Năm 1799, ông nhận được bằng sáng chế về việc sử dụng và phương pháp thu được khí đốt bằng cách chưng cất khô gỗ hoặc than, nhưng khí đốt không chỉ thích hợp để thắp sáng.
Vinh dự xây dựng một động cơ thành công về mặt thương mại đốt trong thuộc về thợ cơ khí người Bỉ Jean Etienne Lenoir. Làm việc tại một nhà máy mạ điện, Lenoir đã đi đến kết luận rằng hỗn hợp nhiên liệu không khí trong động cơ xăng có thể được đánh lửa bằng tia lửa điện, và quyết định chế tạo động cơ dựa trên ý tưởng này. Sau khi giải quyết được các vấn đề nảy sinh trên đường đi (hành trình căng và quá nhiệt của piston, dẫn đến động cơ), suy nghĩ về hệ thống bôi trơn và làm mát động cơ, Lenoir đã tạo ra một động cơ đốt trong khả thi. Năm 1864, hơn ba trăm loại động cơ có công suất khác nhau đã được sản xuất. Sau khi trở nên giàu có, Lenoir ngừng tiếp tục cải tiến chiếc xe của mình, và điều này đã định đoạt trước số phận của nó - nó bị loại khỏi thị trường bởi một động cơ tiên tiến hơn do nhà phát minh người Đức August Otto tạo ra và nhận được bằng sáng chế cho việc phát minh ra mô hình động cơ khí của ông vào năm 1864.
Năm 1864, nhà phát minh người Đức Augusto Otto đã ký một hợp đồng với kỹ sư giàu có Langen để thực hiện phát minh của ông - công ty "Otto and Company" được thành lập. Cả Otto và Langen đều không có đủ kiến \u200b\u200bthức trong lĩnh vực kỹ thuật điện và từ chối đánh lửa điện... Chúng được đốt cháy bằng ngọn lửa trần qua một ống. Xylanh của động cơ Otto, không giống như động cơ Lenoir, nằm thẳng đứng. Trục quay được đặt trên hình trụ từ mặt bên. Nguyên lý hoạt động: trục quay nâng piston lên bằng 1/10 chiều cao xylanh, do đó một khoảng trống hiếm được hình thành dưới piston và một hỗn hợp khí và khí được hút vào. Sau đó hỗn hợp bốc cháy. Trong quá trình nổ, áp suất dưới piston tăng lên khoảng 4 atm. Dưới tác dụng của áp suất này, pittông tăng lên, thể tích khí tăng và áp suất giảm. Piston, đầu tiên dưới áp suất khí, và sau đó theo quán tính, tăng lên cho đến khi tạo ra chân không bên dưới nó. Nhờ đó, năng lượng của nhiên liệu bị đốt cháy đã được sử dụng trong động cơ với hiệu suất tối đa. Đây là phát hiện ban đầu chính của Otto. Hành trình làm việc đi xuống của pít tông bắt đầu dưới tác dụng của áp suất khí quyển, và sau khi áp suất trong xilanh đạt đến khí quyển, van xả mở ra và pít tông với khối lượng của nó dịch chuyển khí thải. Do sản phẩm mở rộng hoàn thiện hơn hiệu quả đốt cháy động cơ này cao hơn đáng kể so với hiệu suất của động cơ Lenoir và đạt 15%, tức là nó vượt quá hiệu suất của động cơ tốt nhất động cơ hơi nước lúc đó. Ngoài ra, động cơ của Otto đã gần gấp 5 lần tiết kiệm hơn động cơ Lenoir, họ ngay lập tức bắt đầu có nhu cầu lớn. Trong những năm tiếp theo, khoảng 5.000 chiếc trong số đó đã được sản xuất. Mặc dù vậy, Otto vẫn làm việc chăm chỉ để cải thiện thiết kế của họ. Chẳng bao lâu, một ổ quay đã được sử dụng. Tuy nhiên, phát minh quan trọng nhất của ông là vào năm 1877, khi Otto nhận được bằng sáng chế cho động cơ mới với chu kỳ bốn kỳ. Chu kỳ này là trọng tâm của hầu hết các động cơ xăng và xăng cho đến ngày nay.
Các loại động cơ đốt trong
Động cơ đốt trong piston
ICE quay
Tuabin khí động cơ đốt trong
- Động cơ pittông - buồng đốt được chứa trong xi lanh, tại đây nhiệt năng của nhiên liệu được biến đổi thành cơ năng, từ chuyển động tịnh tiến của pittông được chuyển thành năng lượng quay nhờ cơ cấu tay quay.
Động cơ đốt trong được phân loại:
a) Theo hẹn - chúng được chia thành vận tải, văn phòng phẩm và đặc biệt.
b) Theo loại nhiên liệu sử dụng - chất lỏng nhẹ (xăng, gas), chất lỏng nặng (nhiên liệu điêzen, dầu nhiên liệu hàng hải).
c) Theo phương pháp hình thành hỗn hợp cháy - ngoài (bộ chế hòa khí, kim phun) và trong (trong xi lanh động cơ đốt trong).
d) Bằng cách đánh lửa (đánh lửa cưỡng bức, đánh lửa nén, nung nóng).
e) Theo cách bố trí các xilanh thẳng hàng, thẳng đứng, đối diện với một và hai trục khuỷu, hình chữ V với trục khuỷu trên và dưới, hình VR và hình chữ W, dãy đơn và dãy đôi hình sao, hình chữ H, dãy đôi với trục khuỷu song song, "quạt đôi", hình thoi, ba chùm và một số loại khác.
Xăng
Bình xăng con
Chu kỳ hoạt động của động cơ đốt trong bốn kỳ mất hai doanh thu đầy đủ tay quay, bao gồm bốn hành trình riêng biệt:
- đầu vào,
- tính phí nén,
- đột quỵ làm việc và
- nhả (xả).
Sự thay đổi hành trình làm việc được cung cấp bởi một cơ cấu phân phối khí đặc biệt, thường nó được thể hiện bằng một hoặc hai trục cam, hệ thống van đẩy và van trực tiếp thay đổi pha. Một số động cơ đốt trong đã sử dụng ống lót (Ricardo) với các cổng nạp và / hoặc xả cho mục đích này. Trong trường hợp này, sự giao tiếp của khoang xi lanh với các ống góp được đảm bảo bởi chuyển động quay và hướng tâm của ống bọc, các cửa sổ mở ra kênh mong muốn. Do đặc thù của động lực học khí - quán tính của khí, thời gian xuất hiện của gió khí, hành trình nạp, hành trình và xả trong một chu kỳ bốn kỳ thực sự trùng nhau, điều này được gọi là thời gian van chồng chéo... Tốc độ làm việc của động cơ càng cao thì độ trùng pha càng lớn và càng lớn thì mômen của động cơ đốt trong càng giảm bởi vòng quay thấp... Do đó trong động cơ hiện đại các thiết bị đốt trong ngày càng được sử dụng nhiều để thay đổi thời gian van trong quá trình hoạt động. Động cơ điều khiển van điện từ (BMW, Mazda) đặc biệt thích hợp cho mục đích này. Các động cơ Tỷ lệ nén biến thiên (SAAB) cũng có sẵn với hiệu suất linh hoạt hơn.
