABS is installed on cars and trucks, motorcycles, trailers, as well as on the wheeled chassis of aircraft.
[edit] How the ABS works
When the vehicle is moving, the contact patch of its wheels is immobile relative to the road surface, that is, the resting friction force acts on the wheel. Since this force is greater than the sliding friction force, the deceleration when the wheels rotate at a speed corresponding to the vehicle speed will be more effective than the deceleration when the wheels slip relative to the road surface. In addition, a vehicle with one or more wheels in skid loses control.
[edit] System structure
The ABS consists of the following main components:
Speed \u200b\u200bor acceleration (deceleration) sensors installed on the vehicle wheel hubs.
Control valves, which are elements of the pressure modulator, installed in the line of the main brake system.
A control unit that receives signals from sensors and controls the operation of valves.
After the start aBS braking begins a constant and fairly accurate determination of the speed of rotation of each wheel. If a wheel starts to rotate much slower than the others (which means that the wheel is close to blocking), a valve in the brake line limits the braking force on that wheel. As soon as the wheel is released from the lock, the braking force is restored. [ source not specified 105 days ]
This process is repeated several times (or several tens of times) per second, and usually leads to noticeable pulsation of the brake pedal. Usually, it is on this basis that the driver can determine the moment when the ABS is activated. [ source not specified 105 days ]
The braking force can be limited as in the entire braking system at the same time ( single-channel ABS), and in the braking system of the board ( two-channel ABS) or even a separate wheel ( multichannel ABS). Single-channel systems provide fairly effective deceleration, but only if the traction conditions of all wheels are more or less the same. Multi-channel systems are more expensive and more complex than single-channel systems, but they are more effective when braking on uneven surfaces, if, for example, during braking, one or more wheels hit the ice, a wet section of the road or the side of the road. [ source not specified 105 days ]
Modern ABS includes a self-diagnostic system that controls the operation of all system components according to their physical parameters. The self-diagnosis system lights the ABS fault lamp on dashboard and writes the corresponding fault code into the memory of the control unit. After a malfunction is identified, this component is excluded from the system, or the entire system stops working, and the braking system continues to work. [ source not specified 105 days ]
In modern cars, electric brakesacting independently on each wheel. In this case, the ABS exists, basically, as one of the algorithms of the control unit of such a brake system and does not have any effect on the brake pedal or lever. [ source not specified 105 days ]
[edit] ABS performance
In some cases, the presence of ABS allows you to achieve a significantly shorter stopping distance than in its absence. In addition, the ABS allows the driver to maintain control over the vehicle during emergency braking, that is, it remains possible to perform rather sharp maneuvers directly during braking. The combination of these two factors makes ABS a very significant plus in ensuring active vehicle safety. [ source not specified 105 days ]
An experienced driver can effectively brake even without using the ABS, controlling the wheel breakdown moment on his own (most often this method of braking is used by motorcyclists) and weakening the braking force on the verge of blocking. The effectiveness of such braking can be comparable to braking when using a single-channel ABS. In any case, multichannel systems have the advantage of being able to control the braking force on each individual wheel, which gives not only effective deceleration, but also the stability of the vehicle's behavior in difficult conditions of uneven adhesion of the wheels to the road surface. [ source not specified 105 days ]
For an inexperienced driver, the presence of an ABS is better in any case, since it allows emergency braking in an intuitive way, simply by applying maximum effort to the brake pedal or handlebar while still being able to maneuver. [ source not specified 105 days ]
In some conditions, the operation of the ABS can lead to an increase in the braking distance. On loose surfaces such as deep snow, sand or gravel, wheels blocked when braking begin to dig into the surface, which gives additional deceleration. Unlocked wheels slow down under these conditions. In order to be able to effectively brake in such conditions, the ABS is often made disconnectable. In addition, some types of ABS have a special braking algorithm for loose surfaces, which leads to numerous short-term wheel locks. This braking technique allows you to achieve effective deceleration without losing control, as with a full lock. The type of surface can be set manually by the driver or can be determined by the system automatically, by analyzing the behavior of the car or using special sensors for determining the road surface. [ source not specified 105 days ]
[edit] Brake Assist
This technology first hit the consumer market in 1996 in the Mercedes-Benz SL-Class and S-Class. Since 1998, the company has started to implement this system in all of its models. standard configuration... Mercedes-Benz was soon followed by companies such as Audi, Acura, Infiniti, BMW, Rolls royce, Land rover and Volvo with its own Brake Assist developments.