Động cơ hai kỳ có nhiều cách bố trí và nhiều loại hệ thống kết cấu. Nguyên tắc cơ bản của bất kỳ động cơ hai kỳ nào là piston thực hiện các chức năng của bộ phận phân phối khí. Nói một cách chính xác, chu trình làm việc bao gồm ba bước: hành trình làm việc kéo dài từ tâm điểm chết trên ( TDC) lên đến 20-30 độ đến trung tâm chết dưới cùng ( NMT), nhặt rác, thực sự kết hợp nạp và xả, và nén, kéo dài từ 20-30 độ sau BDC đến TDC. Theo quan điểm của động lực học chất khí, sự tẩy rửa là liên kết yếu của chu trình hai kỳ. Một mặt, không thể đảm bảo tách biệt hoàn toàn phí mới và khí thải, do đó, hoặc sự mất mát của hỗn hợp tươi là không thể tránh khỏi, bay ra ngoài theo nghĩa đen ống xả (nếu động cơ đốt trong là diesel, chúng ta đang nói đến sự mất mát không khí), mặt khác, hành trình làm việc kéo dài không phải nửa vòng quay mà ít hơn, tự nó làm giảm hiệu suất. Đồng thời, thời lượng cực kỳ quá trình quan trọng Không thể tăng trao đổi khí trong động cơ bốn kỳ chiếm một nửa chu kỳ làm việc. Động cơ hai kỳ có thể hoàn toàn không có hệ thống phân phối khí. Tuy nhiên, nếu chúng ta không nói đến động cơ giá rẻ được đơn giản hóa, thì động cơ hai kỳ phức tạp hơn và đắt hơn do bắt buộc phải sử dụng quạt gió hoặc hệ thống điều áp, mật độ nhiệt tăng lên của CPG đòi hỏi nhiều vật liệu đắt tiền hơn cho piston, vòng đệm, ống lót xi lanh. Hiệu suất của piston đối với các chức năng của phần tử phân phối khí bắt buộc phải có chiều cao của nó không nhỏ hơn hành trình piston + chiều cao của các lỗ thổi, điều này là không quan trọng ở xe mô tô, nhưng đáng kể làm cho piston nặng hơn ngay cả ở công suất tương đối thấp. Khi công suất được đo bằng hàng trăm mã lực, sự gia tăng khối lượng piston trở thành một yếu tố rất nghiêm trọng. Sự ra đời của ống bọc phân phối hành trình dọc trong động cơ Ricardo là một nỗ lực nhằm giảm kích thước và trọng lượng của piston. Hệ thống hóa ra phức tạp và tốn kém để thực hiện, ngoại trừ ngành hàng không, những động cơ như vậy không được sử dụng ở bất kỳ nơi nào khác. Van xả (với van một dòng thổi) có cường độ nhiệt gấp đôi so với van xả của động cơ bốn thì và điều kiện thoát nhiệt kém hơn, và ghế của chúng tiếp xúc trực tiếp với khí thải lâu hơn.
Đơn giản nhất theo quan điểm của trình tự công việc và phức tạp nhất theo quan điểm thiết kế là hệ thống Fairbanks - Morse, được giới thiệu ở Liên Xô và ở Nga, chủ yếu bằng các động cơ diesel của dòng D100. Động cơ này là một hệ thống trục đôi đối xứng với các piston phân kỳ, mỗi piston được kết nối với trục khuỷu riêng của nó. Như vậy, động cơ này có hai trục khuỷu, đồng bộ về cơ khí; cái nối với piston xả nằm trước cửa nạp 20-30 độ. Do tiến bộ này, chất lượng của quá trình xả đáy, trong trường hợp này là dòng chảy trực tiếp, được cải thiện và sự nạp đầy của xi lanh được cải thiện, vì ở cuối quá trình xả đáy, các cổng xả đã được đóng lại. Trong những năm 30 - 40 của thế kỷ XX, các phương án với các cặp piston phân kỳ đã được đề xuất - hình thoi, hình tam giác; có những động cơ diesel của máy bay với ba piston phân kỳ hướng tâm, trong đó hai ống nạp và một ống xả. Trong những năm 1920, Junkers đề xuất một hệ thống trục đơn với các thanh nối dài được kết nối với các chốt piston phía trên bằng các cánh tay quay đặc biệt; pít tông phía trên truyền lực tới trục khuỷu bằng một cặp thanh nối dài và có ba khuỷu trục trên mỗi xi lanh. Trên cánh tay của rocker cũng là những pít-tông vuông của các hốc thanh tẩy. Động cơ hai thì với các piston phân kỳ của bất kỳ hệ thống nào về cơ bản đều có hai nhược điểm: thứ nhất, chúng rất phức tạp và có kích thước, thứ hai, các piston và ống xả ở khu vực cửa sổ xả có ứng suất nhiệt đáng kể và có xu hướng quá nhiệt. Vòng piston xả cũng bị ứng suất nhiệt, dễ bị co ngót và mất tính đàn hồi. Những tính năng này làm cho thiết kế những động cơ như vậy không phải là một nhiệm vụ tầm thường.
Động cơ van dòng chảy trực tiếp được trang bị trục cam và các van xả. Điều này làm giảm đáng kể các yêu cầu về vật liệu và thiết kế của CPG. Việc nạp vào thông qua các cửa sổ trong ống lót xi lanh, được mở bởi piston. Đây là cách lắp ráp động cơ diesel hai kỳ hiện đại nhất. Khu vực cửa sổ và lớp lót ở phía dưới trong nhiều trường hợp được làm mát bằng không khí tích điện.
Trong trường hợp một trong những yêu cầu chính đối với động cơ là giảm chi phí, chúng được sử dụng các loại khác nhau đường viền buồng quay-cửa sổ thổi - vòng lặp, vòng lặp qua lại (bộ làm lệch hướng) trong các sửa đổi khác nhau. Để cải thiện các thông số động cơ, các kỹ thuật thiết kế khác nhau được sử dụng - chiều dài của các kênh hút và xả có thể thay đổi, số lượng và vị trí của các kênh rẽ nhánh có thể thay đổi, ống cuốn, bộ cắt khí quay, tấm lót và cửa chớp được sử dụng để thay đổi chiều cao của cửa sổ (và theo đó, thời điểm bắt đầu hút và xả). Hầu hết các động cơ này đều được làm mát bằng gió một cách thụ động. Nhược điểm của chúng là chất lượng trao đổi khí tương đối thấp và mất hỗn hợp dễ cháy trong quá trình tẩy rửa; khi có nhiều xi lanh, các phần của các buồng quay phải được tách ra và bịt kín, việc thiết kế trục khuỷu trở nên phức tạp hơn và tốn kém hơn.
Các đơn vị bổ sung cần thiết cho động cơ đốt trong
Nhược điểm của động cơ đốt trong là chỉ phát huy được công suất cao nhất ở dải vòng tua hẹp. Vì vậy, bộ truyền động là một thuộc tính tích hợp của động cơ đốt trong. Chỉ trong một số trường hợp (ví dụ, trong máy bay), nó có thể được thực hiện mà không cần một đường truyền phức tạp. Ý tưởng về một chiếc xe hybrid đang từng bước chinh phục thế giới, trong đó động cơ luôn hoạt động ở mức tối ưu.
Ngoài ra, động cơ đốt trong cần có hệ thống động lực (cung cấp nhiên liệu và không khí - điều chế hỗn hợp nhiên liệu - không khí), hệ thống xả (để loại bỏ khí thải), nó cũng không thể thiếu hệ thống bôi trơn (được thiết kế để giảm lực ma sát trong các cơ cấu động cơ, bảo vệ các bộ phận động cơ khỏi bị ăn mòn, cũng như kết hợp với hệ thống làm mát để duy trì điều kiện nhiệt tối ưu), hệ thống làm mát (để duy trì điều kiện nhiệt tối ưu của động cơ), hệ thống khởi động (sử dụng các phương pháp khởi động: khởi động bằng điện, sử dụng động cơ khởi động phụ, khí nén, sử dụng sức người ), hệ thống đánh lửa (để đốt cháy hỗn hợp nhiên liệu-không khí, được sử dụng trong động cơ đánh lửa cưỡng bức).
Xem thêm
- Philippe Le Bon là một kỹ sư người Pháp, người đã nhận được bằng sáng chế năm 1801 cho động cơ đốt trong nén hỗn hợp khí và không khí.
- Động cơ quay: thiết kế và phân loại
- Động cơ piston quay (động cơ Wankel)
Ghi chú
Liên kết
- Ben Knight "Tăng số dặm bay" // Bài báo về Công nghệ làm giảm mức tiêu thụ nhiên liệu của động cơ bên trong ô tô
Động cơ đốt trong - động cơ , trong đó nhiên liệu cháy trực tiếp trong buồng làm việc ( phía trong ) động cơ. ICE chuyển đổi áp lực từ sự đốt cháy nhiên liệu trong công việc cơ khí.
- không có thêm các yếu tố truyền nhiệt - nhiên liệu, đốt cháy, tự nó tạo thành chất lỏng hoạt động.
- nhỏ gọn hơn, vì nó không có một số đơn vị bổ sung
- dễ dàng hơn
- kinh tế hơn
- tiêu thụ khí hoặc lỏng nhiên liệu có các thông số được chỉ định rất chặt chẽ (độ bay hơi, điểm chớp cháy của hơi, tỷ trọng, nhiệt đốt cháy, trị số octan hoặc số Cetane), vì bản thân hiệu suất của động cơ đốt trong phụ thuộc vào các đặc tính này.