Brake Assist is a driver-adaptive system that assists the driver when braking. The electronics that control the operation of Brake Assist are linked to the braking system and distinguish between emergency braking and, for example, stopping at traffic lights. Let's say a child unexpectedly ran out onto the road. Your foot instinctively presses the brake pedal, the sensor instantly calculates the reaction and the force of pressing the pedal and determines the degree of danger of the situation. Then the sensor sends a signal to the brakes in a fraction of a second, and then they - brake calipers, the ABS is activated, the vehicle slows down.
Brake Assist shortens the braking distance by 45 percent, although even experienced drivers can shorten the braking distance by only 10 percent, and the braking distance is a guarantee of the health and life of both the pedestrian and the driver.
Besides own developments Mercedes-Benz, such as the distance controller Distronic Plus, which controls the required distance to the vehicle in front, there are other types of Brake Assist. Volvo has invented the “City Safety system” that operates at vehicle speeds up to 30 km / h. The symbiosis of the navigator and Brake Assist is offered by Toyota, in which the system is activated in the event of emergency braking at traffic lights.
Anti-lock braking system (ABS, ABS)
Anti-lock braking system (ABS, ABS) is an automated system that prevents the wheels of the car from locking in the event of braking. The main task of the system is to ensure vehicle control during heavy braking. Also, the action of abs is aimed at eliminating the possibility of an uncontrolled slip of the car.
Now the anti-lock braking system (abs, abs) is one of the subsystems, the main system that ensures the safety of braking. Along with abs, it includes traction control, emergency braking system, electronic stabilization system.
Anti-lock braking system (ABS, ABS) is installed on most modern vehicles: trucks and cars, trailers, motorcycles, as well as on some aircraft.
The principle of operation of the ABS (ABS)
Let's describe the basic principle of ABS operation:
When the car is moving, the area of \u200b\u200bcontact of its wheels is unchanged relative to the carriageway. The wheel is affected by the static friction force. The sliding friction force is much less than the static friction force. Deceleration when spinning wheels at a speed equal speed the movement of the car will be more effective than deceleration with sliding wheels. It is also worth noting that a vehicle whose wheels are in sliding loses control when braking.
The essence of the anti-lock braking system (ABS, ABS) is to limit the braking force on the wheels. The limitation is made to a value not exceeding the static friction force between the wheel and the carriageway. This restriction prevents the wheel from skidding. In doing so, the anti-lock braking system tries to maximize the braking force to ensure effective deceleration.
The principle of operation of the anti-lock braking system (abs, abs) is as follows: at the beginning of braking, when the brake system is applied, sensors installed on the wheels of the car determine the beginning of the moment of an abrupt stop (blocking) of the wheels and through feedback, the braking force is weakened, which allows the wheel to turn engagement with the carriageway. This applies preventive measures to determine the moment of slippage, in order to prevent even short-term slippage.
System design
The following components are an integral part of the anti-lock braking system:
· Speed \u200b\u200bsensors installed on the wheels of the car, determining the speed;
· Control valves, in the main line of the vehicle brake system;
· Feedback unit that receives signals from sensors on wheels and regulates valve operation.
As soon as braking starts, the anti-lock braking system begins to accurately track the speed of rotation of each of the wheels. As soon as it is detected that the rotational speed of one of the wheels is significantly lower than the rotational speed of the others (which indicates a possible blockage), the braking force is limited by means of a valve located in the brake line of the locked wheel. As soon as the wheel speed is normalized, the anti-lock braking system regains the braking force. The described process occurs several times, while accompanied by a pulsation of the brake pedal. This is what informs the driver about the ABS operation.