YouTube bách khoa
1 / 4
Nguyên lý hoạt động của động cơ đốt trong
Thiết bị chung của động cơ đốt trong
Bài 179. Động cơ đốt trong - 1
10 chiếc xe nhỏ kỳ lạ nhất với động cơ đốt trong
Phụ đề
Lịch sử hình thành
Năm 1807, một nhà phát minh người Pháp gốc Thụy Sĩ Francois Isaac de Rivas * (François Isaac de Rivaz) đã chế tạo động cơ piston đầu tiên, thường được gọi là công cụ de Rivas... Động cơ chạy bằng khí hydro, có các yếu tố cấu trúc đã được đưa vào các nguyên mẫu ICE tiếp theo: nhóm thanh truyền-pít-tông và bộ đánh lửa. Động cơ đốt khí hai thì có thể sử dụng thực tế đầu tiên được thiết kế bởi một thợ cơ khí người Pháp Etienne Lenoir (1822-1900) năm 1860. Sức mạnh là 8,8 kWh (11,97 l. từ.). Động cơ là một cỗ máy hai xi lanh, nằm ngang, hoạt động bằng hỗn hợp không khí và gas thắp sáng với sự đánh lửa bằng tia lửa điện từ nguồn bên ngoài. Hiệu quả động cơ không vượt quá 4,65%. Bất chấp những thiếu sót, động cơ Lenoir đã trở nên phổ biến. Dùng làm động cơ thuyền.
Tìm hiểu về động cơ Lenoir, một nhà thiết kế xuất sắc người Đức Nikolaus August Otto (1832-1891) tạo ra hai nét vào năm 1863 động cơ khí quyển đốt trong. Động cơ có bố trí xi lanh thẳng đứng, đánh lửa bằng ngọn lửa trần và Hiệu quả Lên đến 15 %. Đã tháo động cơ Lenoir.
Năm 1876, Nikolaus August Otto đã xây dựng một bốn thì động cơ khí đốt trong.
Năm 1885 kỹ sư người Đức Gottlieb Daimler và Wilhelm Maybach phát triển một loại xăng nhẹ bộ chế hòa khí... Daimler và Maybach đã sử dụng nó để tạo ra chiếc xe máy đầu tiên vào năm 1885 và vào năm 1886 trên chiếc ô tô đầu tiên.
Máy kéo động cơ đốt trong có thể sử dụng thực tế đầu tiên là máy kéo ba bánh Ivel 1902 của Mỹ do Dan Alborn sản xuất. Khoảng 500 cỗ máy nhẹ và mạnh này đã được chế tạo.
Gần như đồng thời ở Đức theo lệnh của Liên Xô và theo dự án của giáo sư Yu.V. Lomonosov về hướng dẫn cá nhân V.I.Lênin trong 1924 năm tại nhà máy Esslingen của Đức (trước đây là Kessler) gần Stuttgart, một đầu máy diesel Eel2 (ban đầu là Yue001) đã được chế tạo.
Các loại động cơ đốt trong
Nếu nhiên liệu dễ cháy, sự chớp cháy xảy ra trước khi pít tông TDC ... Điều này sẽ làm cho piston quay trục khuỷu theo hướng ngược lại - một hiện tượng được gọi là bắn ngược.
Số octan là thước đo phần trăm isooctan trong hỗn hợp heptan-octan và phản ánh khả năng chống tự bốc cháy của nhiên liệu theo nhiệt độ. Nhiên liệu có trị số octan cao hơn cho phép động cơ có tỷ lệ nén hoạt động mà không có xu hướng tự phát cháy và kích nổ, do đó, có tỷ số nén cao hơn và hiệu suất cao hơn.
Trái với suy nghĩ thông thường, động cơ hiện đại, thường được gọi là diesel, không hoạt động theo chu trình diesel và bởi chu kỳ Trinkler-Sabate với nguồn cung cấp nhiệt hỗn hợp.
Những bất lợi của động cơ diesel là do đặc thù của chu trình vận hành - ứng suất cơ học cao hơn, đòi hỏi độ bền kết cấu tăng lên và kết quả là tăng kích thước, trọng lượng và tăng giá thành do thiết kế phức tạp và sử dụng vật liệu đắt tiền hơn. Cũng thế động cơ diesel với chi phí đốt cháy không đồng nhất được đặc trưng bởi lượng phát thải muội không thể tránh khỏi và tăng oxit nitơ trong khí thải.
Động cơ xăng
Động cơ đốt cháy làm nhiên liệu hydrocacbon ở trạng thái khí trong điều kiện bình thường:
- hỗn hợp khí hóa lỏng - được chứa trong xi lanh dưới áp suất hơi bão hòa (đến 16 aTM). Bốc hơi trong máy hóa hơi pha lỏng hoặc pha hơi của hỗn hợp mất dần áp suất trong bộ giảm khí để gần với khí quyển và được động cơ hút vào ống nạp thông qua bộ trộn khí-không khí hoặc được bơm vào đường ống nạp bằng điện kim phun ... Đánh lửa được thực hiện với sự trợ giúp của tia lửa điện trượt giữa các điện cực của bugi.
- cô đặc khí tự nhiên - được lưu trữ trong quả bóng bay dưới áp suất 150-200 aTM ... Cấu trúc của hệ thống cung cấp điện tương tự như hệ thống cung cấp khí đốt hóa lỏng, điểm khác biệt là không có thiết bị bay hơi.
- khí máy phát điện - khí nhận được chuyển nhiên liệu rắn thành khí ... Các chất sau được sử dụng làm nhiên liệu rắn:
Khí-diesel
Phần chính của nhiên liệu được chuẩn bị như một trong các loại động cơ khí, nhưng được đánh lửa không phải bởi một ngọn nến điện, mà bởi một phần đánh lửa của nhiên liệu diesel, được phun vào xi lanh tương tự như động cơ diesel.
Piston quay
Do nhà phát minh Wankel đề xuất vào đầu thế kỷ 20. Cơ sở của động cơ là một rôto hình tam giác (pít-tông) quay trong một buồng hình số 8 đặc biệt đóng vai trò là pít-tông, trục khuỷu và bộ phân phối khí. Thiết kế này cho phép bất kỳ 4 thì chu trình diesel , Stirling hoặc là Otto mà không cần sử dụng một cơ chế phân phối khí đặc biệt. Trong một vòng quay, động cơ thực hiện ba chu kỳ làm việc hoàn chỉnh, tương đương với hoạt động của động cơ piston sáu xi lanh. Được chế tạo nối tiếp bởi NSU ở Đức (xe hơi RO-80), VAZ ở Liên Xô (VAZ-21018 "Zhiguli", VAZ-416 , VAZ-426 , VAZ-526), Mazda ở Nhật Bản (Mazda RX-7, Mazda RX-8). Mặc dù đơn giản về cơ bản, nó có một số khó khăn về thiết kế khiến việc triển khai rộng rãi rất khó khăn. Những khó khăn chính liên quan đến việc tạo ra các vòng đệm hiệu quả bền giữa rôto và buồng và với việc xây dựng hệ thống bôi trơn.
Ở Đức vào cuối những năm 70 của thế kỷ XX, có một giai thoại: “Tôi bán NSU, tôi sẽ tặng thêm hai bánh xe, một đèn pha và 18 động cơ dự phòng trong tình trạng tốt”.
- RCV - động cơ đốt trong, hệ thống phân phối khí được thực hiện nhờ chuyển động của pít-tông, chuyển động qua lại, luân phiên đi qua các đường ống vào và ra.
Động cơ đốt trong kết hợp
- - Động cơ đốt trong, là sự kết hợp của máy piston và máy lưỡi (tuabin, máy nén), trong đó cả hai máy đều tham gia một cách tương đối vào việc thực hiện quá trình làm việc. Một ví dụ về động cơ đốt trong kết hợp là động cơ piston có nạp tuabin khí (tăng áp). Một đóng góp lớn cho lý thuyết về động cơ liên hợp là của kỹ sư Liên Xô, Giáo sư A. N. Shelest.
Tăng áp
Loại động cơ kết hợp phổ biến nhất là động cơ tăng áp piston. Tăng áp hoặc một bộ tăng áp (TK, TN) là bộ tăng áp được thiết lập trong chuyển động khí thải ... Nó có tên từ từ "tuabin" (fr. Tuabin từ turbo - xoáy, vòng quay trong tiếng Latinh). Thiết bị này bao gồm hai phần: bánh xe rôto tuabin dẫn động bằng khí thải, và máy nén ly tâm cố định ở hai đầu đối diện của trục chung. Phản lực của chất lỏng làm việc (trong trường hợp này là khí thải) tác động lên các cánh được cố định xung quanh chu vi của rôto, và đặt chúng chuyển động cùng với trục, được chế tạo thành một mảnh với rôto tuabin làm bằng hợp kim gần thép hợp kim ... Trên trục, ngoài rôto tuabin còn có rôto máy nén làm bằng hợp kim nhôm, khi trục quay sẽ cho phép “bơm” không khí có áp suất vào các xi lanh động cơ đốt trong. Do đó, do kết quả của hành động khí thải rôto tuabin, trục và rôto máy nén đồng thời quay trên các cánh tuabin. Việc sử dụng bộ tăng áp kết hợp với bộ làm mát liên động (intercooler) cho phép cung cấp không khí đậm đặc hơn cho các xi-lanh của động cơ đốt trong (trong các động cơ tăng áp hiện đại thì sơ đồ này được sử dụng). Thường thì khi dùng turbo tăng áp trong động cơ, người ta nói đến tuabin mà không nói đến máy nén. Bộ tăng áp là một mảnh. Bạn không thể sử dụng năng lượng của khí thải để cung cấp hỗn hợp không khí dưới áp suất cho các xi lanh của động cơ đốt trong chỉ sử dụng tuabin. Phun được cung cấp bởi bộ phận đó của bộ tăng áp, được gọi là máy nén.
Trên chạy không tảiở số vòng quay thấp, bộ tăng áp tạo ra ít công suất và được dẫn động bởi một lượng nhỏ khí thải. Trong trường hợp này, bộ tăng áp hoạt động không hiệu quả và động cơ hoạt động giống như khi không tăng áp. Khi động cơ cần một công suất lớn hơn nhiều, vòng tua máy cũng như khoảng cách bướm ga sẽ tăng lên. Miễn là có đủ khí thải để làm quay tuabin, thì sẽ có nhiều không khí được hút qua ống nạp.
Tăng áp cho phép động cơ chạy hiệu quả hơn vì turbo sử dụng năng lượng từ khí thải mà nếu không (hầu hết) sẽ bị lãng phí.
Tuy nhiên, có một giới hạn công nghệ được gọi là "độ trễ tăng áp" ("turbo delay") (ngoại trừ động cơ có hai bộ tăng áp - một nhỏ và một lớn, khi TK nhỏ hoạt động ở tốc độ thấp và một lớn ở tốc độ cao, cùng cung cấp lượng hỗn hợp không khí cần thiết vào xi lanh. hoặc khi sử dụng tuabin có dạng hình học thay đổi, đua xe thể thao cũng sử dụng gia tốc cưỡng bức của tuabin bằng cách sử dụng hệ thống thu hồi năng lượng). Công suất động cơ không tăng ngay lập tức do tốc độ của động cơ sẽ mất một thời gian nhất định, có một số quán tính, và cũng do khối lượng của tua bin càng lớn thì thời gian quay vòng và tạo áp suất càng nhiều. đủ để tăng công suất động cơ. Ngoài ra, áp suất khí thải tăng lên làm cho khí thải truyền một phần nhiệt của chúng. bộ phận cơ khí (Vấn đề này được các nhà sản xuất động cơ đốt trong của Nhật Bản và Hàn Quốc giải quyết một phần bằng cách lắp thêm hệ thống làm mát cho bộ tăng áp. chất chống đông).
Các chu kỳ hoạt động của động cơ đốt trong piston
Động cơ phản lực đốt trong được phân loại theo số lần hành trình trong chu trình làm việc tại hai nét và bốn thì.
Chu kỳ làm việc của động cơ đốt trong bốn kỳ thực hiện hai vòng quay hoàn toàn hoặc quay 720 độ trục khuỷu (PKV), bao gồm bốn biện pháp riêng biệt:
- đầu vào,
- tính phí nén,
- đột quỵ làm việc và
- nhả (xả).
Thay đổi hành trình làm việc được cung cấp bởi một cơ cấu phân phối khí đặc biệt, thường được thể hiện bằng một hoặc hai trục cam, một hệ thống van đẩy và van trực tiếp cung cấp sự thay đổi pha. Một số động cơ đốt trong đã sử dụng ống lót (Ricardo) cho mục đích này, có các cổng nạp và / hoặc xả. Trong trường hợp này, sự liên lạc của khoang xi lanh với các ống góp được đảm bảo bằng chuyển động quay và hướng tâm của ống bọc, các cửa sổ mở ra kênh mong muốn. Do tính chất đặc thù của động lực học khí - quán tính của khí, thời gian xuất hiện của gió khí, hành trình nạp, hành trình công suất và xả trong một chu kỳ bốn kỳ thực trùng nhau, điều này được gọi là thời gian van chồng chéo... Tốc độ làm việc của động cơ càng cao thì độ trùng pha càng lớn và càng lớn thì mômen của động cơ cháy ở tốc độ thấp càng giảm. Vì vậy, trong các động cơ đốt trong hiện đại ngày càng sử dụng nhiều thiết bị cho phép thay đổi thời gian van trong quá trình hoạt động. Động cơ có điều khiển van điện từ ( Xe BMW , Mazda). Cũng có sẵn các động cơ với tỷ số nén thay đổi (SAAB AB), mang lại hiệu suất linh hoạt hơn.
Động cơ hai kỳ có nhiều cách bố trí và nhiều hệ thống thiết kế. Nguyên tắc cơ bản của bất kỳ động cơ hai kỳ nào là piston thực hiện các chức năng của bộ phận phân phối khí. Chu trình làm việc, nói một cách chính xác, bao gồm ba bước: một chu trình làm việc kéo dài từ trung tâm chết hàng đầu (TDC) lên đến 20-30 độ so với đáy trung tâm chết (NMT), nhặt rác, kết hợp hiệu quả giữa nạp và xả, và nén, kéo dài từ 20-30 độ sau BDC đến TDC. Theo quan điểm của động lực học chất khí, sự tẩy rửa là liên kết yếu của chu trình hai kỳ. Một mặt, không thể đảm bảo tách hoàn toàn điện tích tươi và khí thải, do đó, việc thất thoát hỗn hợp tươi theo nghĩa đen bay ra ngoài đường ống xả là không thể tránh khỏi (nếu động cơ đốt trong là diesel, chúng ta đang nói đến sự thất thoát khí), mặt khác, hành trình làm việc không kéo dài nửa doanh thu, nhưng ít hơn, tự nó làm giảm Hiệu quả ... Đồng thời, thời gian của quá trình trao đổi khí cực kỳ quan trọng mà ở động cơ bốn kỳ chiếm một nửa chu kỳ làm việc cũng không thể tăng lên. Động cơ hai kỳ có thể hoàn toàn không có hệ thống phân phối khí. Tuy nhiên, nếu chúng ta không nói đến động cơ giá rẻ được đơn giản hóa, thì động cơ hai kỳ phức tạp hơn và đắt hơn do bắt buộc phải sử dụng quạt gió hoặc hệ thống điều áp, mật độ nhiệt tăng lên của CPG đòi hỏi nhiều vật liệu đắt tiền hơn cho piston, vòng đệm và ống lót xi lanh. Việc thực hiện các chức năng của bộ phận phân phối khí bởi piston bắt buộc phải có chiều cao của nó không nhỏ hơn hành trình piston + chiều cao của các cổng thanh lọc, điều này là không quan trọng ở xe mô tô, nhưng đáng kể làm cho piston nặng hơn ngay cả ở công suất tương đối thấp. Khi công suất được đo bằng hàng trăm sức ngựa , sự gia tăng khối lượng piston trở thành một yếu tố rất nghiêm trọng. Sự ra đời của ống bọc phân phối hành trình dọc trong động cơ Ricardo là một nỗ lực nhằm giảm kích thước và trọng lượng của piston. Hệ thống hóa ra phức tạp và tốn kém để thực hiện, ngoại trừ ngành hàng không, những động cơ như vậy không được sử dụng ở bất kỳ nơi nào khác. Van xả (với van một dòng thổi) có cường độ nhiệt gấp đôi so với van xả của động cơ bốn thì và điều kiện tản nhiệt kém hơn, và ghế của chúng tiếp xúc trực tiếp với khí thải lâu hơn.
Đơn giản nhất về trình tự công việc và phức tạp nhất về thiết kế là hệ thống Koreyvo , đại diện ở Liên Xô và ở Nga, chủ yếu là động cơ diesel đầu máy xe lửa của dòng D100 và động cơ diesel xe tăng KhZTM. Động cơ này là một hệ thống trục đôi đối xứng với các piston phân kỳ, mỗi piston được kết nối với trục khuỷu riêng của nó. Như vậy, động cơ này có hai trục khuỷu, được đồng bộ cơ khí; cái nối với piston xả nằm trước cửa nạp 20-30 độ. Do tiến bộ này, chất lượng của quá trình xả đáy được cải thiện, trong trường hợp này là dòng chảy trực tiếp và việc nạp đầy xi lanh được cải thiện, vì ở cuối quá trình xả đáy, các cổng xả đã được đóng lại. Trong những năm 30 - 40 của thế kỷ XX, các phương án với các cặp piston phân kỳ đã được đề xuất - hình thoi, hình tam giác; có những động cơ diesel của máy bay với ba piston phân kỳ hướng tâm, trong đó hai ống hút và một ống xả. Trong những năm 20 Người bỏ rác đề xuất một hệ thống trục đơn với các thanh nối dài được kết nối với các chốt piston phía trên bằng các tay quay đặc biệt; pít-tông phía trên truyền lực tới trục khuỷu bằng một cặp thanh nối dài và có ba khuỷu trục trên mỗi xi lanh. Trên cánh tay của rocker cũng là những pít-tông vuông của các hốc thanh tẩy. Động cơ hai thì với các piston phân kỳ của bất kỳ hệ thống nào về cơ bản đều có hai nhược điểm: thứ nhất, chúng rất phức tạp và có kích thước, thứ hai, các piston và ống xả ở khu vực cửa sổ xả có ứng suất nhiệt đáng kể và có xu hướng quá nhiệt. Các vòng piston xả cũng bị ứng suất nhiệt, dễ bị co ngót và mất tính đàn hồi. Những tính năng này làm cho việc thiết kế những động cơ như vậy trở thành một nhiệm vụ không hề nhỏ.