Anti-lock braking system is divided into 3 types:
Single-channel ABS - braking forces are limited throughout the entire brake system simultaneously;
Two-channel ABS - braking forces on each side of the car are limited;
Multi-channel ABS - braking forces are limited at each individual wheel.
Single-channel anti-lock braking systems provide the best braking performance only when all wheels are on a similar surface. Multichannel systems provide the best braking on uneven road sections of all the systems listed, but they are much more complex and more expensive.
At the moment, cars are equipped with electric anti-lock braking systems (ABS, ABS), which independently track the rotation of each wheel. In this case, there is no feedback from the pedal.
Anti-lock braking system performance
The presence of ABS in the braking system can significantly reduce the braking distance. Also, the ABS allows the driver to maintain controllability of the car during emergency braking, which makes it possible to maneuver during braking. The listed advantages make ABS a necessary attribute in the braking system. modern car.
For an inexperienced driver, the presence of ABS is better, in any case, since it allows you to brake urgently in an intuitive way, simply by applying maximum force to the brake pedal, while maintaining the ability to maneuver.
The only drawback of modern ABS is braking on loose road sections (high snow, gravel, sand). The braking distance becomes longer than with complete blocking of the wheels, since the car does not "dig" into the surface, but continues to move. However, modern ABS has algorithms that are applied when braking on loose surfaces.
Hello dear car enthusiasts and blog readers Today we will talk about one of the main car safety systems, namely the anti-lock braking system.
Let's take a look at what it is:
Anti-lock braking system ( Anti-lock braking system) or just ABC, serves to prevent the wheels from locking during braking. The danger of wheel blocking is that during heavy braking, or when braking on slippery road, the driver may lose control of the vehicle due to uncontrolled sliding of the locked wheels. In such situations, the car can either stop "obeying the steering wheel" altogether, or, in best case increase the braking distance. It is to prevent such dangerous situations that the anti-lock braking system was created.
The ABS consists of acceleration sensors that are installed on the vehicle wheel hubs, control valves (pressure modulators) built into the brake line, as well as an electronic control unit (ECU) that receives signals from the sensors and controls the valves.
Each of the sensors measures the speed of rotation of the wheel on which it is installed. The information received by the sensor is sent to the ECU, where it is processed by the processor and, in accordance with the data received from the sensors, is sent to the valves, which act as an actuator. The valves, depending on the situation, change the pressure in the working brake cylinder of each wheel in such a way as to prevent it from stopping completely while driving. This process is repeated with very high frequency - several tens of times within a second. When the ABS is triggered, the driver can feel a noticeable pulsation of the brake pedal, and by this sign it is possible to determine the moment when the anti-lock braking system is activated.
What types of ABS are there?
The braking force can be limited not only in a single wheel, but also in all wheels at the same time, or in the wheels of one side of the car. It depends on the ABS design (single-channel or multi-channel). In addition, modern ABS is equipped with self-diagnostics systems that control the operation of all system nodes by physical parameters.
How to use ABS correctly?
Performing braking on a vehicle with ABS has its own characteristics. Of course, with such a system, the efficiency of the braking system is significantly increased. The main thing is that when braking, a car with ABC absolutely does not change its straight motion... Driving such a car, you can forget about smooth, intermittent braking, and constant control of wheel traction. On the contrary, if the car has an ABC, then the brakes need to be hit, as they say, that is, during emergency braking, the brake pedal must be pressed hard, applying full force to it. It should also be borne in mind that when braking, you do not need to use the help of a motor, that is, "brake with the engine" - ABC likes to work independently. In other words, during emergency braking, you must press both the brake pedal and the clutch pedal at the same time, disconnecting the engine from the transmission.
That's all, the main thing is not to pin all hopes on electronics and try to avoid moments in which ABS will turn on.
I'll tell you about the shortcomings of the ABS later,
Until next time!