Động cơ van dòng chảy trực tiếp được trang bị trục cam và van xả. Điều này làm giảm đáng kể các yêu cầu về vật liệu và thiết kế của CPG. Việc nạp vào thông qua các cửa sổ trong ống lót xi lanh, được mở bởi piston. Đây là cách lắp ráp động cơ diesel hai kỳ hiện đại nhất. Khu vực cửa sổ và lớp lót ở phía dưới trong nhiều trường hợp được làm mát bằng không khí tích điện.
Trong trường hợp một trong những yêu cầu chính đối với động cơ là giảm chi phí, các kiểu thổi cửa sổ theo đường viền buồng quay khác nhau được sử dụng - vòng lặp, vòng quay trở lại (bộ làm lệch hướng) trong các sửa đổi khác nhau. Để cải thiện các thông số động cơ, một loạt các kỹ thuật thiết kế được sử dụng - chiều dài của các kênh nạp và xả có thể thay đổi, số lượng và vị trí của các kênh rẽ nhánh có thể thay đổi, ống cuốn, ống cắt khí quay, tấm lót và cửa chớp được sử dụng để thay đổi chiều cao của cửa sổ (và theo đó, thời điểm bắt đầu hút và xả). Hầu hết các động cơ này đều được làm mát bằng không khí thụ động. Nhược điểm của chúng là chất lượng trao đổi khí tương đối thấp và mất hỗn hợp dễ cháy trong quá trình thổi; khi có nhiều xi lanh, các phần của buồng quay phải được tách ra và bịt kín, việc thiết kế trục khuỷu trở nên phức tạp hơn và tốn kém hơn.
Các đơn vị bổ sung cần thiết cho động cơ đốt trong
Nhược điểm của động cơ đốt trong là nó phát triển cao nhất quyền lực chỉ trong một phạm vi vòng quay hẹp. Do đó, một thuộc tính tích hợp của động cơ đốt trong là quá trình lây truyền ... Chỉ trong một số trường hợp (ví dụ: trong máy bay), bạn có thể làm mà không cần một đường truyền phức tạp. Ý tưởng đang từng bước chinh phục thế giới xe điện , trong đó động cơ luôn chạy ở mức tối ưu.
Ngoài ra, động cơ đốt trong cần có hệ thống động lực (để cung cấp nhiên liệu và không khí - điều chế hỗn hợp nhiên liệu-không khí), hệ thống ống xả (để loại bỏ khí thải), bạn cũng không thể làm gì nếu không có hệ thống bôi trơn (được thiết kế để giảm lực ma sát trong các cơ cấu động cơ, bảo vệ các bộ phận động cơ khỏi bị ăn mòn và cùng với hệ thống làm mát để duy trì điều kiện nhiệt tối ưu), hệ thống làm mát (để duy trì điều kiện nhiệt tối ưu động cơ), hệ thống khởi động (các phương pháp khởi động được sử dụng: khởi động điện, với sự trợ giúp của động cơ khởi động phụ, khí nén, với sự trợ giúp của sức người), hệ thống đánh lửa (để đánh lửa hỗn hợp nhiên liệu-không khí, được sử dụng trong động cơ đánh lửa cưỡng bức).
Sản xuất tính năng công nghệ
Yêu cầu cao được đặt ra đối với việc gia công các lỗ trên các bộ phận khác nhau, bao gồm các bộ phận động cơ (lỗ đầu xi lanh (đầu xi lanh), ống lót xi lanh, lỗ đầu trục khuỷu và piston, lỗ bánh răng), v.v. Công nghệ chính xác cao được sử dụng mài và mài giũa.
Xem thêm
tại Wikimedia Commons | |
Động cơ đốt trong trên Wikinews |
- Hệ thống làm mát động cơ đốt trong
- Philippe Le Bon - người Pháp kỹ sư nhận trong 1801 năm bằng sáng chế cho động cơ đốt trong nén hỗn hợp khí và không khí.
- Động cơ piston quay (Động cơ Wankel)
NƯỚC ĐÁ là động cơ đốt trong các loại nhiên liệu trực tiếp bên trong chính đơn vị. Không giống như các loại động cơ khác, ICE bị tước đoạt: bất kỳ phần tử nào truyền nhiệt để chuyển hóa thêm thành năng lượng cơ học, quá trình chuyển đổi diễn ra trực tiếp từ quá trình đốt cháy nhiên liệu; nhỏ gọn hơn nhiều; có trọng lượng thấp so với các loại thiết bị khác có công suất tương đương; yêu cầu sử dụng một loại nhiên liệu nhất định với các đặc tính nghiêm ngặt về nhiệt độ cháy, mức độ bay hơi, số octan Vân vân.
Động cơ bốn kỳ được sử dụng trong ngành công nghiệp ô tô:
1. Cửa vào;
2. Nén;
3. Đột quỵ làm việc;
4.
Giải phóng.
Nhưng cũng có những phiên bản động cơ đốt trong hai kỳ, nhưng trong thế giới hiện đại, chúng được sử dụng hạn chế.
Trong bài viết này, chỉ các động cơ lắp trên ô tô sẽ được xem xét.
Các loại động cơ cho nhiên liệu được sử dụng
Động cơ xăng, như tên gọi của nó, chúng được sử dụng làm nhiên liệu cho công việc - xăng có trị số octan khác nhau và có hệ thống đánh lửa cưỡng bức hỗn hợp nhiên liệu bằng tia lửa điện.Chúng có thể được chia theo kiểu nạp vào bộ chế hòa khí và phun. Động cơ bộ chế hòa khí đã không còn được sản xuất do khó điều chỉnh, tiêu thụ cao xăng, trộn hỗn hợp nhiên liệu không hiệu quả và không phù hợp với hiện đại những yêu cầu về môi trường... Trong các động cơ như vậy, sự trộn hỗn hợp dễ cháy bắt đầu trong các buồng chế hòa khí và kết thúc dọc theo đường đi trong đường ống nạp.
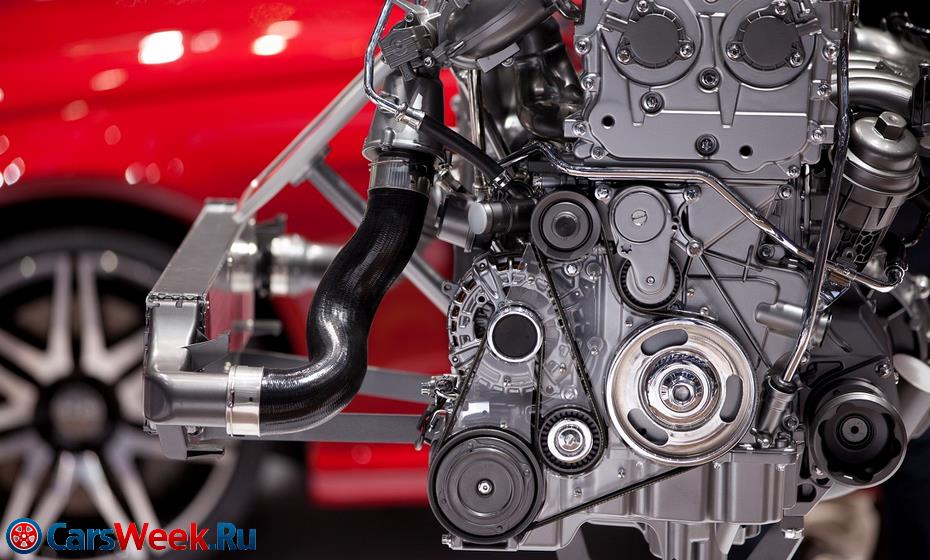
Các đơn vị phun đang phát triển với tốc độ nhanh chóng và hệ thống phun nhiên liệu đã được cải thiện theo từng thế hệ. Các kim phun đầu tiên có một "tiêm đơn" với một vòi phun duy nhất. Trên thực tế, đó là một sự hiện đại hóa động cơ chế hòa khí... Theo thời gian, trên hầu hết các đơn vị, hệ thống bắt đầu được sử dụng với các vòi phun riêng biệt cho mỗi xi lanh. Việc sử dụng kim phun trong hệ thống nạp giúp kiểm soát chính xác hơn tỷ lệ nhiên liệu và không khí ở các chế độ vận hành khác nhau của tổ máy, giảm tiêu hao nhiên liệu, tăng chất lượng hỗn hợp nhiên liệu, tăng công suất và tính thân thiện với môi trường của các tổ máy.
Kim phun hiện đại được lắp đặt trên các đơn vị điện có hệ thống phun trực tiếp nhiên liệu vào xi lanh có khả năng tạo ra một số lần phun nhiên liệu riêng biệt cho mỗi hành trình. Điều này cải thiện hơn nữa chất lượng của hỗn hợp nhiên liệu và tối đa hóa năng lượng trở lại từ lượng xăng được sử dụng. Tức là, tính kinh tế và hiệu suất của động cơ đã tăng lên nhiều hơn.

Đơn vị diesel - sử dụng nguyên tắc đánh lửa hỗn hợp dầu đi-e-zel và không khí khi bị đốt nóng do nén mạnh. Đồng thời, hệ thống đánh lửa cưỡng bức không được sử dụng trong các tổ máy diesel. Động cơ này có một số ưu điểm hơn động cơ xăng, trước hết là tiết kiệm nhiên liệu (tới 20%), có sức mạnh tương đối. Tiêu thụ ít nhiên liệu hơn do tỷ số nén trong xi lanh cao hơn, điều này cải thiện đặc tính đốt cháy và sản lượng năng lượng của hỗn hợp nhiên liệu, do đó, cần ít nhiên liệu hơn để đạt được kết quả tương tự. Ngoài ra, các đơn vị diesel không sử dụng van tiết lưu, giúp cải thiện luồng không khí vào bộ phận điện, giúp giảm tiêu hao nhiên liệu hơn nữa. Động cơ diesel phát triển nhiều mô-men xoắn hơn và ở tốc độ động cơ thấp hơn.
Không phải không có sai sót. Do tải trọng lên thành xi lanh tăng lên, các nhà thiết kế phải sử dụng vật liệu đáng tin cậy hơn và tăng kích thước của kết cấu (trọng lượng tăng và chi phí sản xuất cao hơn). Ngoài ra, hoạt động của động cơ diesel đơn vị năng lượng - kêu to do đặc điểm của nhiên liệu đánh lửa. Và khối lượng các bộ phận tăng lên không cho phép động cơ phát triển vòng quay cao cùng tốc độ với xăng và giá trị lớn nhất của số vòng quay trục khuỷu thấp hơn đơn vị xăng.
Một loại động cơ đốt trong theo thiết kế
Hệ thống truyền động hybrid
Loại xe này bắt đầu thịnh hành trong những năm gần đây. Nhờ hiệu quả tiết kiệm nhiên liệu và tăng sức mạnh tổng thể của xe nhờ kết hợp hai loại đơn vị Trên thực tế, thiết kế này đại diện cho hai đơn vị riêng biệt - một động cơ đốt trong nhỏ (thường là diesel) và một động cơ điện (hoặc một số động cơ điện) với pin sạc dung lượng lớn.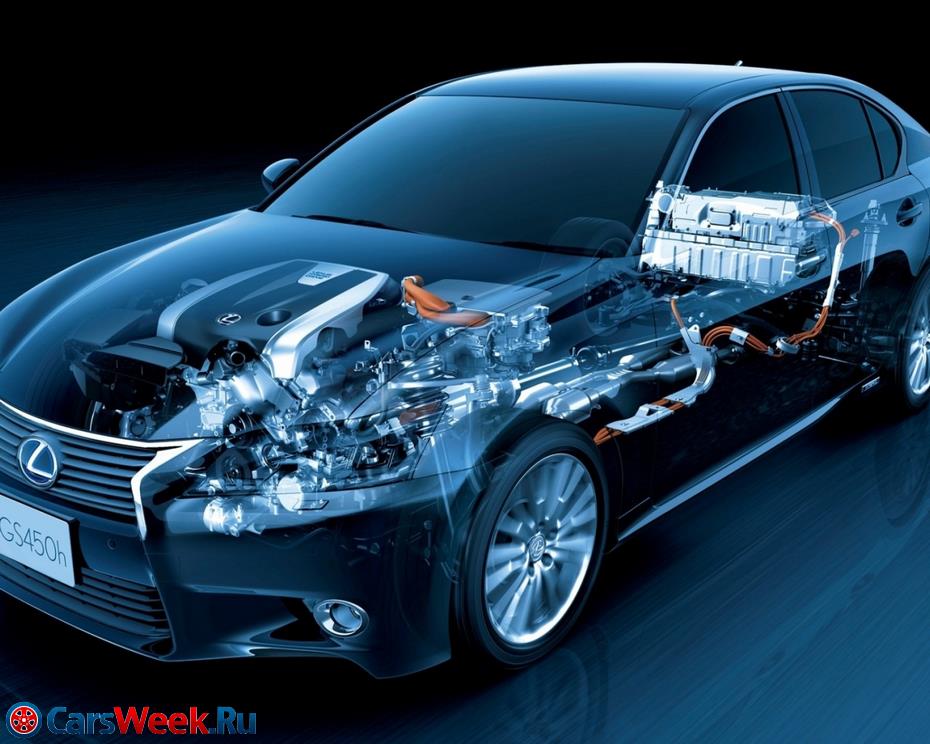
Ưu điểm của sự kết hợp thể hiện ở khả năng kết hợp năng lượng của hai tổ máy trong quá trình tăng tốc, hoặc sử dụng riêng từng loại động cơ tùy theo nhu cầu. Ví dụ, khi lái xe trong thành phố tắc đường, chỉ có động cơ điện mới hoạt động được, giúp tiết kiệm nhiên liệu diesel. Khi lái xe trên đường quê, động cơ đốt trong hoạt động cứng cáp hơn, mạnh mẽ hơn và có bộ dự trữ năng lượng lớn.
Đồng thời, pin đặc biệt dành cho động cơ điện có thể được sạc lại từ máy phát điện hoặc sử dụng hệ thống thu hồi trong quá trình phanh, giúp tiết kiệm không chỉ nhiên liệu mà còn tiết kiệm điện năng cần thiết để sạc pin.
Động cơ piston quay
Động cơ piston quay được chế tạo theo kế hoạch độc đáo chuyển động của piston-rôto, chuyển động bên trong xi lanh không dọc theo đường chuyển động qua lại mà quanh trục của nó. Điều này là do thiết kế piston hình tam giác đặc biệt và sự sắp xếp đặc biệt của đầu vào và đầu ra trong xi lanh.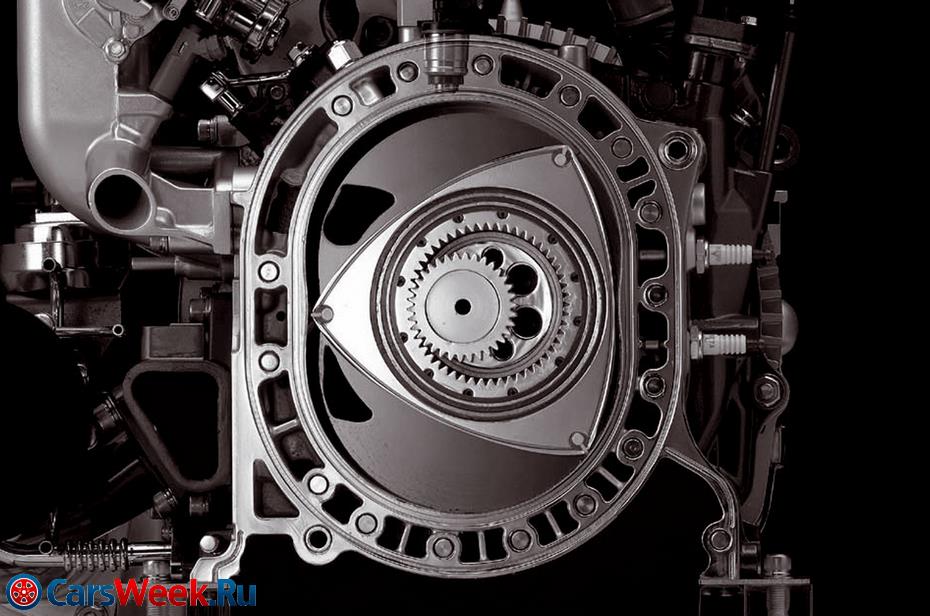
Nhờ thiết kế này, động cơ tăng tốc nhanh, làm tăng đặc tính động học của xe. Nhưng với sự phát triển của thiết kế ICE cổ điển, động cơ Wankel bắt đầu mất dần tính liên quan do những hạn chế trong thiết kế. Nguyên tắc chuyển động của piston không cho phép đạt được tỷ số nén cao của hỗn hợp nhiên liệu, loại trừ việc sử dụng nhiên liệu diesel. Và một nguồn lực nhỏ, sự phức tạp của việc bảo trì và sửa chữa, cũng như yếu hiệu suất môi trường không cho phép các hãng xe phát triển theo hướng này.