› Why the brakes are anti-lock braking system (ABS)
Have you ever had to go around a sudden obstacle and brake at the same time? Surely yes. It would seem that this is difficult - pressed the brake, turned the steering wheel and corrected the trajectory. However, everything is relatively simple up to a certain point. If, during emergency braking, you press the brake pedal harder than necessary, the wheels may lock and ...
Further, two scenarios are possible. Both are due to the presence or absence of the anti-lock brake system (ABS - Anti-lock Brake System). If the car is archaic, has its pedigree from the mid-seventies of the last century, or rolled off the assembly line of one of the domestic car factories, then, no matter how hard you turn the steering wheel, the vehicle will not change its trajectory. The fact is that the locked wheels, sliding, deprive the driver of the opportunity to maneuver - having fallen into a skid, the car will go stupidly in a straight line, as if the steering wheel was cut off. Only an experienced pilot will be able to coolly unlock the wheels by momentarily releasing the brake pedal. And then, using impulse braking, regain control and extinguish speed. The second option is for a car equipped with ABS. The driver is only required to press the brake pedal harder and work quietly at the steering wheel. Do you feel the difference?
For 30 years, the system has undergone dramatic changes. The performance and the number of operating cycles per unit of time have increased tenfold. For example, the first control units for passenger cars weighed over 7 kg. Modern ones are much more compact and pull one and a half kilograms.
Blocking is also dangerous because it can cause the car to skid or drift to the side. This can happen when there is a dissimilar coating under the wheels, the axle load is greatly changed during the previous maneuver, or different tires (the latter sounds crazy, but in Russia, alas, it is not uncommon). In addition, when the wheels are locked, the vehicle can change its trajectory under the influence of any lateral force (road slope or collision). It is almost impossible to correct the trajectory in this case.
The ABS uses inductive frequency sensors and Hall effect sensors to determine the rotational speed. Each new generation of wheel speed sensors is getting smaller, more accurate and more reliable. At first, only one sensor was installed, which was mounted on the gearbox rear axle or checkpoint. Later, two more were added to it - on the front wheels. And only the latest versions of the ABS provide for the installation of sensors on each wheel, respectively, with individual modulators. By the way, the most ancient and primitive single-channel ABS acted on all braking mechanisms at once.
Another negative effect of blocking is an increase in stopping distance. The point here is that the static friction force is usually greater than the sliding friction force. Therefore, to stop the car as quickly as possible, it is necessary to generate such an amount of pressure in the brake lines so that the wheels rotate on the verge of blocking when braking. There is such an important indicator as relative slippage. Depending on the degree of braking of the wheel, it can vary from zero (the wheel rolls without slipping) to 100% (the wheel is completely locked). It has been experimentally established that the maximum braking efficiency is achieved at 15–20 percent slippage - that is, in the case when the rotation speed of a braked wheel is 15–20% lower than the speed of a free-wheeling wheel at a constant vehicle speed. Looking ahead, let's say that the electronics maintains exactly this value during braking, periodically blocking and unlocking the wheels.
Almost any modern ABS system includes: an electronic control unit (1), a modulator (2) that changes the pressure in hydraulic lines, wheel speed sensors (3) installed on the inner part of the wheel hub.
Progressive mankind finally realized the harm of locked wheels only in the 70s of the last century. The pioneer in this area was Mercedes-Benz, which, together with Bosch, developed a system that in 1979 began to be installed on the Mercedes S-class. The basic principle of the ABS was formed just then, and then it was only improved.
Modern electronics (ABS, traction control, ESP) take into account more than just the wheel speed in order to keep the vehicle's lateral and longitudinal dynamics under control. Controlled are the steering angle, the degree of body roll, acceleration ... The pressure in the brake circuits is generated from the totality of the received data, plus in some cases the engine thrust is forcedly changed.
The task of ABS is to regulate the speed of rotation of the wheels by changing the pressure in the lines of the brake system. To control the angular velocity, you need to know its magnitude and how it changes over time. Each wheel is equipped with a sensor that generates electrical impulses with a frequency proportional to the wheel speed. This information is sent to the ABS control unit.
If, during braking, the angular speed of the wheel approaches zero, the electronic brain will immediately decide to “release” it. The hydraulic modulator with the help of an electrovalve will release the pressure from the line and redirect the "excess" portion of the brake fluid to the accumulator. The pressure will decrease until the wheel, again "grasping" the surface, spins up to a certain speed. Further ABS will sharply increase the pressure in the line again and slow down the wheel. The cycle will continue until the car stops or the driver releases the pedal pressure to a position where ABS is not needed.
The systems available on the market are highly tuned and provide maximum braking performance.
Many will say: "Little wisdom!" You can intermittently brake yourself. And the truth is: in many cases, this method of deceleration on vehicles not equipped with ABS allows you to bypass a sudden obstacle during emergency braking. When the wheels are locked - you brake, as soon as you "release" - you get the opportunity to correct the direction of travel. Naturally, in this situation, the braking distance will increase significantly, but the driver will be able to bypass the obstacle and extinguish the skid with the preemptive action of the steering wheel.
Unfortunately, no award-winning racer is capable of delivering "portioned" braking at the rate that ABS does. The system (depending on the version) manages to lock and unlock the wheels about 15 times per second. In addition, the driver simultaneously acts on all brakes (this is how the first ABS systems worked), while modern 4-channel anti-lock braking systems monitor the rotational speed and adjust the braking force for each wheel separately.
Hydraulic modulator combined with control unit (black).
In most modern cars, ABS works in conjunction with EBD (Electronic Brake Distribution), a brake force distribution system that doses the intensity of the braking to each wheel. With EBD, you can safely brake in the corner and on the "mixed". By the difference in rotational speeds, the electronics will understand that the wheels have hit areas with a dissimilar coating, and will reduce the braking forces on wheels that have better grip with the road. By the way, the intensity of deceleration in this case will decrease and will be determined by the frictional force of the wheel (s), which has the worst grip.
It is worth noting that for maximum deceleration efficiency, the brake pedal on cars with ABS must be pressed into the floor with strength. However, the latter does not have to be done by those drivers whose cars are equipped with the Brake Assist system, which itself creates excessive pressure in the brake line, "braking" for a weak or indecisive person. With standard decelerations, it does not interfere. However, a sharp press (blow) on the Brake Assist pedal is regarded as a signal for emergency braking and comes into play.
But not everything is so smooth. ABS, like any other system, has disadvantages. For example, a simple "antiblock" can lose the usual brakes on snow, ice or sand, negate the advantages of studded rubber. Indeed, on ice, the spikes provide the greatest deceleration only with the maximum relative slip, when they, like claws, dig into the ice and furrow it. The trick is that ABS, trying to release the wheels, does not allow the studs to work and thereby increases the braking distance. The same happens on unpaved roads (sand, gravel, clay) and snow-covered surfaces.
The presence of ABS is not a reason for abandoning studded rubber. During blocking, the studs will still cling to the ice and provide more reliable deceleration than non-studded tires.
Cars with ABS in this case have a longer braking distance, because the permanently unlocking wheels do not create a "plow effect". But it is precisely on such surfaces that the locked wheels have the maximum braking efficiency - due to the fact that they rake in front of them "rollers" of soil or snow. This is why you need to remember that on icy, snowy or unpaved surfaces, the braking distance of a vehicle without ABS may be shorter.
Cars with ABS remain steerable during emergency braking.
The ABS can put a small pig on an uneven road. If, during braking, one wheel hovers for a moment in the air and is blocked, the deceived electronics will begin to save you from skidding and immediately reduce the pressure in the remaining lines. When cornering, the car will unpleasantly wag its tail, and the braking distance will increase. In principle, no one is insured against such accidental breaks, but it must be remembered that a good suspension is the key to adequate ABS operation.
In case of any malfunction in the system, a warning lamp on the dashboard comes on. In this case, there is only one advice - run to the service.