Các loại đơn vị năng lượng theo cách bố trí
Do yêu cầu giảm trọng lượng và kích thước, cũng như việc bố trí số lượng piston lớn hơn trong một đơn vị, đã dẫn đến sự xuất hiện của các loại động cơ về cách bố trí.Động cơ nội tuyến

Động cơ trong dòng là phiên bản cổ điển nhất của khối động cơ. Trong đó tất cả các piston và xylanh đều nằm trên một hàng. Đồng thời, động cơ hiện đại có bố trí thẳng hàng chứa không quá sáu xi lanh. Nhưng nó là sáu xi lanh động cơ trong dòng, có hiệu suất tốt nhất trong việc cân bằng độ rung trong quá trình hoạt động. Hạn chế duy nhất là chiều dài đáng kể của động cơ, so với các cách bố trí khác.
Động cơ hình chữ V
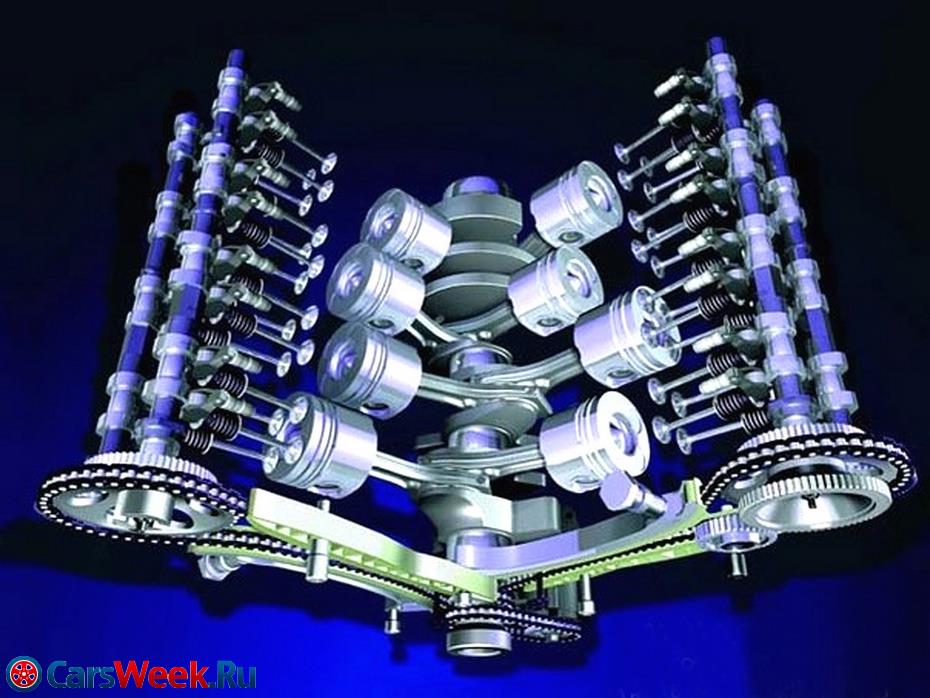
Những động cơ này xuất hiện là kết quả của mong muốn của các nhà thiết kế nhằm giảm kích thước của động cơ và yêu cầu đặt nhiều hơn sáu piston trong một khối. Trong các động cơ này, các xi lanh nằm trong các mặt phẳng khác nhau. Trực quan, sự sắp xếp của các hình trụ tạo thành chữ "V", do đó có tên. Góc giữa hai hàng được gọi là góc khum, và rất khác nhau, chia loại này động cơ thành các nhóm con.
Động cơ boxer
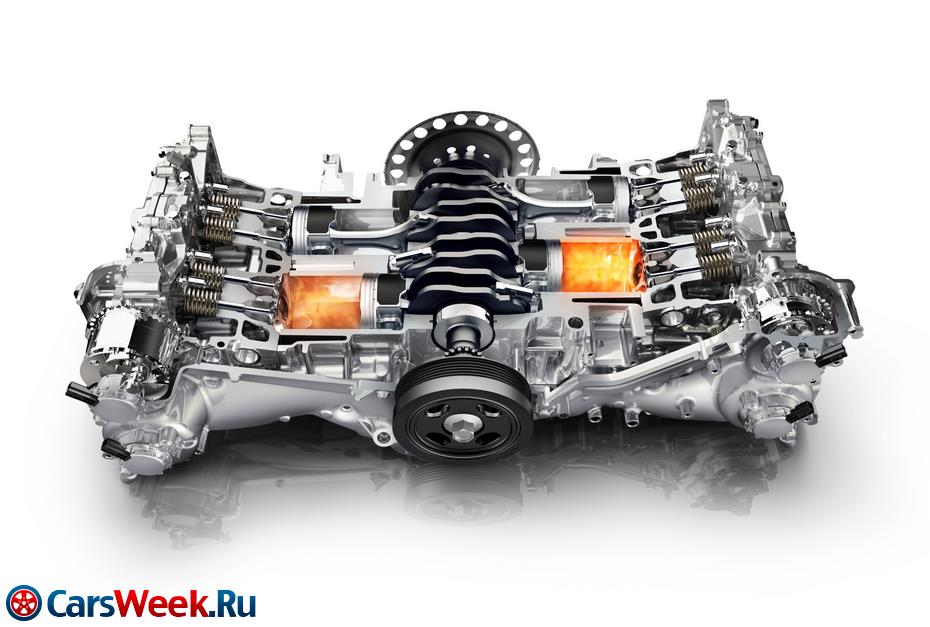
Động cơ Boxer, có góc tối đa khum 180 độ. Điều đó cho phép các nhà thiết kế giảm chiều cao đơn vị xuống kích thước tối thiểuvà phân phối tải trên trục khuỷu, tăng tài nguyên của nó.
Động cơ VR
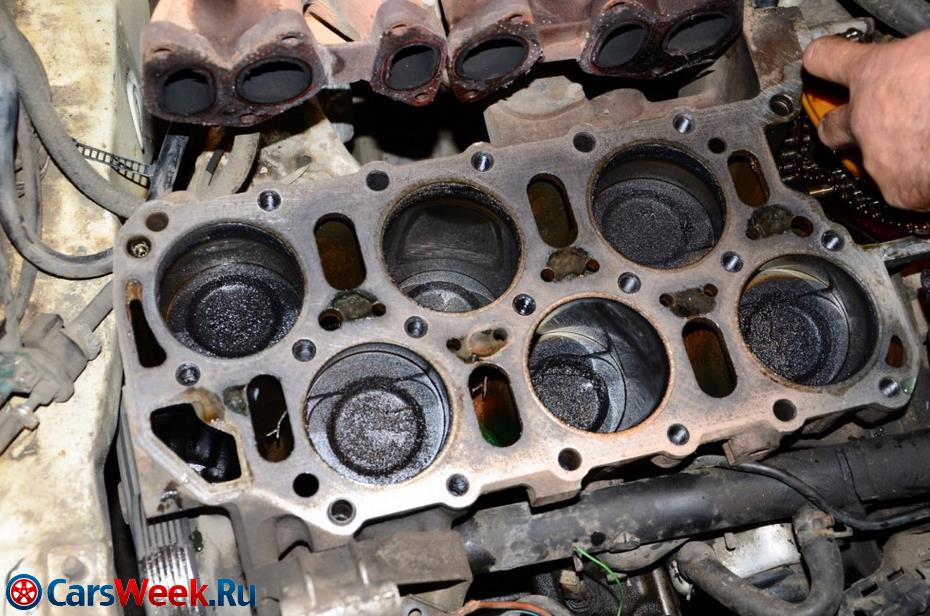
Nó là sự kết hợp của các thuộc tính của các đơn vị thẳng hàng và hình chữ V. Góc camber trong các động cơ như vậy đạt tới 15 độ, cho phép sử dụng một đầu xi lanh với cơ cấu điều phối van đơn.
Động cơ hình chữ W
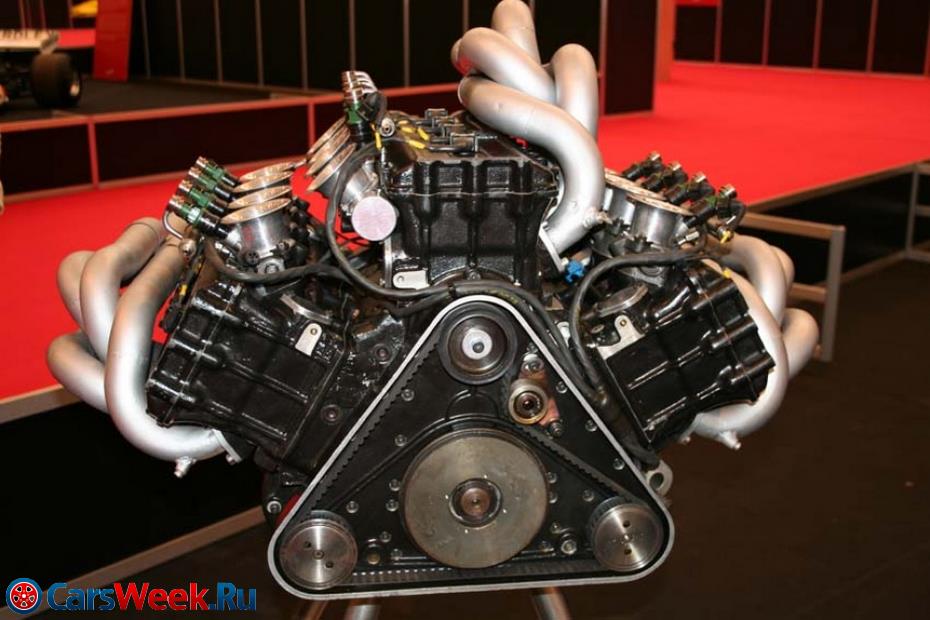
Một trong những thiết kế mạnh mẽ và "cực chất" của ICE. Chúng có thể có ba hàng trụ với góc khum lớn hoặc hai khối VR kết hợp. Ngày nay, động cơ tám và mười hai xi lanh đã trở nên phổ biến, nhưng thiết kế cho phép sử dụng nhiều xi lanh hơn.
Đặc điểm động cơ đốt trong
Sau khi xem xét nhiều thông tin về những chiếc xe khác nhau, bất kỳ người nào quan tâm sẽ thấy các thông số cơ bản nhất định của động cơ:Công suất của đơn vị công suất, được đo bằng hp. (hoặc kWh);
Mômen xoắn cực đại do đơn vị công suất phát triển, được đo bằng N / m;
Hầu hết những người đam mê ô tô chỉ chia sẻ các đơn vị điện năng bằng nguồn. Nhưng cách phân chia này không hoàn toàn đúng. Tất nhiên, một đơn vị 200 "ngựa" động cơ thích hợp 100 "con ngựa" trên một chiếc crossover hạng nặng. Và đối với một chiếc hatchback đô thị hạng nhẹ, động cơ 100 mã lực là đủ. Nhưng có một số sắc thái.
Công suất tối đa, được quy định trong tài liệu kỹ thuật, đạt được ở tốc độ trục khuỷu nhất định. Nhưng khi sử dụng xe trong môi trường đô thị, người lái ít khi nổ máy trên 2.500 vòng / phút. Do đó, thời gian hoạt động của máy càng lâu thì chỉ một phần của điện năng tiềm ẩn.
Nhưng, thường có những trường hợp trên đường. Khi cần tăng mạnh tốc độ để vượt, hoặc tránh trường hợp khẩn cấp... Nó là mô-men xoắn cực đại ảnh hưởng đến khả năng của đơn vị để nhanh chóng đạt được tốc độ và công suất cần thiết. Nói một cách đơn giản, mô-men xoắn ảnh hưởng đến động lực học của xe.
Cần lưu ý một sự khác biệt nhỏ giữa động cơ xăng và động cơ diesel. Động cơ xăng - cung cấp mô-men xoắn cực đại tại vòng tua trục khuỷu từ 3.500 đến 6.000 mỗi phút, và động cơ diesel có thể đạt thông số cực đại ở vòng tua máy thấp hơn. Do đó, nó dường như với nhiều người. Động cơ diesel đó mạnh hơn và "kéo" tốt hơn. Tuy nhiên, hầu hết các đơn vị mạnh nhất sử dụng nhiên liệu xăng, vì chúng có thể phát triển số vòng quay mỗi phút lớn hơn.
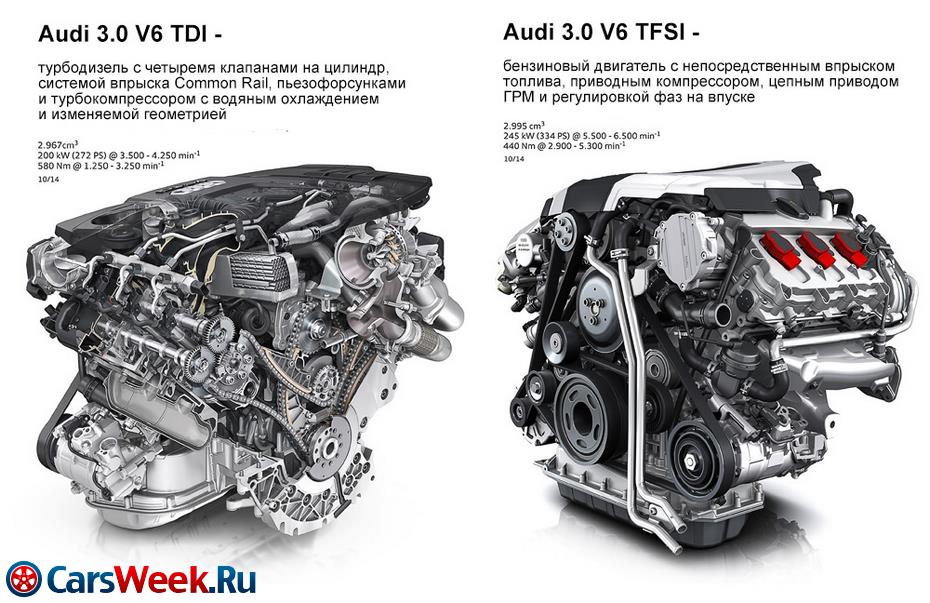
Và để hiểu chi tiết về thuật ngữ mô-men xoắn, bạn nên xem các đơn vị đo lường của nó: Newton nhân với mét. Nói cách khác, mô-men xoắn xác định lực mà piston đẩy lên trục khuỷu, từ đó truyền lực đến hộp số và cuối cùng là các bánh xe.
Ngoài ra, chúng ta có thể kể đến kỹ thuật mạnh mẽ, trong đó mô-men xoắn cực đại có thể đạt được ở tốc độ 1.500 vòng / phút. Về cơ bản, đây là những chiếc máy kéo, xe ben mạnh mẽ và một số loại xe chạy địa hình chạy bằng dầu diesel. Đương nhiên, những máy như vậy không cần phải quay động cơ lên \u200b\u200bđến vòng tua tối đa.

Dựa trên thông tin được cung cấp, chúng ta có thể kết luận rằng mômen xoắn phụ thuộc vào khối lượng của bộ nguồn, kích thước, kích thước của các bộ phận và trọng lượng của chúng. Các yếu tố này càng nặng thì mô-men xoắn càng chiếm ưu thế ở số vòng quay thấp. Động cơ diesel có nhiều mô-men xoắn hơn và số vòng quay của trục khuỷu thấp hơn (quán tính của trục khuỷu nặng hơn và các yếu tố khác không cho phép phát triển số vòng quay cao).
Công suất động cơ ô tô
Cần phải thừa nhận rằng công suất và mô-men xoắn là các thông số tương quan và phụ thuộc vào nhau. Công suất là một lượng công mà động cơ thực hiện trong một thời gian. Đổi lại, công của động cơ là mômen. Do đó, công suất được đặc trưng như lượng mô-men xoắn trên một đơn vị thời gian.Có một công thức nổi tiếng đặc trưng cho tỷ số giữa công suất và mô-men xoắn:
Công suất \u003d mô-men xoắn * vòng / phút / 9549
Kết quả là, chúng tôi nhận được giá trị công suất tính bằng kilowatt. Nhưng tự nhiên, nhìn vào các đặc điểm của ô tô, chúng ta quen với việc nhìn thấy các con số bằng "hp". Để chuyển đổi kilowatt sang hp bạn cần nhân giá trị kết quả với 1,36.