Progress gives birth to more and more advanced systems. Operating with a large number of indications, they are able to adapt to the type of road surface and brake according to one of the previously laid down effective algorithms. Of course, electronics cannot be perceived as a panacea for all ills, but statistics are stubborn things: a competently tuned ABS with all vehicle systems in good condition on dry and wet surfaces on average helps to save up to 20% of the braking distance and leaves the driver a chance to maneuver. Needless to say, life and health can depend on these precious meters?
Over the past ten years, the antilock braking system ABS (Antilock Brake System) has become widespread among car manufacturers around the world.
The advantage of this system has long been proven by the preservation of many human lives on the roads.
The purpose of ABS can be formulated very simply - this system prevents the wheels from locking during braking and keeps the car stable on the road.
The essence of ABS work is to limit the braking force on the wheels to a value not exceeding the static friction force between the wheel and the road surface, thus preventing the wheel from slipping. However, the braking force must be as high as possible to ensure effective deceleration.
Figure: 1. Layout of ABS units on a passenger car
In fig. 1 shows general scheme ABS passenger car.
The anti-lock braking system includes the following components:
Speed \u200b\u200bor acceleration (deceleration) sensors installed on the vehicle wheel hubs;
Control valves, which are elements of the hydraulic pressure modulator, installed in the line of the brake system;
A control unit that receives signals from sensors and controls the operation of valves.
Sensors for determining the angular speed of a wheel - electromagnetic type (DSK). They are installed on the fixed part of the front hub and rear suspension and secured with a flange.
Toothed rims are fixed on the moving part of the hubs of all wheels of the car.
When the gear rim rotates, the teeth change the magnetic field of the sensor, and pulses are formed, the frequency of which is directly proportional to the angular speed of the wheel rotation.
In fig. 2 shows oscillograms of signals from sensors at different speeds of rotation of a car wheel.
Figure: 2. Oscillograms of signals from ABS sensors
The signals from the sensors are fed directly to the electronic control unit, where it determines the speed of rotation of one or another wheel at the moment of braking the car by the number and repetition rate of pulses.
The main unit of the anti-lock braking system is a hydromodulator with a built-in electronic control unit, which, after determining the angular speed of the wheels, turns on / off the solenoid valves (EMC), thereby controlling the pressure in the brake cylinders, eliminating wheel blocking and maintaining vehicle control on a difficult road section.
The hydraulic modulator has two main solenoid valves, which are controlled by an electronic control unit. The first valve blocks the access of the brake fluid to the line coming from the master cylinder, and the second, at excessive pressure, opens the supply of the brake fluid to the reserve reservoir of the accumulator.
In modern cars, the hydromodulator can contain more than two valves, which ensure the operation of the brake cylinders of the front and rear suspension wheels.
Figure: 3. Place of installation of the hydromodulator on a VAZ KALINA car
Also, the hydromodulator includes a return pump and an electric motor of the return pump, which, when the pressure drops, pumps excess brake fluid into the reservoir of the main brake cylinder.
In fig. 3 shows the location of the hydromodulator on the LADA KALINA car, and fig. 4 - for UAZ PATRIOT.
Figure: 4. Place of installation of the hydromodulator on the UAZ PATRIOT vehicle
In fig. 5 shows a schematic diagram ABS car LADA KALINA, LADA PRIORA, and in fig. 6 families lineup Ssang Yong.
The hydraulic modulator control unit is an electronic circuit controlled by a central microprocessor. The circuit contains a non-volatile memory microcircuit that stores fault codes, parameters of the general passport of the hydromodulator and the entire system.
With the development of electronics and its increasing introduction into the automotive industry, the electrical equipment of the modern car has also improved.
The ABS system has also undergone major changes. Along with it, new security systems have appeared that work together. The following systems can be distinguished:
ASR (Anti-Slip Control) is an anti-slip system that prevents slipping of the driving wheels, for example on ice or gravel, by acting on the braking system and engine operation;
EBD (Electronic Brake Distribution) is an electronic brake force distribution system. It prevents the so-called overbraking rear wheels before the ABS starts working;
ESP (Electronic Stability Program) is an electronic anti-skid system with elimination of a turn (skid) when braking a car.
On the device and work the most difficult eSP systems let's dwell in more detail.
Figure: five. Schematic diagram ABS systems of the car LADA KALINA and LADA PRIORA
The ESP system provides traction control and elimination of the vehicle's turn.
When the driver is carrying out a maneuver to avoid a sudden obstacle, sensors (sensors) record the unstable state of the vehicle. Electronic system ESP makes an instant calculation for further action to get out of this situation.
The ESP system includes the following components:
The electronic unit management;
Brake master cylinder with brake pressure sensor;
Sensors (sensors) for steering wheel angle, lateral acceleration, yaw system, additional sensors for rear and front wheels.
ESP system operation switch;
Control lamp ASR / ESP operation located on dashboard.
The steering angle sensor is mounted directly on the steering shaft next to the steering wheel. It is a photosensor that is triggered when the light flux is blocked during the rotation of the steering wheel by a program washer, on which there are slots with certain dimensions.
The lateral acceleration sensor consists of a permanent magnet attached to a spring plate and a Hall sensor. On a car, it is usually installed under the driver's seat.
The brake pressure sensor contains a piezoelectric element that is pressurized by the brake fluid.
The ABS system is a device with a large current consumption from the vehicle's on-board network (up to 40 A), which requires special attention to the condition of the contacts in the power circuits of the wiring, the health of the battery and generator.
Frequent malfunctions associated with the operation of the ABS system may arise, for example, due to an untimely maintenance or due to improper repair of suspension elements or electrical equipment of the car. Consider the most common malfunctions of the ABS system, their diagnosis and elimination.
It should be noted that when any malfunction occurs, a lamp with the inscription "ABS" lights up on the instrument panel of the car.
After that, driving the car is possible, only it is necessary to take into account that at this time the car's braking system works in normal mode.
Figure: 6. Schematic diagram of the ABS system of Ssang Yong cars
Before traveling to a service station (except for cars located in warranty service), some troubleshooting work can be done.
First check the protective fuses electronic circuit ABS systems, the operation of the vehicle generator (when the voltage drops to 10.5 V, the ABS system is automatically disabled).
The next step in checking is the wheel speed sensors. The cause of the malfunction may be trivial dirt in the gear rim and an increase or decrease in the air gap between the sensor and the gear rim (the gaps of the sensors of the front wheels are 0.2 ... 1.5 mm, the rear ones are 0.5 ... 2.0 mm, depending on the car model).
Eliminate these faults with a brush and blowing compressed air.
You should especially pay attention to unstable work ABS systems. It can manifest itself as a partial failure or a delayed reaction, which is dangerous for the driver, especially in emergency situation.
The source of this malfunction may be excessive play of wheel bearings, tires of different sizes on the car and their wear, etc.
The table shows the ABS fault codes lADA cars KALINA and LADA PRIORA.
Fault codes of the ABS system of LADA KALINA and LADA PRIORA cars
Code Description |
|
Failure in a chain of the front left DSC or implausible signal |
|
Failure in the front right DSC circuit or invalid signal |
|
Failure in the rear left DSC circuit or implausible signal |
|
Failure in the rear right DSC circuit or implausible signal |
|
Failure in the chain of the exhaust front left EMC |
|
Failure in a chain of the intake front left EMC |
|
Failure in the chain of the exhaust front right EMC |
|
Failure in the chain of the intake front right EMC |
|
Refusal in a chain of an exhaust rear left EMC |
|
Refusal in a chain of the intake rear left EMC |
|
Failure in the chain of the exhaust rear right EMC |
|
Failure in the intake rear right EMC circuit |
|
Failure in the EVN circuit |
|
Failure in the EMC supply voltage relay circuit |
|
Failure in the brake signal switch circuit |
|
DSC frequency measurement error |
|
Internal ECU malfunction |
|
Supply voltage below or above the operating range |
|
After eliminating the malfunction, delete the malfunction code from the ECU memory |